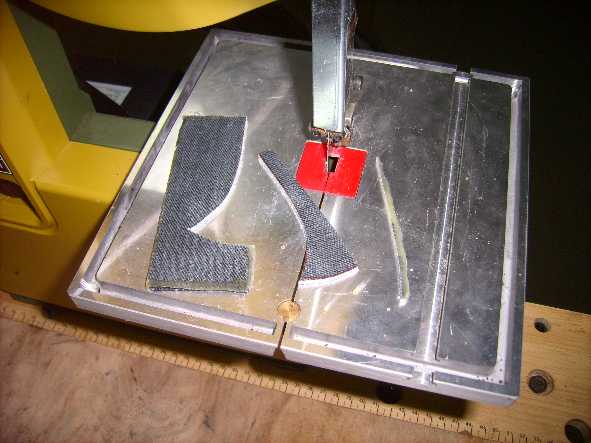
Découpe grossière à la scie à ruban de
l'entretoise en micarta maison.
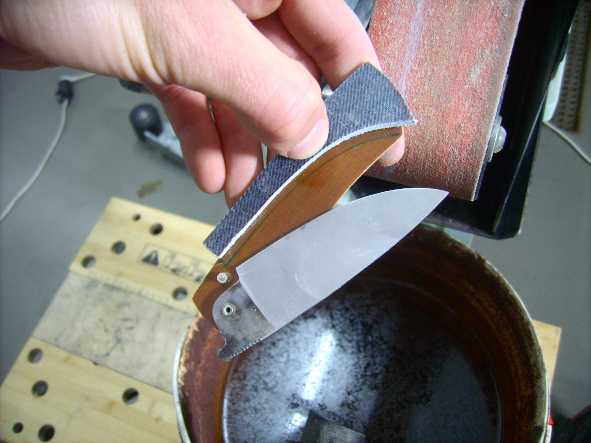
Façonnage plus précis de la face intérieure afin
qu'elle épouse bien la forme de la lame.
Non illustré
J'ai fini ladite face au papier abrasif à la main afin de faire
ressortir la couleur bleue . Ce devrait
être plus joli lorsqu'on regardera à l'intérieur.
Papiers P220, 400, 600, 800, 1200 et 2500 avec
de l'eau.
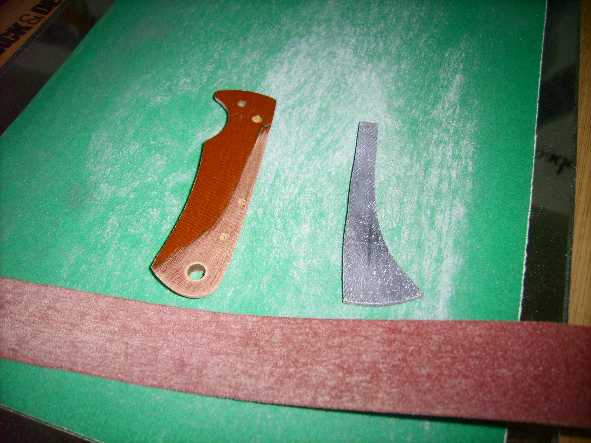
Rectification plane au P120 sur un mirroir de la face à coller
de l'entretoise.
Egrenage de la face opposée sur la plaquette

Acétone pour le dégraissage, colle époxy à
prise progressive et pince serre-joint.
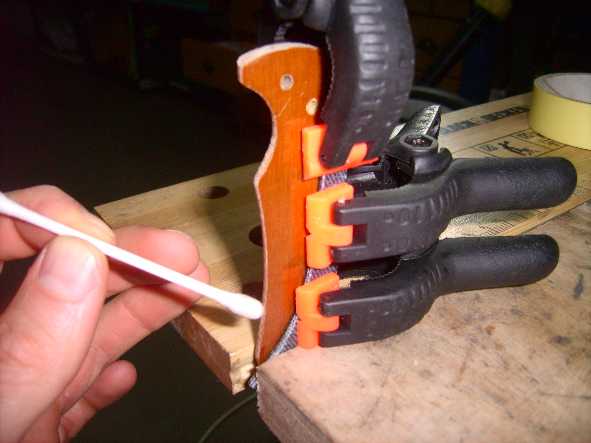
Après collage et mise sous presse, essuyage des excès de
colle au coton-tige+acétone.
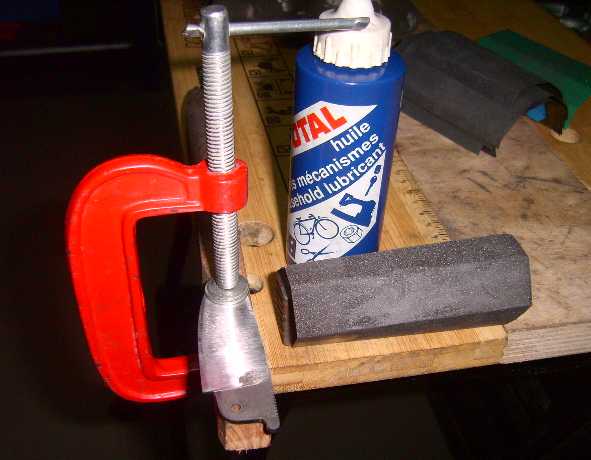
Ponçage jusqu'à P400 des faces parallèles autour
du trou d'axe.
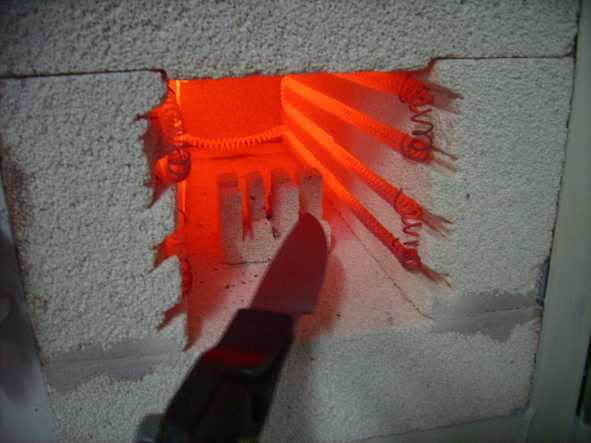
A force d'avoir forger l'acier sa structure garnulaire m'est inconnue.
Je la veux la plus fine possible
avec des grains sphéroïdaux et pas lamellaires. Je passe
l'acier au desssus de Acm afin de dissoudre
tout le carbone dans l'austénite. Un court instant pour
éviter aux grains de grossir. Bref j'enfourne
pour 5 min à 920°C.
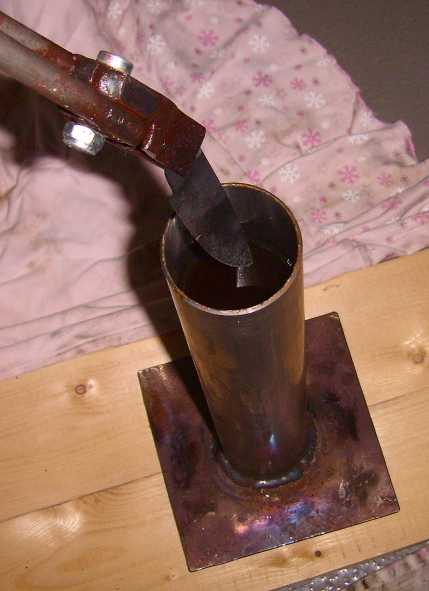
A présent pour obtenir des grains biens fins, une trempe sauvage
pendant
4 à 5 s dans de l'huile de colza préchauffée entre
50 et 80°C. Puis on
refroidit à l'air ambiant.
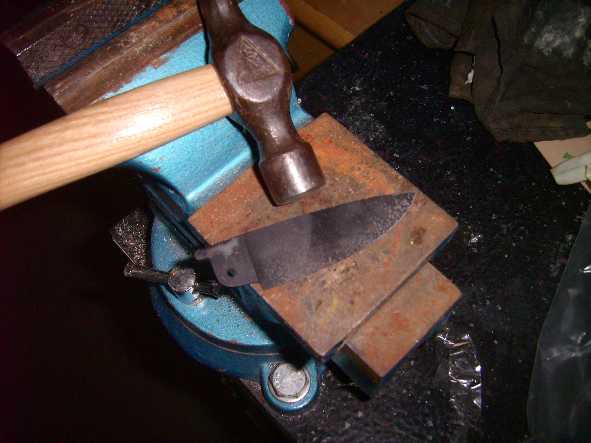
Parfois la lame se déforme mais on peut encore la redresser. Ici
elle était encore à 40..50°C. Parait
qu'il vaut mieux le faire vers 200°C mais je n'ai pas eu le temps.
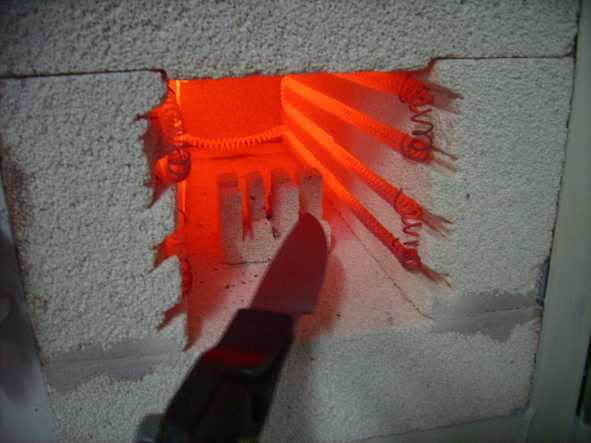
Le traitement suivant sert encore à affiner le grain: on chauffe
l'acier entre Acm et A1 (choix: 795°C)
et on le fait descendre progressivement sous A1 (choix: 680°C).
J'ai donc mis la lame 5 min à 795°C
et j'ai baissé le four de 20°C toutes les 4..5 min pour
atteindre 680°C. Cela s'est fait en 15..16 min.
Puis j'ai laissé la lame 5 min à 680°C.
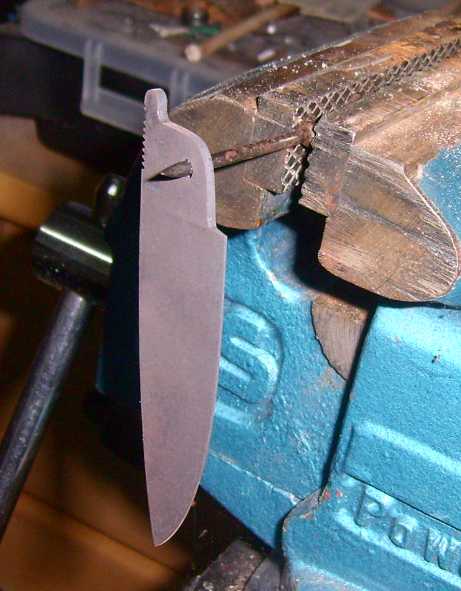
La lame est ensuite sortie du four et laissée à l'air
libre. Nous voilà théoriquement
avec des grains encore plus fins.
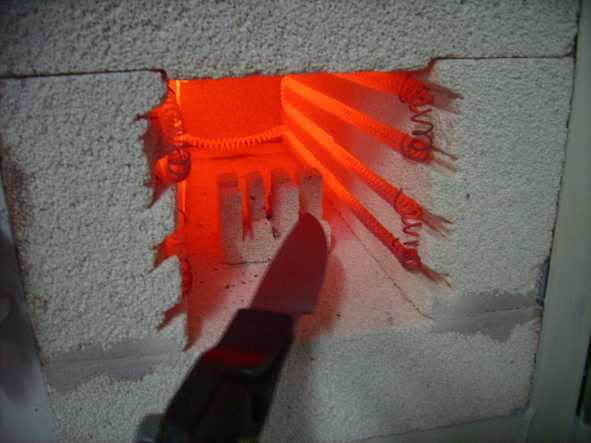
A présent la trempe. Je remets la lame 5 min à 835°C,
sa température dite d'austénisation.
J'ai choisi 835°C pour que l'acier final soit très dur avec
environ 0,8% de carbone dissous
aux joints de grains et qui formera la martensite et 0.2% de carbone
qui se combinera avec
du chrome afin de former des carbures qui donneront de la
résistance à l'usure.
(mes explications plus complètes en
page
22 au 27-JUL-21014)
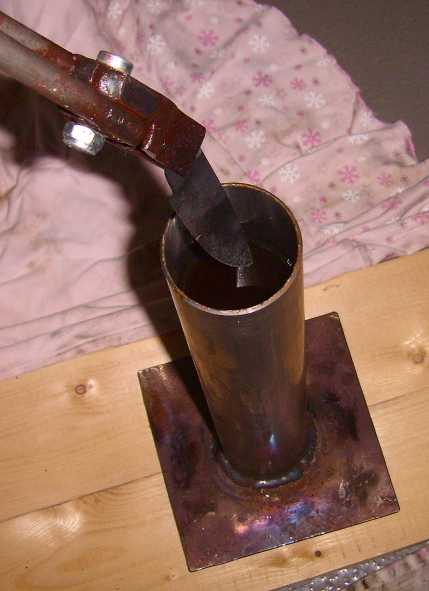
Puis on la refroidit dans de l'huile de colza préchauffée
à 50..80°C pendant
5..10 s. On laisse la lame se refroidir lentement ensuite. On est
"passée" sous
le "nez" perlitique suffisamment vite, ce qui se forme à
présent est forcément
de la martensite très dure. Comme sa densité est
différente, un refroidissement
final plus lent évite de trop grosses tensions dans l'acier.
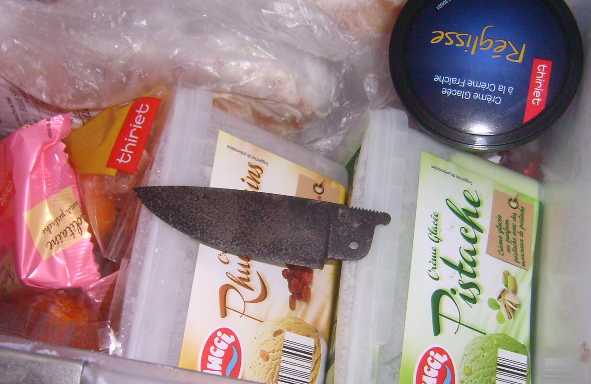
Afin de transformer un maximum d'austénite en martensite je
poursuis le refroidissement sous 0°C
dans mon congélateur vers -18°C pendant 30 min.
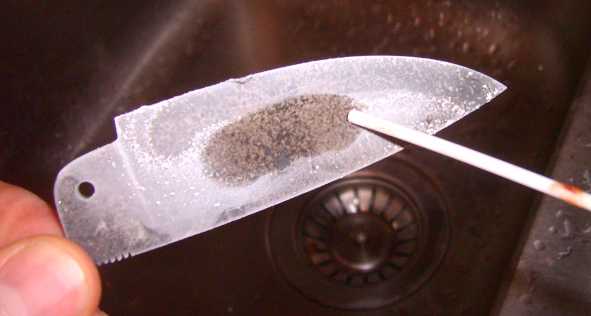
Et je descends encore à -52°C avec un spray
réfrigérant en ciblant le tranchant.
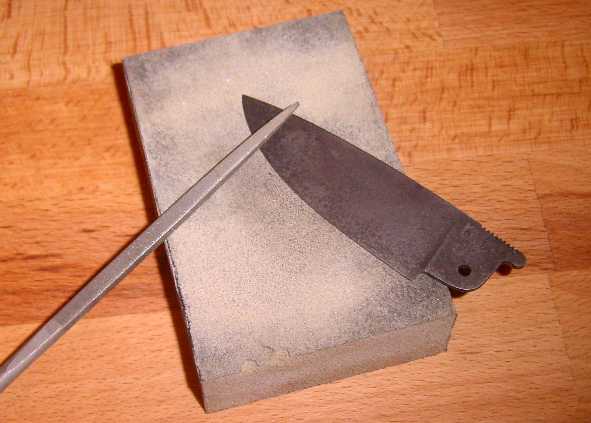
A présent je teste ma trempe avec une lime (qui doit glisser) et
je polis la lame pour voir plus tard
sa couleur de revenu (je vise un jaune paille)
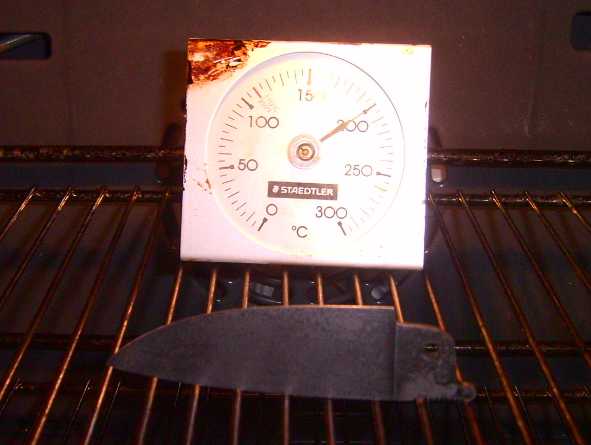
Un revenu en four de cuisine (dont on vérifiera la
température avec un thermomètre si possible
étalonné): 60 min à 200°C
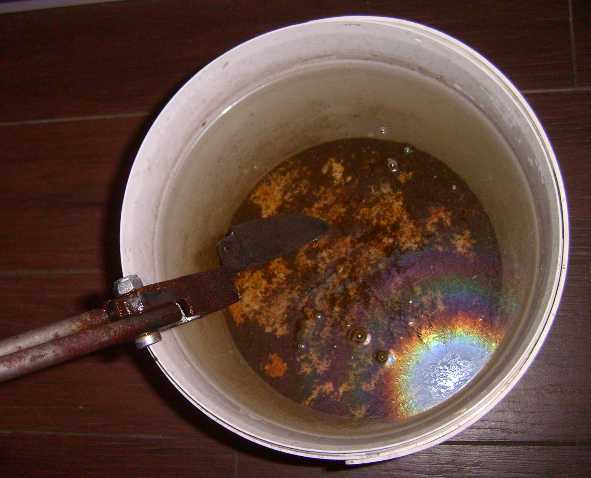
En sortie de four, pschiit dans de l'eau.
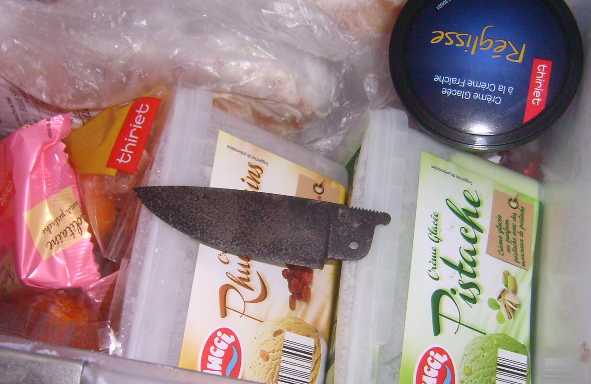
Et nouveau retour à -18°C. Cette fois pour la nuit et le
lendemain car je dois aussi dormir mais
30 min suffiraient selon moi. Il s'agit de transformer
l'austénite résiduelle en martensite fraiche qu'il
faudra à nouveau "adoucir" par un second revenu.
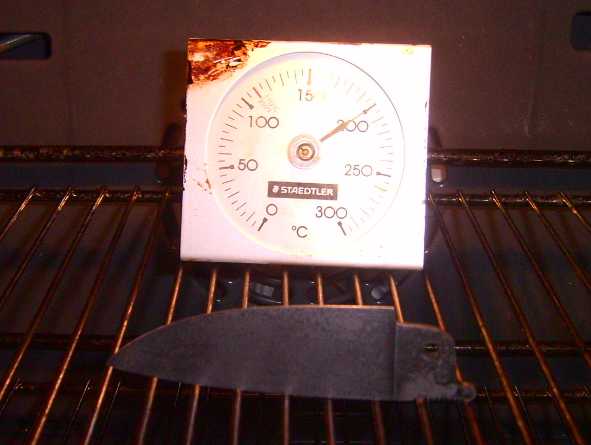
Second revenu: 60 min à 200°C.
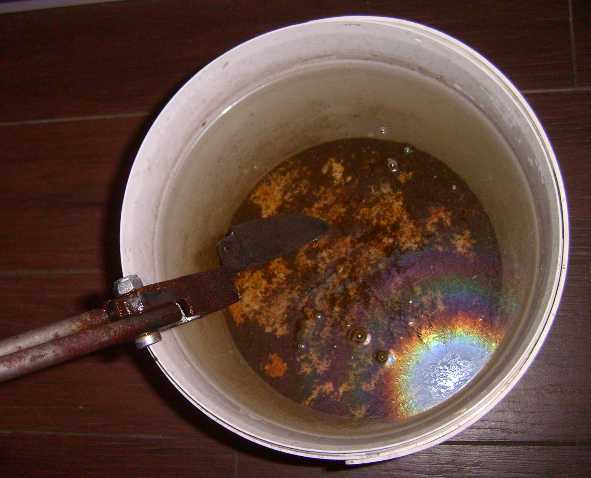
Nouveau refroidissement à l'eau.
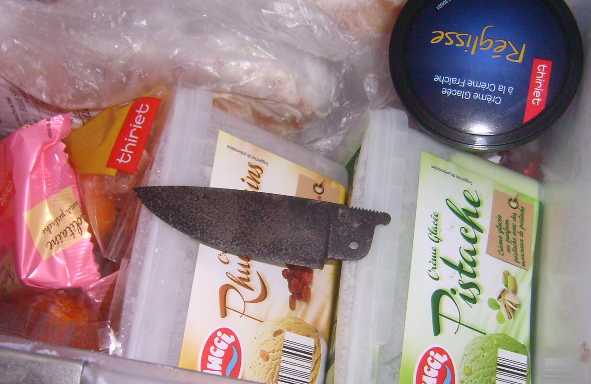
Et un dernier séjour à -18°C jusqu'au lendemain.
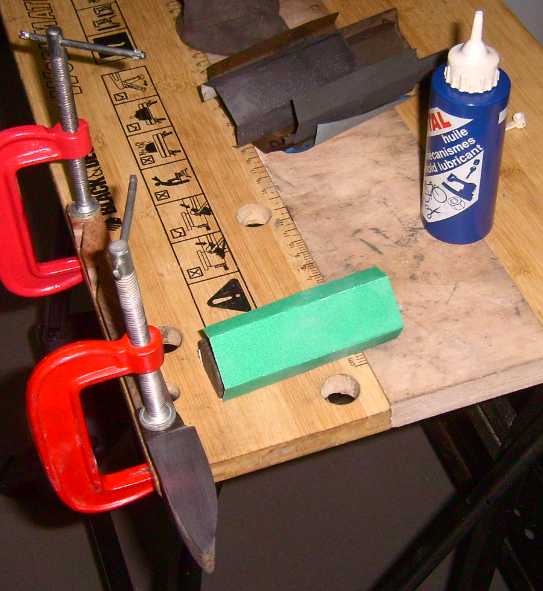
Reprise de l'émouture avec un ponçage fin à la
main et à l'huile à partir de P125 jusqu'à
P2500. La lame est un peu creusée (décarburation?) au
point qu'on dirait du brut de forge et
extrêment dure.
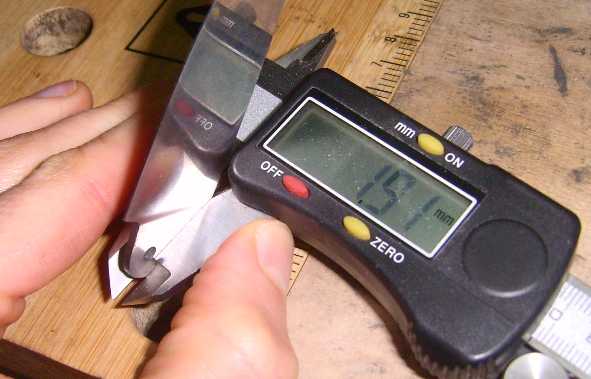
Mesure de l'épaisseur de la lame au point le plus épais
c-à-d au pivot: 1.91 mm environ.
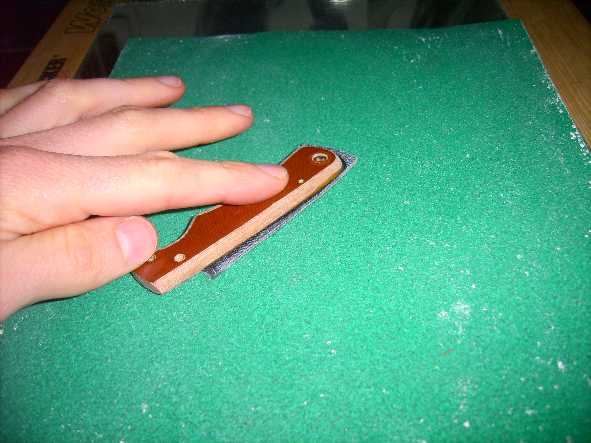
Ponçage de l'entretoise pour la descendre à la même
épaisseur.
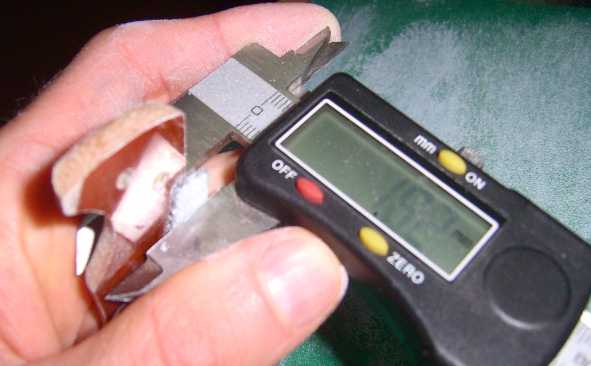
La voilà à 1.92 mm (la vérité c'est que mon
ponçage n'est pas parfaitement parallèle mais ça
ira)
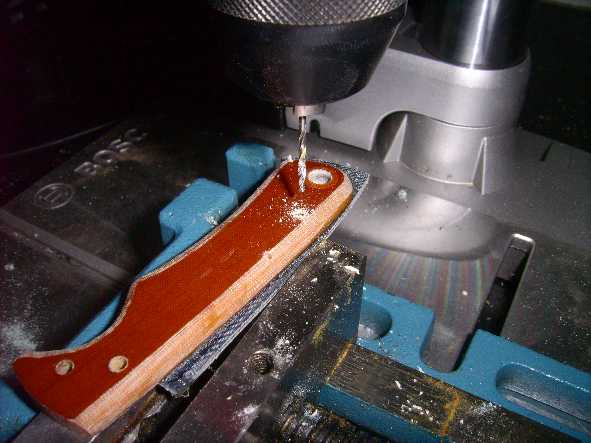
Perçage de l'entretoise en se servant de la plaquette comme
guide.
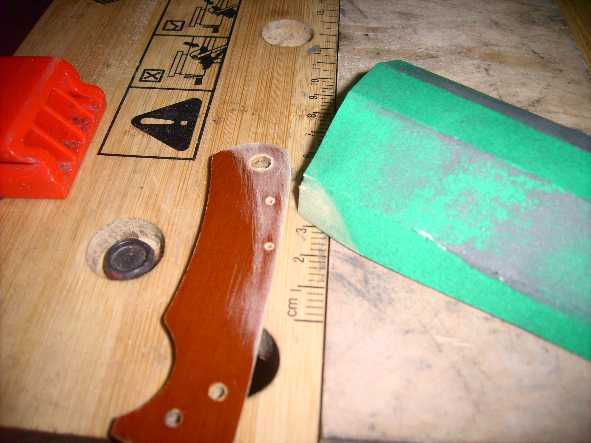
La zone à coller de l'autre plaquette est rendue rugueuse pour
une meilleure accroche de la colle.
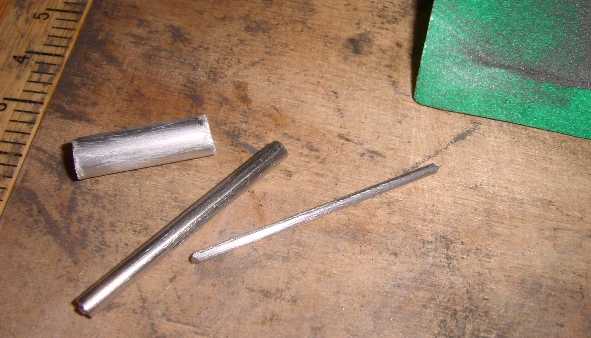
Idem pour tous les rivets, tube.
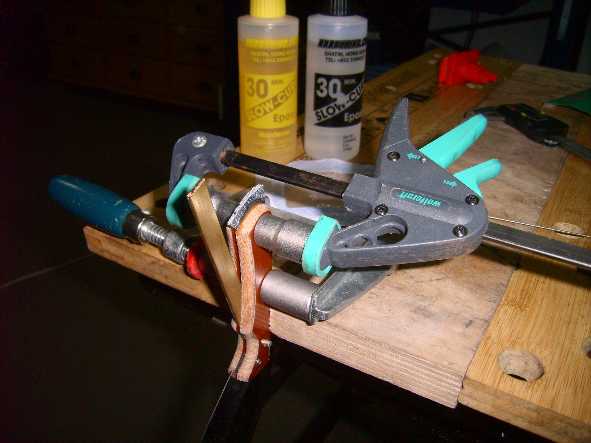
Avant le collage tout est nettoyé à l'alcool
ménager. Colle époxy à prise progressive et mise
sous
presse. Pour éviter que les pièces ne soient de travers,
j'ai glissé une cale de 2 mm entre les plaquettes.
La butée de lame n'est pas encore collée.
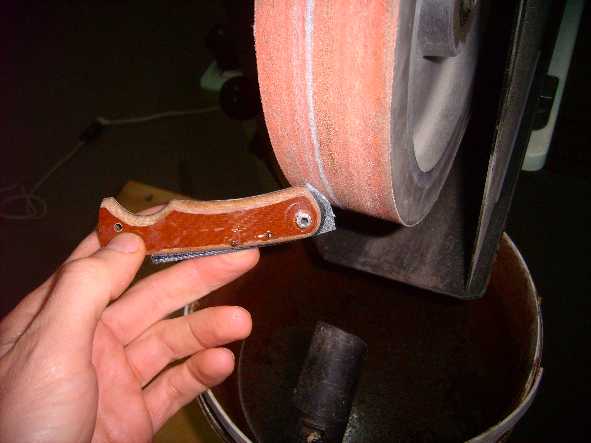
On ponce grossièrement tout ce qui dépasse au backstand.
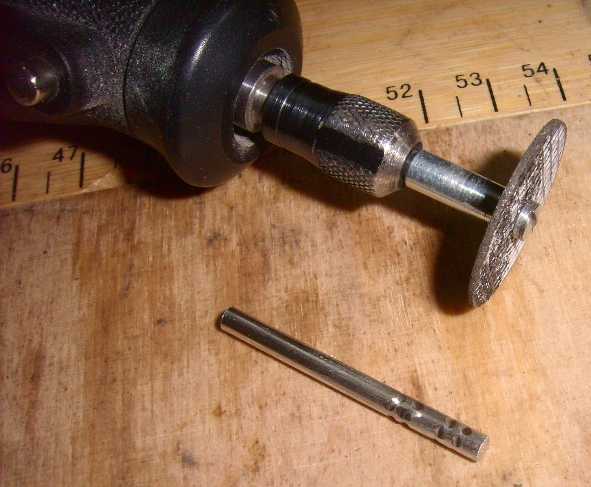
Ici je taille à la Dremel des poches de colle dans la
butée de lame pour augmenter l'efficacité de la
liaison par adhérence.
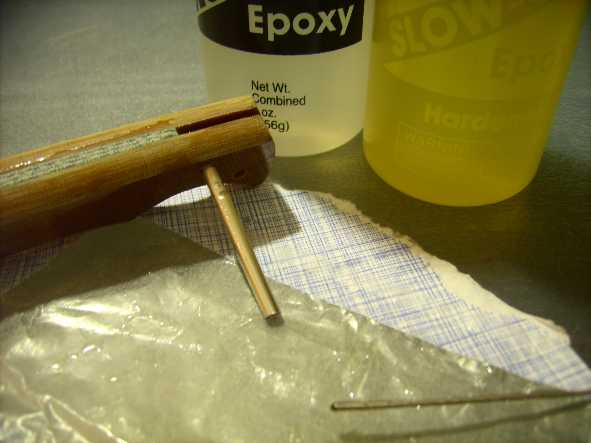
Collage de la butée de lame à l'époxy. J'ai fait
ce collage à part du premier afin de limiter au maximum
les débordements de colle autour de la butée au centre du
manche. Pour cela je place aussi la colle
dans le second trou et en face du premier mais sur l'axe. Si on met de
la colle dans le premier trou,
celle-ci sera repousser vers l'intérieur du manche comme le
ferait le piston d'une seringue.
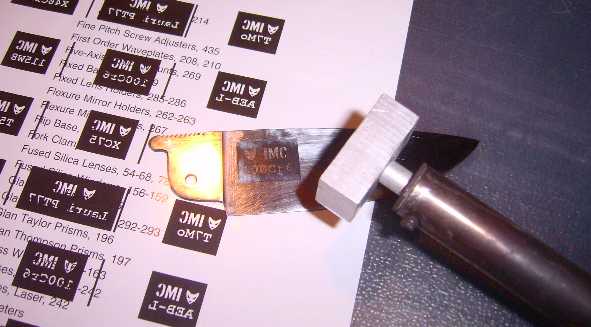
Transfert à chaud (avec un fer à souder modifié
maison) d'un masque d'un logo en toner imprimé
sur du papier glacé (
la technique
en détail)
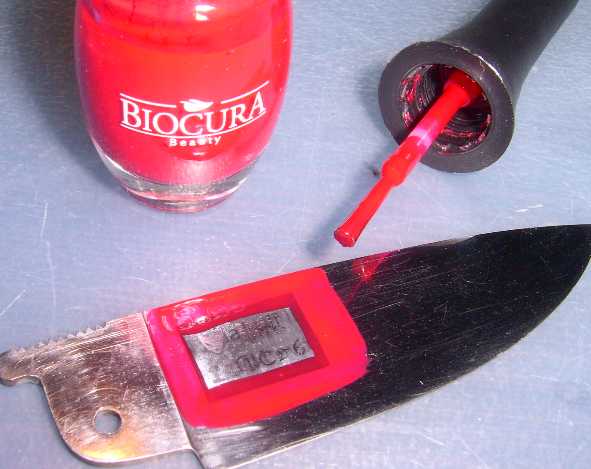
Amélioration de la protection de lame avec du vernis à
ongle.
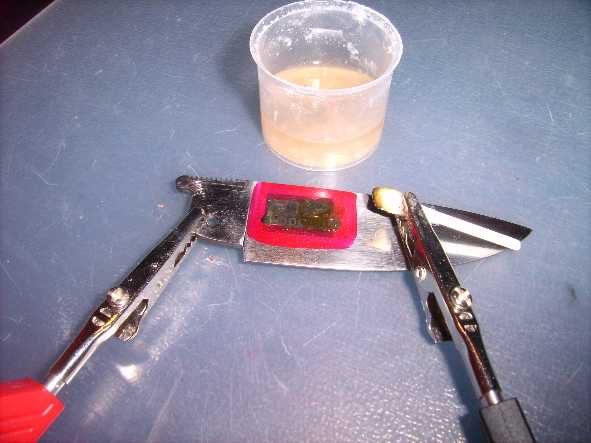
Sous 9 V et 250 mA en courant continu, la lame est mise au + tandis
qu'un coton-tige imbibé d'eau
salée en excès est mi au -. Il suffit de passer le
coton-tige sur le masque pour que du métal soit arraché
au niveau miscroscopique, pour migrer dans le coton.
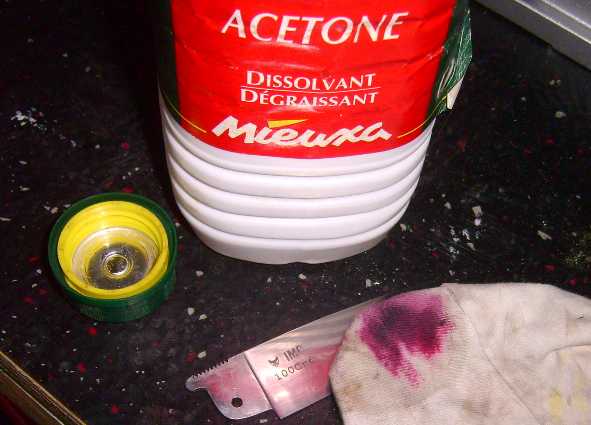
Nettoyage à l'acétone du toner et du vernis.
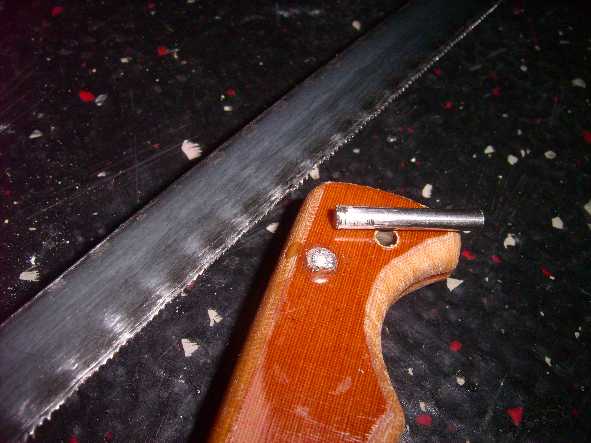
Sciage de la butée de lame.
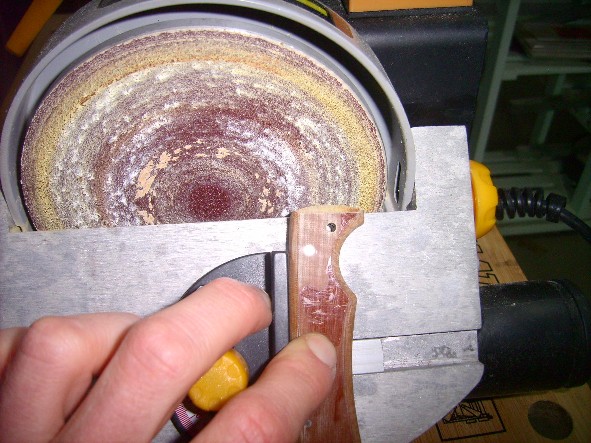
Et à présent je peux ajouter un petit chanfrein à
45° à l'avant du manche
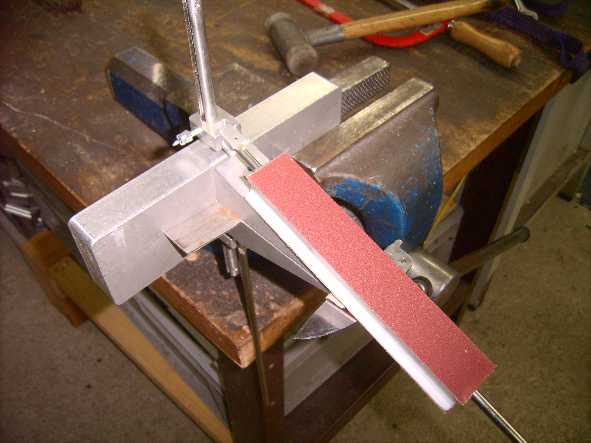
A la main (et donc à température très
éloignée du moindre risque de revenu), j'ai mis avec un
support
copié sur le "wicked sharp" appartennant à un
collègue de travail un demi-angle de 15° au sommet du
tranchant. Je me suis arrêté à P400 pour le moment
et j'ai protégé la lame..
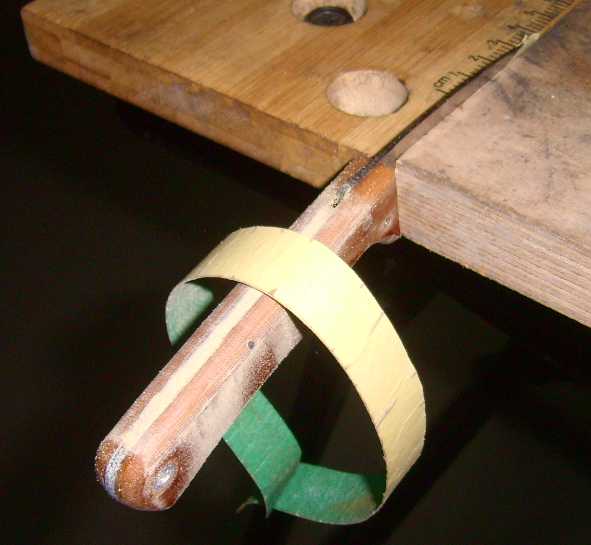
Ici j'attaque les finitions du manche avec des abrasifs de plus en plus
fin jusqu'à P600.
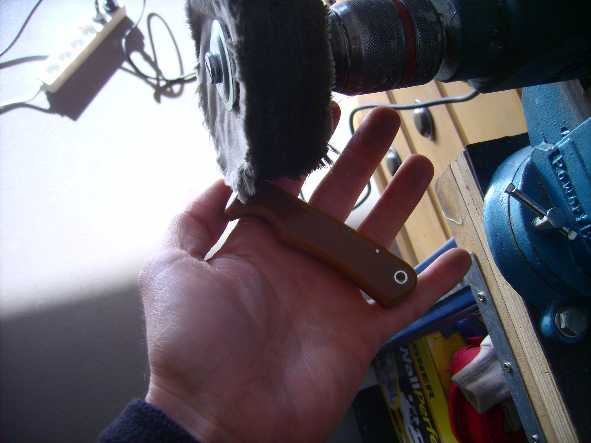
Polissage du manche aux pâtes abrasives 40 et 2 microns et disque.
Pour faire ressortir la matière, au lieu de la traditionnelle
huile WD-40, j'ai mis de la cire de carnauba.
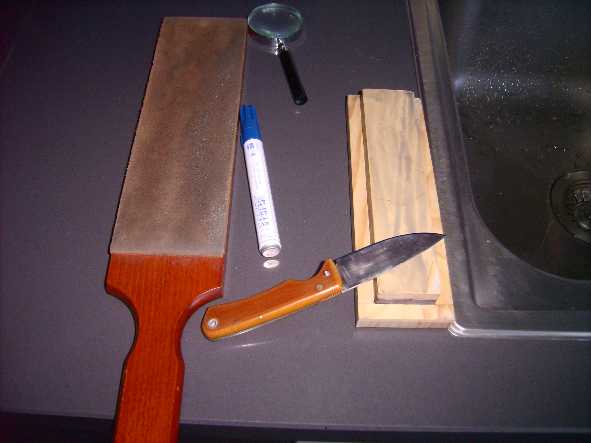
Dernier affûtage à la pierre de coticule et au cuir.

Been there, done that! Projet SFBA-2014 achevé. Pliant à
friction à palette raccourcie sur modèle "Borel II
pliant".
41 g seul. Acier 100Cr6 de 1.9 mm d'épaisseur, longueur totale
165 mm,
longueur de lame 72 mm, longueur curviligne de tranchant 73 mm,
demi-angle au sommet du tranchant d'environ 15°, épaisseur
derrière le fil 0.51 mm, ~ 62
HRc. Manche en micarta marron et entretoise en micarta
maison sur base de toile denim, finition cire de carnauba, rivets et
butée en inox, tube en aluminium.