On est à 29 g. Le tranchant fait 0,53..0,60 mm et le dos 1,39
avant de descendre à 0,56 mm à la pointe.
Il reste une trace de "peau" de forge et surtout deux petites
fissures/plis repérés à la loupe (celles
Comme je veux commencer par une normalisation "sévère"
par trempe vers 890°C, j'ai très peur
des fissures. Je pense reprendre l'émouture à la main
jusqu'à P400 pour éliminer toute amorce de
24-JUL-2014
J'ai sorti mes 3 lames du congélateur et
elles ont rejoints les deux autres précédemment
trempées. Me voilà avec 5 couteaux à
compléter pendant mes longues soirées d'hiver, ou avant.
J'ai poli un peu à la main au P120 puis 220
le "Dancelou" en 100Cr6 pour régulariser la surface et tenter
d'effacer les deux fissures/plis de la lame. La petite à l'avant
a presque disparu mais la seconde est bien là. Avec les soudures
de réparation du manche et leurs fissures, les
irrégularités de la surface de forge non disparues (une
sorte de croûte) je compte pas moins de 9 endroits à
problème potentiel. Je dois avouer qu'à ce stade cela me
ferait bien suer de ruiner le couteau à la normalisation ou
à la trempe, mais c'est ainsi même pour les meilleurs
forgerons japonais (je le sais, je l'ai lu!). Il faut que je l'accepte.
Je vais prendre mon temps pour continuer encore de
poncer à la main tout ce que je peux sur cette lame et je
tacherai de faire de même pour les traitements thermiques (pas de
stress, un jour de weekend).
27-JUL-2014
J'ai continué de polir les deux plis /
fissures de la lame, sans réussir à les faire
disparaitre. Je ne voulais pas trop affiner la lame. J'ai fini les
faces au P220 et le chant est à P400 issu du back.
Alors il faut que vous sachiez que j'ai beaucoup
cherché le bon traitement thermique du 100Cr6. On trouve 3
à 4 sources qui semblent sérieuses sur des forums
Américains, Allemands et Français mais le moins que l'on
puisse dire c'est qu'ils sont différents et manquent à
mon goût d'explications rationnelles qui permettent d'expliquer
les choix. Peut-être que tous sont valables, si leurs auteurs y
croient et les ont expérimenté. Je ne les mets pas en
doute. Mais je suis plutôt "Fakten, Daten, Zahlen" (expression
teutonne: des faits, des données, des chiffres). Du coup je me
suis rabattu sur le livre de Verhoeven et cherchant les sections
consacrées aux hypereutectoïdes pour la trempe,
l'austénisation, la cristallisation, avec parfois des exemples
concernant directement l'acier 52100 américain qui n'est rien
d'autre que le 100Cr6 du point de vue composition chimique.
Alors mon protocole de trempe se rapproche le plus
de celui décrit par Verhoeven pour un exemple de 52100 (et de ma
petite expérience à la vue de mes lectures et recherches
sur les trempes des aciers de coutellerie). Je tente l'explication avec
mes faibles moyens.
- je veux tremper pour obtenir une dureté maximale après
trempe. Cette dureté s'obtient déjà avec 0.7
à 0.8% de carbone dissout dans l'austénite
- pas besoin donc des 1% complets de carbone. On va utiliser ce rab de
carbone pour l'associer au chrome afin de former des carbures de chrome
très durs qui donneront de la résistance à l'usure
à notre fil tranchant.
- la grande dureté permet un demi-angle au sommet très
fin (excellente résistance mécanique latérale du
fil) et les carbures la résistance à l'usure: c'est le
Graal, l'épée laser, qui dure... (bon pour
l'affûtage faudra voir...)
- pour le mix martensite (qui va venir de l'austénite) +
carbures de chrome (venant de la cémentite) pas besoin d'aller
au dessus de Acm (100% d'austénite), on peut rester entre A1 et
Acm à la température qui donnera une fraction massique de
0.7 à 0.8% de C.
- le diagrame fer carbone du 100Cr6 est déplacé par
rapport aux aciers purs carbone à cause de la présence du
chrome (voir ci-dessous)
- la température qui donne la fraction massique de 0,7..0,8% de
carbone se situe entre 830 et 845°C selon mes estimations (vaut
mieux choisir par défaut que par excès car trop
d'austénite résiduelle après trempe va impacter
négativement la dureté)
- bref je décide d'austéniser à 835°C
- maintenant, depuis le temps que j'en parle, je répète
qu'il faut des grains les plus petits possibles avant trempe de
façon à avoir une résistance mécanique
maximale (aux chocs) du couteau et surtout du fil (avec en prime un
sommet du fil très fin: le grain représente en gros la
résolution de l'acier; plus il sera petit plus le rayon au
sommet du fil sera petit et ledit sommet "pointu" donc tranchant)
- bien que l'acier des roulements soit très fins, dans quel
état est-il après que je lui ai tapé sur la gueule
à chaud? Je n'en sais rien. Pas mal peut-être, mais
peut-être pas. Il faut donc préparer l'acier pour lui
donner des grains fins si possible plutôt sphériques qu'en
forme de plaques et bien répartis dans la matrice.
- Verhoeven parle du truc employé par l'industrie pour livrer
des aciers fins recuits sans trempe: dans les hypereutectoïdes
chauffés entre Acm et A1, de petites particules
sphériques de cémentite se forment naturellement si
l'acier de départ ne contient pas de gros grains. Ici
l'austénite se transforme directement en cémentite
sphéroïdale et en ferrite plutôt qu'en perlite
à structure lamellaire. Le reste est difficile à traduire
pour moi et également à expliquer (laisser moi le temps
d'intégrer) mais en refroidissant lentement en repassant sous A1
on garde cette structure. Verhoeven parle de DET: transformation
eutectoïde divorcée? Meilleure traduction bienvenue
- bref reste plus qu'à être sûr de ne pas avoir de
gros grains au départ. Et cela je compte l'obtenir en passant au
dessus de Acm (environ 910°C pour le 52100; voir diagramme
ci-dessous): tout le carbone sera dissout dans une matrice pure
d'austénite dont les grains vont vite grossir mais qu'on va
casser en leur "trempant" la gueule
- la grosse question c'est les temps. En effet le chrome diminue
énormément les vitesses de diffusion. Elles
dépendent aussi du gradient de température (=vitesse de
chauffe) et de l'épaisseur de la lame. J'ai tâché
de bien régler le pifomètre.
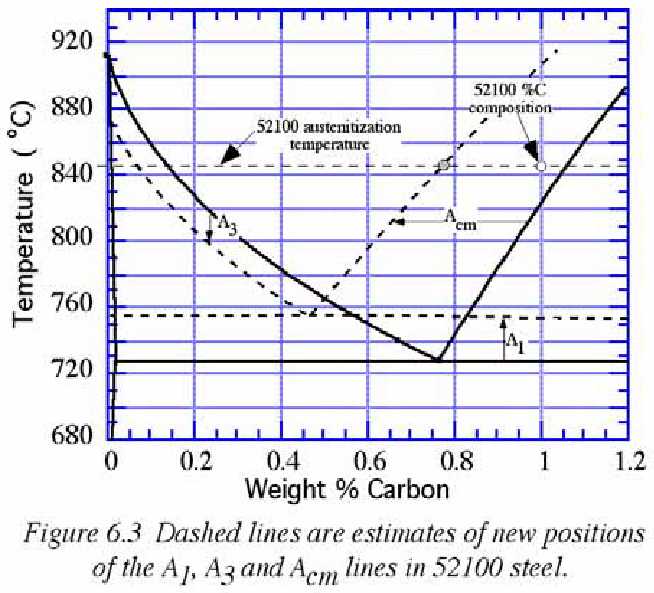
diagramme fer carbone de l'acier 52100 (=100Cr6), extrait du livre
gratuit en ligne de John D. Verhoeven.
(
Metallurgy
of Steel for Bladesmiths & Others who Heat Treat and Forge steel)
L'eutectoïde passe à environ 0.55% de C, A1 remonte vers
755°C, A3 redescend, Acm se déplace vers la gauche.
Bref avec ceci en tête, voici où j'en
suis arrivé. J'ai préchauffée mon huile dans le
tube sur ma plaque de cuisson à gaz.
- lame (1*+4) minutes à 920°C puis trempe à l'huile
de colza à environ 55°C pendant 4..5 secondes
[
ici la lame s'est courbée
latéralement mais j'ai pu facilement la redresser à la
main, dans l'étau, avec des gants sans me brûler]
- reste du refroidissement à l'air
- lame (1+5)' à 795°C
- consigne du four placée alors à 680°C avec la lame
encore dedans, porte fermée
[
idéalement pour copier
l'exemple deVerhoeven il faudrait y descendre en environ 18', mais
3'20" ont suffit -four pas assez bien isolé-, alors j'ai
laissé la lame 5' de plus à 680°C]
- sortie de lame avec refroidissement à l'air, suspendue
à un crochet dans une pièce à l'abri du vent (en
parallèle, nouvelle chauffe de l'huile de trempe)
- lame à Tambiante placée au four pendant (1+5'45")'
à 835°C [
ce devait
être (1+4)' mais j'ai eu un contre-temps]
- trempe à l'huile de colza** à environ 85°C pendant
5"
[
pas de déformation de lame
cette fois! Youpi!]
- reste du refroidissement à l'air
- congélateur 90' à -18°C
[
parce que je devais cuisiner en
parallèle sinon ç'eut été moins longtemps]
- spray réfrigérant à -52°C
- revenu au four de cuisine 60' à 200°C
- sortie de four et refroidissement à l'eau
- congélateur jusqu'au lendemain (soit environ 20h) à
-18°C
- revenu au four de cuisine 60' à 200°C
- sortie de four et refroidissement à l'eau
* 1 minute c'est environ le temps de remontée en
température du four après ouverture - placement de la
lame - fermeture de la porte. C'est une valeur moyenne. Avec la
nouvelle résistance plus puissante et le coup de main (ouverture
fermeture rapide) ce temps descend parfois à 20".
* il semble que l'huile de colza soit un très bon ersatz
d'huiles minérales spécifiques aux traitements
thermiques. Selon le bouquin de Verhoeven, que l'huile soit à
50, 100 ou 150°C n'a que peu d'influence sur sa vitesse de
refroidissement dans cette plage, bien moins que pour de l'eau en tout
cas. Par contre il faut que l'huile soit chauffée pour obtenir
un refroidissement rapide. L'huile à 20°C est bien moins
efficace. Question de viscosité? Dernière remarque au
sujet de l'huile de colza: elle laisse bien moins de calamine et autre
saloperie, sans puer, que l'huile de vidange que j'avais
utilisée pour mon tout premier couteau et les quelques restes se
nettoient bien mieux. A 1.19 EUR le litre que demander de plus?
Petite explication des trempes de 4 à 5
secondes au lieu de laisser la lame se refroidir jusqu'à la
température du liquide de trempe. L'idée c'est de
refroidir suffisament vite pour passer sous le "nez" perlitique des
courbes de refroidissement. Il faut arriver au dessous de 600°C en
moins de 3 secondes pour être sûr de passer de la phase
austénitique à la martensitique. Le début de la
transformation de l'austénite en martensite (dite Ms) se situe
aux alentours de 250°C. La martensite est plus "volumineuse" que
l'austénite et fait "gonfler la lame" dans les 3 axes. Si cette
transformation est trop brusque cela augmente d'autant plus le risque
de fissures et/ou de déformations (c'est ainsi que les sabres
japonais prennent leur belle courbure: ils sont droits au
départ!). Donc rapide au début pour ne pas louper le
coche et mollo à la fin pour "épargner" la lame

Diagramme TTT de l'acier 52100 (=100Cr6) issu du site de Kevin Cashen.
Vous vous souvenez du petit morceau
prélevé par découpe du contour au 17-JUL-2014? Je
lui ai fait subir le même traitement en parallèle jusqu'au
congélateur à -18°C inclus. Puis je l'ai cassé
pour observer le grain. Le morceau a pété comme du verre
et la section est un rêve de coutellier: grains invisibles
à l'oeil. Suis content!
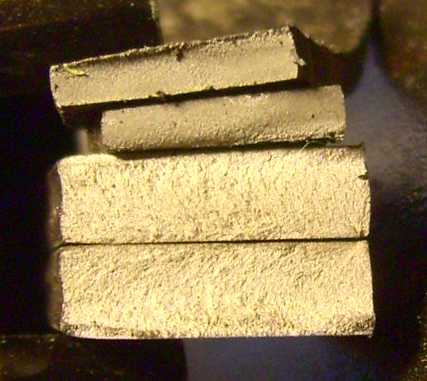
Ma chute de 100Cr6 normalisée et trempée comme le couteau
face à mon
meilleur essai sur de l'XC75, au grain le plus fin. Pour
référence la section
du 100Cr6 fait environ 7 x 1.8 [mm] et celle d'XC 75 10 X 3 [mm].
28-JUL-2014
J'ai fait le second revenu du "Dancelou" comme
mentionné hier, ci-dessus. Et comme capuchon pour mon tube de
trempe à l'huile de colza, j'ai pris une cool can que j'ai
décapité. Avec 65 mm de diamètre ça va
nickel.
29-JUL-2014
Au courrier, un colis... Des U.S.A., plus
précisément de Sugarcreek, Ohio. Yes le kit du
Build
Along 2014! Déception, vous allez encore trouver que je me
plains toute le temps. Tim Troyer avait annoncé le matos
nécessaire et plutôt que de devoir trouver des pivots,
j'ai préféré commander le kit, sachant qu'en plus
il y aurait sans doute de l'acier O1 ou du 1095. N'ayant jamais
travaillé aucun des deux, c'était la petite cerise.
L'acier à se procurer devait faire entre 2 et 3 mm, au max 1/8"
c'est-à-dire 3.2 mm.
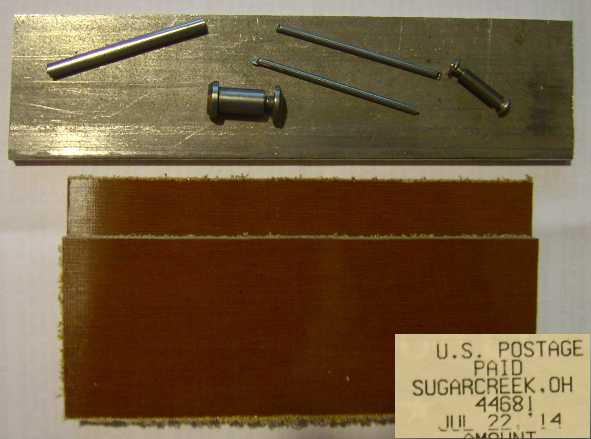
Expédiés le 22-JUL-2014: deux plaquettes de micarta
marron
de 105 X 40 X 5 [mm], deux rivets aciers
de 1/16" X 40 mm, un rivet acier de 1/8" X 40 mm, 1 vis pivot de 3/16"
X 3/8", 1 autre de 1/8" X 3/8"
et un plat d'acier inconnu de 130 X 32 X
4.65
[mm]. Que voulez que je fasse d'un bout de ferraille de
presque 5 mm d'épaisseur dans un pliant à friction? Je
suppose que c'est pour pouvoir découper une
entretoise dans une chute du micarta de 5 mm qu'on pourra
réduire à l'épaisseur du plat d'acier.
Tant pis je vais prendre un morceau plus fin dans mes tiroirs: T7Mo ou
XC 75 de 3 mm, T508 de
2.9 mm ou X46Cr13 de 2.5 mm? A moins que je ne récupère
la chute malheureuse du 100Cr6 du
"Dancelou" d'origine?
A propos de
"Dancelou", j'ai repris le couteau à l'abrasif à la main
ce soir après avoir tenté d'affiner un peu
l'émouture au back à P220. J'ai rendu le manche "rugueux"
au P40 (je compte ne pas utiliser d'intercalaire pour cette fois: bois
collé directement sur acier) et j'ai repris le reste
jusqu'à P2500 suivi des disques à polir aux pates 6.5 et
2 microns. Comme toujours il reste de nombreuses rayures mais je vais
finir par m'y faire (de ne pas y arriver). C'est dur l'échec.
Les deux plis / fissures sont toujours là.
Avant de continuer à investir du temps, j'ai
mis un tranchant sur la lame pour voir si ça ferait un couteau.
Environ 10° de demi-angle au sommet sur un tranchant d'environ 0.40
mm juste derrière le fil. Bilan ça coupe nickel. C'est
mon couteau à l'angle le plus aigu avec la lame la plus fine
jusqu'à présent.
J'ai donc continué... En mettant le logo.
J'ai dû m'y reprendre à 5 fois avant que le masque en
toner ne prenne bien: chaque fois trop chaud ou pas assez. Les 5 logos
que j'avais d'avance y sont tous passés.
L'autre face de la lame, juste sous le logo, a légèrement
jauni, à force de tentatives de faire fondre le toner au fer
à souder. L'envers du logo a donc subi un petit revenu
suppléementaire. L'électro-érosion a très
bien marché avec
le 100Cr6. Demain je tente la découpe et le collage du bois: ce
sera du galeux d'orme avec quelques petits loupes flammées dont
j'espère un beau fini.
Au fait les soudures du tube de trempe suintent
très légèrement l'huile. Va falloir soigner
ça.
30-JUL-2014
Soirée productive. La bricole sereine
ça me repose, ça me détent. Avec la scie
circulaire sur table, j'ai coupé une tranche de 7 mm de galeux
d'orme dans mon carrelet carré de 60 mm de coté. Il y a
plein de petits trous dans le bois! J'y ai reporté le contour du
manche et j'ai scié la plaquette en deux avec la scie à
ruban. Ensuite à la scie à chantourner j'ai
dégrossi le contour de chaque plaquette.
Me voilà avec juste ce qu'il faut de bois
à aplanir. Avec un mirroir et de l'abrasif P80 posé
à plat, j'ai rectifié une face de chaque plaquette. Comme
je n'utiliserai pas de fibre intercalaire, je cherche des
rugosités maximum pour augmenter l'accroche de la colle. Donc
après P80, fini, pas d'abrasif plus fin.
J'ai percé les trous du rivet (4 mm) et des
tubes laiton (5 et 6 mm) dans la première plaquette en me
servant du manche comme guide. Une pince étau plaque fortement
la plaquette sur un martyr en bois avec du ruban adhésif
à l'interface afin de limiter les risque de casse des bords du
trou en sortie de palquette. On introduit les pièces laiton au
fur et à mesure pour limiter les mouvements. Idem avec l'autre
plaquette.
J'ai façonné au back à
l'abrasif P100 la face avant (au ricasso) d'une plaquette. La seconde
fixée à la première par les tubes, j'ai
"copié" sa courbure à l'avant. Les plaquettes ensemble
j'ai poncé la surface à la main au P220, 400, 600 et 800.
Ensuite je suis passé au disque à polir avec de la
pâte 40 puis 2 microns.
Pour augmenter encore l'accroche j'ai percé
des amorces de trous de 3 mm dans la plaquette côté
manche. Il serviront de poche et réservoir pour l'époxy
une fois le manche pressé fortement contre les plaquettes. Le
manche a été rendu rugueux au P40
précédemment. A la lime triangulaire j'ai fait des
entailles au centre des pièces en laiton. Encore une fois afin
de créer des poches de rétention de l'époxy.
J'ai dégraissé les pièces
métalliques à l'acétone et les plaquettes avec un
produit appelé "décireur" (à base de
térébenthine je dirai selon l'odeur). J'ai
préparé longuement une bonne portion de ma meilleure
résine époxy, celle qui prend en 1h40 (prise très
progressive garantissant un joint très solide) de chez
Sader/Bostik. J'ai tout assemblé et mis sous presse, 5 au total.
Les excès d'époxy ont été essuyé au
coton-tige imbibé d'acétone au niveau de la face avant
près du ricasso.
Et ce sera tout pour quelques jours, car je vais
partir en vacances avec ma fille. Je reprendrai à mon retour,
avant de repartir au soleil cette fois, dans des contrées plus
lointaines. Au programme restant: rivet mosaïque maison au centre,
dégrossissage du manche, bouchage des trous éventuels au
mélange sciure+colle à bois D3, stabilisation sous vide
du bois au durcisseur, façonnage final et polissage.