1 un des morceaux du prétendu semi-inox de MJM en section 12 X 4
[mm]: Fe 85.59% Cr 13.08%
2 le second morceau du prétendu semi-inox de MJM en section 15 X
4 [mm]: Fe 86.4% Cr 12.73%
4 la lame de chez C. Schwarte Solingen: Fe 98.09% Mn 0.66% Cr 0.29% Mo
0.03%
D'abord le
semi-inox, on a un total en métaux de 98.67% et 99.13%. Avec de
tels taux de chrome, ce ne sont pas des semi-inox mais bien des inox,
quelque chose comme un X46Cr13/1.4034 ou X65Cr13/1.4037. Vu l'absence
totale de manganèse je pencherai pour le dernier. La finesse du
grain observé lors des casses pourrait aussi laisser croire
à du 12C27 mais cet acier est selon moi très bien
"dosé". On devrait être très proche de 13.5% de
chrome si c'en était. Il s'agit sans doute de la
même nuance d'acier pour les deux sections, aux dispersions de
fabrication près.
La dent de râteleuse avec un total en
métaux de 99.32% est un acier à fort taux de
manganèse, ce qui améliore la trempabilité. Sans
connaitre les taux de Si, P et S (qui ne sont pas des métaux)
qui sont forcément présents, cela laisse peu de place au
carbone. En cherchant parmi les compositions chimiques de l'excellent
site teuton
metallograf.de
avec Mn~1%, S+P~0%, Si+C~0.65%, je n'ai rien trouvé de bien
convaincant mais au moins des directions. Sachant que cet acier a pris
au mieux 60 HRc sur mon Frichet (d'où la présence d'une
quantité non négligeable de carbone), je dois
régler mon pifomètre sur un truc du style Si 0.20%
et C entre 0.45 et 0.5%. Avec Mn un poil plus bas, on aurait une assez
bonne corespondance avec un XC55.
La lame de chez Schwarte avec un total en
métaux de 99.07% est un acier à fort taux de
manganèse avec un soupçon de chrome, deux
éléments d'addition qui améliorent la
trempabilité, surtout le chrome.
Cela permet d'obtenir de bonnes trempes sur des gros lots de
pièces même si on perd un peu de temps à la sortie
du four et que toutes les pièces ne passent pas sous les
600°C en moins d'une seconde. Sans connaitre les taux de Si, P et S
(qui ne sont pas des métaux) qui
sont forcément présents, cela laisse peu de place au
carbone mais plus que dans la dent de râteleuse. Toujours
à l'aide du site cité plus haut, je conjecture avec une
forte probabilité du 1.2003/75Cr1, bref un XC75 avec un poil de
chrome.
Dernière "science" pour vous saouler: en
surfant par hasard chez Opinel, j'ai vu que leur inox
était du Sandvik 12C27M, M pour modifié. En cherchant la
fiche matière chez Sandvik je suis tombé sur leurs
leçons de traitement thermique pour les inox martensitiques
destinés à la coutellerie: 12C27, 13C26, 14C28N et 19C27.
En voilà des braves gens avec un discours scientifique
basé sur des faits, des mesures, bref du concret, du solide, du
crédible, pas du blabla de forum ou de couteliers avec des
thèses sans la moindre preuve. Et tout cas cela corrobore ce
qu'on
préssent en lisant le chapitre des inox chez Verhoeven
- quel que soit le traitement par le froid, il apporte un gain en
dureté. C'est-à-dire que même dans le
congélateur à "seulement" -18°C, l'austénite
résiduelle sera diminuée et la dureté
augmentée. Cela fiche en l'air tous les "on-dit" qu'il faut au
moins descendre à -70°C sinon il ne se passe rien.
- plus je monte en température d'austénisation, plus je
dissous de carbone, plus je peux augmenter la dureté si je
refroidis assez bas (une courbe montre 1120°C et 15%
d'austénite résiduelle avec une trempe cryo à
-70°C)
- (comme le dit aussi Landes) pas la peine de refroidir à
-70°C ou -196°C pendant 48 h, il suffit d'atteindre la
température pour transformer l'austénite en martensite
(et c'était logique car le changement de structure d'un cristal
n'est pas un phénomène continu mais un "switch", un saut
discret)
Bref avec toutes ces données, je me sens bien armé,
contre ce que n'importe quel gourou ès couteaux pourra dire,
pour mettre au point mes propres protocoles de traitement thermique
d'un inox martensitique.
15-MAR-2016
Vous souvenez vous qu'après discussions avec
un collègue très porté sur l'électronique,
j'avais dans l'idée de pouvoir affiner les fonctionalités
de mon four afin de pouvoir faire des recuits ou des cyclages
progarmmés plutôt qu'à la main et au chrono? Ce
collègue expatrié en Allemandie, loin de son foyer,
utilise son temps d eloisr pour bricoler ses projets. Problème:
il n'y plus d eprojet en cours et me propose de s'occuper de la
commande plus sophistiquée de mon four. Je dois avouer que c'est
bien tentant car ce serait à coup sûr plus
économique en temps, sans même immobilisé mon four.
16-MAR-2016
J'ai dit au collègue qu'il me fasse sa
liste de commissions et qu'on faisait aujourd'hui le kick off officiel
du projet four de trempe 2.0. Je lui ai aussi fait un petit cahier des
charges. Tout cela semble déjà exister dans les
communautés électroniques du web.
19-MAR-2016
Le matin j'ai bricolé un peu au garage
- fabrication de 2 gabarits en tôle pour la forge pour le
"Chukotat" et le "Borel V"
- rectification du manche du "Franquelin II" (j'ai aplani le manche):
c'est pas parfait mais l'époxy comblera le peu de matière
qui manque
- taillage progressif des émoutures des "Borel IV" forgé
et "Franquelin II" forgé (P100, 240 et 400): avec un tranchant
de 0.4 mm sur le premier et 0.55 mm sur le second, je crois qu'il me
faut oublier la trempe sélective du second (en dessous de 0.8 mm
j'ai toujours des vagues)
20-MAR-2016
L'après-midi j'ai bricolé pas mal au
garage. J'ai taillé les émoutures des 3 "Brochants" que
j'avais dans les tiroirs depuis je ne sais quand.
- 2 en T7Mo de 2.96 mm d'épaisseur (vendu pour 3 mm)
- 1 en T508 de 3.01 mm (vendu pour 2.9 mm)
- j'avais tracé par le passé les tranchants avec 0.8 mm
d'épaisseur
- j'ai fait des chanfreins grossiers à P40 à la main en
ramenant le métal au niveau du tranchant: cela fait une ligne
pour contrôler la progression de l'usinage et l'angle qui n'est
plus vif épargne les bandes
- l'angle de l'émouture était théoriquement de
2.66° et j'ai tout taillé avec mon gabarit à 2.8 °
- pour chaque face d'une émouture, j'ai usiné à
P40, 60 et 100.
- ensuite en appuyant à la main la lame contre la bande du back,
lame reposant sur la table, j'ai tout repris à P240 et P400,
parfois à l'aide d'un petit bout de bois pour pousser
l'émouture contre la bande
- les tranchants sont droits et à peu près
d'épaisseur constante mais pas égaux, deux lames sont
à 0.40 mm et la dernière à 0.60
- les lignes d'attaque ne sont pas assez symétriques, notamment
les arrondis joignant la plate semelle à l'émouture.
J'essaierai de diminuer les défauts à la finition
- j'ai eu l'impression d'aller assez vite, profitant des effets
d'échelle mais il m'aura fallu jusqu'à la fin 2h20, soit
47 min par lame
Me voilà présent avec 6 lames à
tremper
- le "Franquelin II" forgé en XC75 que je veux faire en
sélectif au goop; à voir vue la faible épaisseur
de tranchant restant
- un "Borel II" en damas inox (RWL34/12C27) avec un manche
rapporté plus petit que le contour fini (remplissage
époxy et sciure); ça fait longtemps qu'il attend lui
aussi
- un "Borel IV" forgé super fin en T7Mo
- deux "Brochants" en T7Mo
- un "Brochant" en T508
Là encore je vais tacher de travailler un peu en série:
trempe le même jour, réfigérateur en s'attendant
les uns les autres et revenu en même temps: 150 à 175 pour
les inox (et semi), 200 pour l'XC75
Au fait, le mélange vinaigre blanc paille de
fer (acétate de fer) est devenu une immonde bouillie orange
après une bonne semaine. Toute la paille y flotte en minuscules
particules.
Le soir j'ai reçu un e-mail de mon
collègue parti en vacances pour deux semaines et qui se propose
de me faire un contrôleur programmable pour mon four sur base
Arduino. Il s'agit d'une liste de fourniture que j'ai commandée
sur le Net: 3 articles au Royaume -Uni et 3 en Chine. On excusera mon
vocabulaire approximatif pour la traduction
- un écran LCD bleu retroéclairé blanc 2 lignes de
16 caractères
- un interface/contrôleur pour l'écran
- un lecteur pour carte SD avec alim 3.3 V
- une sorte de carte de connection bi-directionnelle
- un clavier/pavé numérique 16 touches
- un "circuit de developpement" pour puce Arduino
Tout cela est très bon marché.
21-MAR-2016
La soirée fut longue mais j'ai trempé
toutes les lames en attente. Quelques notes pour plus tard (comme
dirait Parker Lewis)
- les temps et les températures d'austénisation sont le
fruit de mon expérience et de mes dernières lectures de
chez Sandvik
- les séquences ont été choisies pour gagner du
temps
- les revenus inox/semi-inox et XC75 sont à température
"compromis" afin de tout mettre au four en même temps: de toute
façon, à 150°C mes inox sont sans doute trop durs et
à 200 mon XC75 pas assez à mon goût
- deux lames en T508 3 mm et RWL34/PMC27 2.5 mm en papillotte inox dans
le four froid
- montée de 7 à 760°C en 10'28"
- 10' à 760°C
- montée de 760 à 1020°C en 8'56"
- 10' à 1020°C et réglage à 1050°C
- trempe entre plaques alu de la lame en T508
- environ 1' de remontée à 1050°C
- 10' à 1050°C et réglage à 1070°C
- trempe entre plaques alu de la lame en RWL34/PMC27
- 44" de remontée à 1070°C
- lame en T7Mo 1.5 mm en papillotte inox introduite 3'
- trempe entre plaques alu de la lame en T7Mo 1.5 mm
- 29" de remontée à 1070°C
- lame en T7Mo 3 mm en papillotte inox introduite 6'
- trempe entre plaques alu de la lame en T7Mo 3 mm
- 32" de remontée à 1070°C
- seconde lame en T7Mo 3 mm en papillotte inox introduite 6'
- trempe entre plaques alu de la seconde lame en T7Mo 3 mm
- réglage à 830°C
(les lames refroidies, sorties des papillottes sont mises au fur et
à mesure au congélateur à -18°C)
- introduction de la lame en XC75 2 mm pendant 2' (temps de
remontée inclus) et réglage à 815°C
- refroidissement de la lame jusqu'à la couleur noire devant la
sortie de l'aspirateur (normalisation)
- introduction de la lame en XC75 2 mm pendant 1' (temps de
remontée inclus) et réglage à 800°C
- refroidissement de la lame jusqu'à la couleur noire devant la
sortie de l'aspirateur (normalisation)
- introduction de la lame en XC75 2 mm pendant 1' (temps de
remontée inclus) et réglage à 830°C
- refroidissement de la lame jusqu'à la couleur noire devant la
sortie de l'aspirateur (normalisation)
- introduction de la lame en XC75 2 mm pendant 2' (temps de
remontée inclus) à 830°C
- trempe sélective au goop
(la première lame aura passé au total 55' à
-18°C et la dernière 20')
**** j'ai coincé seulement les lames entre les plaques, qui
faisaient donc un angle entre elles (maximisation de la zone de contact
pour un refroidissement optimal)
**** le maintien était fait par deux grosses pinces serre-joint
**** ensuite j'ai pris en sandwich la semelle entre deux plaques alu
que je tenais à la main, pendant environ 30"; tout cela va
très vite avec l'alu
**** j'ai l'impression que la plupart des lames ne sont plus
alignées avec la semelle
**** le tranchant en XC75 malgré sa finesse n'a pas
ondulé mais la pointe était très tordue; facile
à redresser au marteau
**** je n'ai redressé aucune autre lame
- sortie du congélateur des lames et pulvérisation de
spray réfigérant -50°C sur le tranchant
- test de la lime: comme toujours le T508 c'est d'la balle, toutes les
autres semblent un cran moins dures et l'XC75, carrément deux
crans: souvent j'ai cru constater (à tort ou à raison)
sur certains aciers que la dureté maximale était atteinte
au moins 2 heures après la trempe....
- revenu des 6 lames en même temps dans le four de cuisine 60'
à 175°C (vérifié au thermomètre
indépendant étalonné): il n'était pas
très stable tantôt 170°C, parfois 180 voir 185°C
- refroidissement brutal des lames à 175°C dans un seau
d'eau froide
- retour à -18°C jusqu'au lendemain; pour une durée
d'environ 21h15 donc
22-MAR-2016
Suite avec le second et dernier revenu
- revenu des 6 lames en même temps dans le four de cuisine 60'
à 175°C
(vérifié au thermomètre indépendant
étalonné): très stable aujourd'hui avec 175°C
quasi constant
- refroidissement brutal des lames à 175°C dans un seau
d'eau froide
- retour à -18°C jusqu'au lendemain; pour une durée
d'environ 9h donc
Deux pièces en T7Mo (dont celle forgée) ont pris une
couleur vert olive matte. Jamais vu avant, peut-être une
réaction chimique, mais avec quoi?
23-MAR-2016
J'ai sorti les lames du congélateur vers 6h00
pour les emmener au boulot afin de les sabler à l'atelier
à la pause de midi.
25-MAR-2016
Me voilà avec 6 lames à monter:
redressage, polissage, logo, fabrication et collage des plaquettes,
façonnage final. Du boulot créatif sympa car on voit
enfin le couteau naitre. Pourtant en pensées je suis
déjà sur 2 autres lames forgées, dans le 100Cr6
récupéré il y a peu.
Et voilà plusieurs jours que je lis partout
comme correctement traiter thermiquement du 100Cr6. A cause des 1.5% de
Cr, son comportement commence à être difficile à
maitriser pour en faire un acier aux caractéristiques optimales
pour un couteau, mais je crois que c'est possible. Ça commence
à s'éclaircir dans ma caboche, trier le bon grain de
l'ivraie, les faits scientifiques des conneries dont le Net est plein,
avec si possible une aura de mystère... On en reparlera le
moment venu.
29-MAR-2016
Rien fait du long weekend de Pâques, du moins
côté couteaux. J'en étais donc à 6 lames
trempées, revenues et sablées. Ce soir j'ai tenté
de les redresser au mieux. Au marteau avec une petite panne arrondie,
au marteau à piqueter, sur un bloc de bois et un plat d'acier D2
rectifié. Ça a plutôt bien marché
jusqu'à la dernière lame. Bref sur les 5 premières
j'ai fait au mieux. Les lames en Damas inox et en T7Mo forgé
étaient presque parfaites, presque rien à faire. Celle en
XC75 forgé était tordue de partout mais comme elle n'a
qu'une trempe sélective, chaque coup de marteau a eu un effet
visible et prévisible. Long mais facile. Les 2 autres "Brochant"
en T508 et T7Mo ont surtout fléchi au niveau du raccord
lame/semelle et un peu le long du tranchant. J'ai à peu
près réussi à rectifier le tir avec des frappes
très locales du marteau à piqueter. Alors c'est mieux
mais vraiment pas parfait. Je vois tous les déafuts... Je vais
sabler à nouveau ces lames pour remettre un coup par dessus les
impacts des marteaux.
Maintenant parlons de la dernière lame,
l'autre "Brochant" en T7Mo. C'est celle avec le tranchant le plus
épais. Rien à faire au marteau, je suis vite passé
à l'étau avec 3 cylindres (ici 3 vis) pour "pousser" sur
la déformation maxi de la lame, juste derrière le
ricasso. J'y suis allé progressivement. La lame s'est
déformée de façon incroyable. Je l'ai
déformée d'au moins le double de ce que j'aurais
estimé être sa limite élastique. Et chaque fois la
lame est revenue à forme initiale. Après chaque zone
élastique, les matériaux ont une zone plastique... Juste
avant la rupture. Oui j'ai pété cette lame. Pas vu de
zone plastique. Fait chier. Tout ce boulot pour rien. Je vais voir si
je peux la ressouder et sauver un peu de ce bon acier inox, bien
trempé.
30-MAR-2016
J'ai remis un coup de sableuse sur les 5 lames
redressées.
La poste m'a livré les 3 pièces en
provenance d'Angleterre pour le contrôleur du four. Même
sans être un spécialiste, le lecteur de carte SD ne s'y
trouvait pas. En lieu et place un PCB de 25 X 25 [mm] avec une grosse
batterie 2032 dessus et l'inscription RTC.
31-MAR-2016
J'ai demandé à mon collègue de
boulot de me ressouder la semelle et la lame du "Brochant"
cassé. A la soudure sur la seconde face, l'ensemble s'est
désaligné. J'ai voulu redresser le tout à la main
(avec un métal d'apport aussi mou pas de souci pensais-je) et
nouvelle casse. Je laisse tomber, du moins pour le moment. Faut savoir
s'incliner et accepter les casses en coutellerie.
Le site anglais, contacté, s'est confondu en
excuses et m'a envoyé fissa le lecteur de carte SD. L'autre truc
est une Real Time Clock et je peux la garder.
01-AVR-2016
J'ai attaqué les logos ce soir. Apparemment
la surface sablée n'est pas d'un super grand secours mais c'est
mieux qu'une surface polie pour l'accroche du toner fondu. Le masque a
pris du premier coup sur les deux lames en T7Mo et à la
troisième tentative sur l'XC75 et le T508. pour la lame en
Damas, le masque est plus grand que le morceau d'aluminium qui le
presse. Du coup je n'ai qu'une fonte partielle du masque. Il faut que
je fasse un logo plus petit. Acutellement c'était "RWL34 /
12C27". Avec "RWL34/PM27", cela devrait raccourcir assez le masque pour
que ça rentre sous le petit pavé d'aluminium de mon fer
à souder modifié.
02-AVR-2016
Y a du boulot à faire dehors avant que la
pelouse ne "skyrocket": pissenlits par ci, tuteur par là,
replanter du gazon devant, tondre une première fois... Pas
beaucoup de temps. J'ai poli à la main la lame du "Franquelin
II", de P125 à P1000 avant de passer un coup de disque avec
pâte 6.5 microns. Petite révélation au perchlorure
de fer et nouveau polissage. C'est dommage la ligne de trempe n'est pas
très nette, plutôt diffuse... Et je ne suis pas non plus
enchanté de la rectitude du fil. Faudrait encore redresser un
chouille de ci de là.
03-AVR-2016
J'ai arrondi les angles au back de l'encoche pou
l'index du "Franquelin II" de P100 à P400. Ensuite j'ai repris
la lame et cette encoche à la main au P2500. J'ai poli à
nouveau la lame au disque avec pâte 6.5 microns avant de refaire
une révélation au perchlorure de fer car la ligne de
trempe avait disparu. Puis
- j'ai découpé 2 plaquettes grossières à la
scie à ruban dans ma planchette d'acajou de 5 mm et
- 3 rivets en laiton (4, 5 mm et tube 6/5 mm) avant
- de percer les plaquettes,
- de façonner la partie avant (arrondi de P60 à P600 puis
pâte à polir 40 microns)
- d'égréner rivets et
- face interne des plaquettes et
- de bien dégraisser semelle, rivets (acétone) et
- plaquettes (décireur)
Pour finir préparation d'époxy, enductuion, collage et
mise sous presse (assez fort partout pour être bien jointif car
la semelle n'est pas un modèle de planéité).
L'acajou semble avoir de gros pores et une dureté très
moyenne. Je tenterai un traitement de surface au durcisseur ou au
bouche-pores (talc). Mais j'espère au moins qu'il prendra un
beau poli comme les bâteaux Riva... Le fait de pouvoir travailler
avec des plaquettes toutes faites, d'épaisseur constante et aux
faces bien parallèles facilite le boulot.
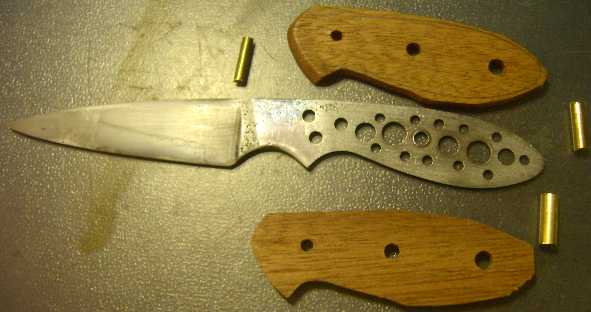
Vus les nombreux trous de liaison dans la semelle et la porosité
de l'acajou, je me suis épargné le
perçage de petites poches de rétention de colle sur les
faces internes des plaquettes.
04-AVR-2016
Le soir au back j'ai ramené les plaquettes du
"Franquelin II" au niveau de la semelle et j'ai fait des chanfreins
à 22.5, 45 et 67.5° aux arêtes des plaquettes pour
accélérer le façonnage manuel ultérieur.
05-AVR-2016
Cette semaine je suis en congé, avec ma
fille. Après le repas j'ai fini à la main et aux abrasifs
P80, 120, 180 et 320 le manche du "Franquelin II". Comme l'acajou est
sans doute un bois à peine mi-dur, j'ai voulu le durcir un peu.
J'ai donc nettoyé le bois au décireur et je l'ai
badigeonné d'une couche de durcisseur pour bois antique et
vermoulu. Un coup de paille de fer au bout de 30 min pour enlever le
côté brillant.
Après 3 heures de séchage un coup de
P320 puis de P600 (pour la quincaillerie en laiton et le chant) pour
revenir au bois naturel. En fait j'espère que le durcisseur
bouche un peu les pores et pénètre quelques
dixièmes sous la face externe du bois. Le soir j'ai enduit
à la pulpe du doigt l'acajou de mon vernis tampon maison. Il
sèche désormais tellement vite que j'ai mis 3 couches sur
chaque plaquette en une seule opération. J'ai renouvellé
l'opération des 3 couches avant le coucher et après un
petit coup de paille de fer 000.
06-AVR-2016
Au cours de la journée j'ai mis 4 couches
d'huile de tung avec 1.5% de siccatif sur l'acajou du manche du
"Franquelin II" dont les deux premières diluées à
50% avec de l'essence de térébenthine.
07-AVR-2016
Disques à polir avec de la cire de carnauba
pour le manche et des pâtes 6.5 et 2 microns pour la lame. Encore
le tranchant à mettre et le "Franquelin II" sera terminé.
08-AVR-2016
Dans un morceau d'environ 7 mm d'épaisseur de
galeux d'orme, j'ai découpé avec ma petite scie à
ruban des contours grossiers de plaquettes pour le "Borel IV"
forgé en T7Mo. Avec une feuille d'abrasif Norton sur un miroir
j'ai poncé à plat les faces internes. Je cite cette
marque car
- vue sa durée de vie, elle est est meilleure marché que
des feuilles chinoises vendues par paquet de 100 et
- surtout, pour une raison que je ne m'explique pas, c'est la seule
avec laquelle j'ai des faces bien planes.
Demain on tente les perçages des plaquettes, le sciage des
rivets, le polissage de la lame ainsi que de la face avant des
plaquettes et le collage. Je suis p-ê un peu
optimiste...
09-AVR-2016
Bon suis pas arrivé au bout...
- sciage des
rivets,
- perçages des plaquettes,
- nouveau dégrossissage des contours et
- polissage de leur face avant
Le galeux d'orme a révélé au fur et à
mesure des trous, comme si de petits vers y avaient festoyer. Je vais
tacher de boucher avec de l'époxy.
C'est pas demain que je vais coller car je consacre
mon dernier jour de congé à ma fille (on va à un
salon de poupée en Alsace; qui sait, je pourrai peut-être
choper une ou deux astuces transposables à la coutellerie), ni
la semaine prochaine, je serai à l'étranger pour le
boulot.
Les 3 derniers composants pour la modernisation de
la commande du four sont arrivés de Chine: arduino, broche et
(mince j'ai oublié). J'enverrai le tout par la poste interne du
boulot à mon collègue de l'usine lundi avant de partir
pour l'aéroport en cours de journée.
16-AVR-2016
New York Herald Tribune: "suite à une longue
absence d'Europe, échangerai tulipes, variété
grandes fleurs contre jolie gravure moderne". Me voilà de
retour. entre deux averses durant la tonte de la pelouse, j'ai poli
à la main la lame du "Borel IV" forgé de P125 à
P400 pour essayer de faire une finition un peu satinée. Il reste
des traces de forge et c'est bien ainsi pour montrer l'origine du
couteau.
Dégraissage de tous les acteurs, collage
à l'époxy, mise sous presse et essuyage des excès.
18-AVR-2016
Sorti de presses, j'ai ramené le contour des
plaquettes du "Borel IV" forgé au niveau de la semelle au
backstand. J'ai ensuite tracé l'épaisseur des plaquettes
avant de les rectifier, encore au back. Pour finir, chanfreins
grossiers à 22.5, 45 et 67.5° sur le contour, toujours au
back.
Les plaquettes ne sont pas parfaitement jointives au
ricasso et au cul de la semelle. De plus le façonnage a fait
"remonter" à la surface encore davantage de fissures, trous etc
dans le galeux d'orme. J'ai comblé les jours avec la semelle
à l'époxy. Une fois sec, je ferai la finition
grossière du contour à la main. A partir de là, je
boucherai les trous restants avec un mélange de sciure et
d'époxy. Je reprendrai plus tard la finition à la main
aux abrasifs plus fins en espérant que tous les trous soient
bouchés. Et puis une bonne couche de durcisseur avant les
finitions ultimes aux vernis, huile et cire. Ça c'est le plan
pour l'instant...
19-AVR-2016
J'ai commencé à façonner les
contours du manche du "Borel IV" forgé avec de fines bandes
d'abrasifs P80 et P125. On doit être à 90..95% de la forme
finale. J'ai ensuite bouché tous les trous et fissures avec un
mélange de sciure (du manche évidemment) et
d'époxy.
21-AVR-2016
J'ai juste eu le temps d'enlever à la main
avec de l'abrasif P120 les surépaisseurs d'époxy sur le
manche du "Borel IV".
24-AVR-2016
J'ai un peu corrigé et affiné le
contour du "Borel IV" forgé au back, puis j'en ai
façonné le manche jusqu'à P600 comme pour la
finition. J'ai bien dégraissé le manche avant de lui
passer au pinceau deux couches grasses de durcisseur de bois vermoulu
dans l'espoir d'en augmenter un peu la dureté, au moins
superficielle. Une fois humide le grain du galeux d'orme fait vraiment
de belles loupes ou flammes.
28-AVR-2016
J'ai enlevé la couche superficielle de
durcisseur au P320 puis P600. Hein? Mais oui sur le "Borel IV"
forgé, suivez un peu nom de bleu!
01-MAI-2016
J'ai poli à la pâte 40 microns le
manche en galeux d'orme du "Borel IV" forgé, puis je lui ai
passé au fur et mesure de la journée à la pulpe du
doit 3 couches de vernis tampon maison, 3 couches d'huile de tung
diluée à 50% avec de la térébenthine (et
1.5% de siccatif) et 3 couches d'huile de tung pure (avec 1.5% de
siccatif).
J'ai poli là la main es lames de 2 des 3
"Brochant" (pas celui au manche cassé): P120, 180, 220, 320, 400
et 600. Ensuite disque à polir et pâte 6.5 microns.
02-MAI-2016
Le soir j'ai sélectionné un morceau de
mirabellier de l'automne 2014 de chez mes parents. Il a l'air bien dur
et sec, sans trou ou fissure. J'en ai fait deux planchettes de 7 mm
à coup de scie circulaire, de dégauchisseuse et de rabot.
Dans l'une d'elle j'ai débité à la scie à
ruban deux plaquettes grossières pour le "Brochant" en T508.
Pour l'autre, je vais faire de même dans une planchette de buis
que je vais essayer de teindre avec mon mélange vinaigre paille
de fer. En effet, bien que très dur et dense (donc idéal
pour la coutellerie), je trouve la blancheur pure du buis ennuyeuse
à souhait.
03-MAI-2016
Le soir j'ai débité à la scie
à
ruban deux plaquettes grossières en buis pour le "Brochant" en
T7Mo. Ensuite j'ai poncé à plat au P60 sur un miroir les
faces internes de ces plaquettes et de celles en mirabellier d'hier.
J'ai découpé la quincaillerie dans des tiges de 2 et 3.2
mm d'aluminium ainsi que les tubes de passage dragonne dans un tube alu
de 6 mm (4 mm intérieur). Sortie de la perceuse pour les trous
de fixations que j'ai comme toujours repris en cote majorée de
+0.1 mm c-à-d 2.1, 3.3 et 6.1 mm. Cela facilite le montage et
permet de loger un peu de colle dans les liaisons.
05-MAI-2016
Il faisait trop beau pour rester dans le garage. Le
soir j'ai cependant pu finir l'avant des manches en mirabellier et en
buis, égréner toutes les surfaces, les dégraisser
et enfin coller le tout. Mise sous presse et essuyage des coulures
d'époxy aux ricassos.
08-MAI-2016
Au back j'ai façonné les manches en
buis et en mirabellier des deux "Brochants"
- élimination des surplus des rivets
- contours ramenés à la semelle
- épaisseurs ramenés à 4, 5 et 6 mm de l'avant
vers l'arrière
- chanfreins grossiers pour casser les angles
Faudra continuer à la main. Le buis est si uniforme que c'est
d'un ennui, mais d'un ennui...
10-MAI-2016
A la faveur du soir en plein air, j'ai
façonné à la main les contours du manche en buis
du premier "Brochant" en T7Mo: P40, P120, P180, P320 et P600. Je me
demande si l'arrière du manche n'est pas trop gros visuellement
par rapport au reste du couteau. Physiquement il permet cependant une
très bonne préhension. L'idéal c'est quand
esthétique et pratique vont de pair. Il parait que c'est
toujours ainsi pour un bon couteau.
14-MAI-2016
J'ai
façonné à la main les contours du manche en
mirabellier
du second "Brochant" en T508: P40, P120, P180, P320 et P600. Il est
très proche du premier, presque des jumeaux.
15-MAI-2016
Long après-midi au garage.
- J'ai découpé à la disqueuse un plat de sandwich
02/XC10
- au back j'y ai façonné le contour d'un "Borel V"
- j'y ai taillé une émouture plate
- j'ai taillé l'émouture dans le second plat en T508
qu'il me restait du modèle "M(a)ousse"
- j'ai repris au back jusqu'à P400 les chants des "Borel V",
"M(a)ousse" et des deux "Brochants"
- j'ai poli au disque et à la pâte 40 microns les manches
des deux Brochants"
- nettoyage au décireur des deux manches
- enduction au pinceau du manche en buis de thé afin de le
charger en tanin
- enduction au doigt du manche en mirabellier de 3 couches de vernis
tampon maison et de 3 couches d'huile de tung diluée à
50% avec de la térébenthine (et 0.5% de siccatif)
16-MAI-2016
Suite du traitement des manches des "Brochants"
- enduction au pinceau de deux couches de vinaigre blanc / fer du
manche en buis (acétate de fer) et séchage. Le manche n'a
noircit que par endroits et assez peu par rapport à ce qu'on
voit sur la toile
- enduction au doigt du manche en mirabellier de 3 couches d'huile de
tung pure (et 0.5% de siccatif)
- enduction au doigt du manche en buis de 3 couches de vernis CCL et de
3 couches d'huile de tung diluée à
50% avec de la térébenthine (et 0.5% de siccatif) et
d'une couche d'huile de
tung pure (et 0.5% de siccatif). Le
grain est enfin un peu mis en valeur.
17-MAI-2016
Suite du manche en buis
"ébénifié"
- enduction au doigt de deux couches d'huile de
tung pure (et 0.5% de siccatif): une le matin, une le soir
20-MAI-2016
J'ai percé le manche du "Borel V", surtout
pour l'alléger. Malgré 4 trous de 8.5 mm, 14 trous de 3
mm et un seul de 6 mm, le centre de gravité s'est à peine
déplacé de 3 mm vers la pointe: il suffit de mettre le
couteau avant et après perçge en équilibre au bord
d'une table pour marquer d'un trait la moitié où le
couteau commence à basculer. Dans l'état percé, le
centre de gravité est encore trop en arrière à mon
goût. Faudrait soit encore limer des boutonnières ou
affiner la semelle... Bof.
24-MAI-2016
Quelques nouvelles de la commande du four que
mon collègue bricole sur base arduino. Il me l'a ramené
aujourd'hui pour une petite démo avant de fabriquer un boitier
- on peut programmer des pas comprenant une montée ou une
descente avec une vitesse donnée et un plateau avec une
durée donnée
- le clavier utilise 4 touches pour se déplacer dans les menus
et une touche de validation
- il faut une alimentation 5 V en sus
- on a laissé tomber la programmation par carte sim et PC
extérieur car je préfère la version autonome
à partir du clavier seul
- on peut stocker 20 programmes avec un maximum de 10 pas
- pas de fonction PID donc je ne sais pas comment la stabilité
de la température sera. Il faudra faire un essai.
- il faudra sans doute aussi ré-étalonner la lecture de
température de ma sonde type K
25-MAI-2016
Quelques nouvelles des fronts:
Front du four à régulation par Arduino
- le collègue a intégré les circuits dans ma
boîte existante hier soir
- pour une connection plus facile du thermocouple, j'ai commandé
une fiche femelle et un peu de câble compensé pour type K
- je me demande si je ne peux avoir les deux systèmes en
parallèle dans la boite: le premier pour un usage rapide et le
second pour des rampes bien précises
Front de la production
- comme les 2 et 3 juillet prochains je dois assister MJM le forgeron
(chez qui j'ai fait un petit stage de forge) pour des démos de
forge et tenir un stand commun à la fête de l'artisanat
dans le château fort de mon patelin d'enfance pour y montrer mes
réalisations
- comme je risque d'avoir quelques fous qui voudraient acheter un
couteau (ben oui c'est le risque)
- il me faudrait un peu de marchandise à vendre,
éventuellement
- du coup j'ai ressorti le Brochant cassé pour le ressouder
- sans four d'ici là (c'est dans à peine un mois)
impossible de faire de nouvelles lames
- bref je vais tenter de finir un "Brochant" de plus et peut-être
le "Borel II" en damas inox
26-MAI-2016
Mon collègue au boulot m'a ressoudé le
"Brochant" cassé. Comme toujours je lui ai dit de ne surtout pas
meuler les cordons, que je le ferai et comme toujours il a
meulé, m'a enlevé trop de matière et
voilà... Cela fera des défauts de plus. Enfin ce n'est
pas bien grave. En fait je l'aime bien le collègue.
27-MAI-2016
J'ai encore tenté de mettre un logo sur le
"Borel II" en damas inox et tant que j'avais le fer à souder de
sorti, j'ai fait de même sur le "Brochant" réparé.
J'ai réussi du premier coup à mettre le long texte "RWL34
/ 12C27" sur le premier couteau. Pour le second, j'ai arreté de
compter au sixième essai, je crois qu'il m'en aura fallu 8 ou
9... Pourquoi?
Le meilleur était encore à venir:
impossible de faire la gravure. Il ne se pase rien sous le coton-tige.
Mauvais contact? J'ai essayé au moins 30 minutes, rien à
faire sauf un court instant sur le T7Mo et après plus rien non
plus. Pourquoi?
28-MAI-2016
Le matin j'ai encore tenté la gravure:
toujours rien à
faire. Je ne comprends pas.
Après le déjeuner, j'ai fait un peu de
forge.
Mais bon visiblement c'est pas ma journée. J'ai voulu forger
deux bruts mais j'ai dû me limiter à un seul, surtout par
fatigue du poignet droit et ampoule naissante au pli du pouce
malgré le port de gants. J'ai beaucoup utilisé la
massette de
chantier de 1.5 kg. Le barreau de 100Cr6 d'environ 4 à 5 mm
d'épaisseur (bague extérieure d'un roulement) est
plutôt "dure" sous le marteau. Cela fatigue mais le sort m'a
accordé une pause car après 35 minutes je suis
tombé en panne de gaz. me suis aussi brûlé les
poils de l'avant-bras gauche, resté trop longtemps devant la
forge (flûte plus rien à couper pour tester
l'affûtage des lames...)
Petite apartée: une bouteille de 12.5 kg de
propane coûte en ce jour 16.70 EUR au Luxembourg (je vis juste
à côté; cela me met aussi notoirement à
l'abri de certaines pénuries organisées côté
huile de roche). Si vous voulez me dire combien coûte votre
propane en France, envoyez-moi un mail. J'estime que ma première
bouteille a dû tenir 20 à 25 heures, mais je me gourre
peut-être lourdement...
Au retour, j'ai fini de forger le brut d'un
"Chukotat". La semelle et la lame sont amincies (1.53 mm à la
pointe et 2.05 au cul; c'est plutôt l'inverse qu'il fallait
atteindre) mais au point le plus
épais, je voulais avoir environ 3 mm fini et j'y suis tout juste
(3.26 au max) après forge. Ce sera donc forcément plus
fin après l'usinage par abrasion. Par contre le point le plus
épais semble bien au milieu et je ne vois pas de gros
défaut de manque ou de surplus local de matière. Je me
répète toujours en forgeant "if thou wilst a keen edge
win, forge it thick and grind it thin" (je me dis que ça aide en
parlant l'anglais façon biblique; eh puis ainsi les gosses du
quartier me craignent et évitent les jeux de balle près
de ma caisse).
Ayant un four hors fonction pour cause de mise
à niveau du contrôleur (pour pouvoir faire des rampes),
j'ai mis ce brut de côté en attendant ses prochains
traitements thermiques. Vous le savez il faut toujours du temps pour
assimiler des connaissances et mes dernieres lectures (notamment Landes
qui résume bien cela mais la "procédure" n'est pas
donnée clairement je trouve ainsi que Verhoeven quand il
évoque
le 52100 aka 100Cr6) m'ont convaincu que lorsque je
forge du 100Cr6 ou une lime en haut carbone faiblement ou non
alliée, il faut faire plusieurs recuits spécifiques avant
usinage
et un dernier après avant de passer à la trempe. On en
reparlera ici
le moment venu,
avec les températures, les cycles et tout et tout.
Je suis sorti acheter une petite table de camping
chez Décathlon et un bout de tissu noir: il s'agit de me faire
une petite table pour exposer mes couteaux dans un mois à la
fête artisanale.
Juste avant d'écrire ces lignes j'ai encore
essayé de graver les logos, cette fois en partant du principe
que la pince croco du coton-tige (le "moins") était
oxydée (plus de contact). Je l'ai échangée avec
celle qui va au manche (le "plus") tandis qu'au manche j'ai
pressé la fiche banane dans un trou. Ça a marché!
Alleuia! J'ai dû déchanté avec le damas inox:
toujours rien à faire. Putain rogntudju!
Comme je suis bloqué côté logo,
traitements thermiques et forge pour demain (dimanche, présence
des voisins), j'ai voulu préparer les plaquettes pour le
"Brochant" (bois de rose: dalbergia frutescens) et le "Borel II"
(olivier et intercalaire noir) mais j'ai manqué de motivation...
Allez, à demain.
29-MAI-2016:
bonne fête Maman!
Premier essai de gravure le matin. Ça a
marché nickel sur le damas inox. C'est à n'y rien
comprendre (oui j'ai vérifié l'alim!).
Du coup j'ai poli les deux lames des "Brochant" et
"Borel II" à P125, 180, 220, 320, 400 et 600. Il reste des
rayures mais je suis passé malgré tout au disque coton
avec pâte à polir 6.5 microns. Faudrait que j'essai un
disque sisal un jour. Le résultat est très satisfaisant
sur le "Brochant" par contre de grosses rayures sont ressorties sur le
damas inox.
La fiche matière de Damasteel dit de prendre
de l'acide sulfurique pour la révélation. Juste histoire
de voir j'ai trempé le damas 1 minute dans le perchlorure de
fer. Il y a bien révélation et du coup les rayures sont
bien moins visibles. Je vais cependant laisser cette lame de
côté et la reprendre encore à la main. J'aimerai un
résultat haut de gamme (pour de l'acier à 400 EUR/m en
prix standard faut bien un peu se mouiller!)
Ma chute FTFI de bois de rose a suffit tout juste
pour y faire deux plaquettes. J'ai percé les trous de 2, 3.2 et
6 mm pour la quincaillerie alu en me servant du manche comme guide
avant de tout élargir à resp. 2.1, 3.3 et 6.1 mm.
Découpe de la quincaillerie alu: rivets 2 et 3.2 mm et tube 4/6
mm. Ensuite ponçage à plat de la face à coller
(P60) et façonnage, chanfreinage ainsi que polissage de la face
avant des plaquettes (P100, 180, 320 et pâte 40 microns sur
disque coton).
Il y a un jour là où mon
collègue a meulé les cordons de soudure de la
réaparation. Tant pis c'est l'époxy qui remplira ce
volume. Demain je vais tâcher de
- sabler le manche pour favoriser l'accroche de la colle,
- égréner la quincaillerie (même but: meilleure
accroche),
- percer de petites poches de rétention de colle dans les
plaquettes (même but)
- dégraisser l'ensemble (même but) et
- tout coller
30-MAI-2016
Au boulot j'ai sablé la lame et la
quincaillerie à la pause. Le soir j'ai percé de petites
poches dans les plaquettes et j'ai diminué leur épaisseur
à la scie à métaux. le bois de rose est
très dur, m'est avis qu'il va vite "boucher" la bande abrasive
du back. Par contre avec la chaleur de la scie ce morceau sent
très bon.
Dégraissage de toutes les pièces,
à l'acétone pour le métal, au décireur pour
le bois et préparation d'une bonne dose d'époxy.
Encollage et mise sous presse. Essuyage des excès au ricasso et
bonne nuit madame.
31-MAI-2016
En rentrant du boulot j'ai forgé. Je
culpabilise car au programme c'était jogging mais depuis que je
fais un peu de yoga j'essaie d'écouter mon corps et aujourd'hui
en bruit de fond derrière la voix qui me répète en
permanence "et si on bouffait une religieuse ou un éclair au
café" j'ai entendu mes guibolles me dire "on a bobo". Bref c'est
tellement pas moi de ne pas respecter avec discipline mes plans, que je
l'ai fait.
Bref toujours dans la bague extérieure de
100Cr6 qu'il me reste j'ai tenté de faire un second "Borel V".
On forge épais, on émouturera fin... J'ai fait une
pointe, j'ai aplani le chemin de roulement, tronçonné le
barreau et
affiné lame et soie en insistant sur cette dernière.
Chauffe moins forte et planage comme j'ai pu (puisque je n'ai pas de
chasse à planer) avec fin de séjour dans le seau de
cendres. Pour une fois il reste de la matière partout et il
faudra en enlever plus que d'habitude. Ce n'est pas très
élégant mais à l'inverse de tout ce que j'ai
forgé jusqu'à aujourd'hui (sauf lors de mon stage) il
faut que je m'approche de la forme finale par excès et non pas
par défaut de matière.
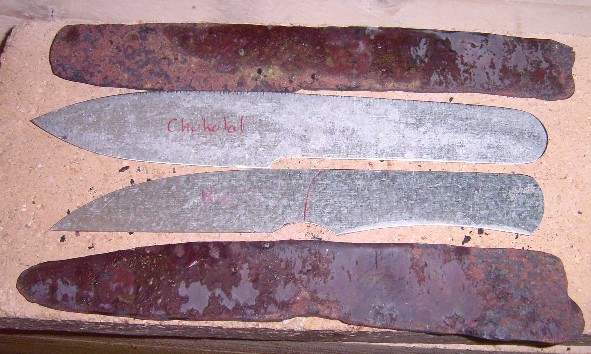
Oui je sais je n'ai pas réussi à faire de pointe au
"Chukotat" (photo antidatée, post TTH)
Mon collègue "arduino" m'a dit qu'il avait
encore rencontré ce weekend des difficultés avec les
composants (de la programmation de mon four): l'alimentation 5 V de la
carte ne sort que 2 V depuis dimanche et le clavier a 3 lignes sur 4
dont les touches ne répondent plus. La qualité des
composants chinois semble très approximative. Comme il ne
travaillera pas sur ce projet dans les 2 semaines à venir, je
lui ai demandé de me ramener ma boîte. Avec un peu de
chance, d'ici juillet je pourrai encore tremper quelques lames avant la
fête de l'artisanat.
01-JUN-2016
Comme convenu j'ai récupéré le
boitier contenant mon contrôleur et le relais statique pour mon
four. Le collègue y a déjà monté le
clavier, l'écran et le circuit imprimé avec l'arduino. Le
clavier est déjà un nouveau (commandé dimanche)
qui marche très bien pour le moment. L'ensemble n'est pas encore
opérationnel et j'ai simplement reconnecté l'ancien
circuit. Je vais peut-être faire des trempes et des recuits dans
les jours qui viennent. Pour certains recuits avec des cyclages
ça va être coton en manuel, alors soit j'attends encore,
soit je choisis des raccourcis. On verra bien.
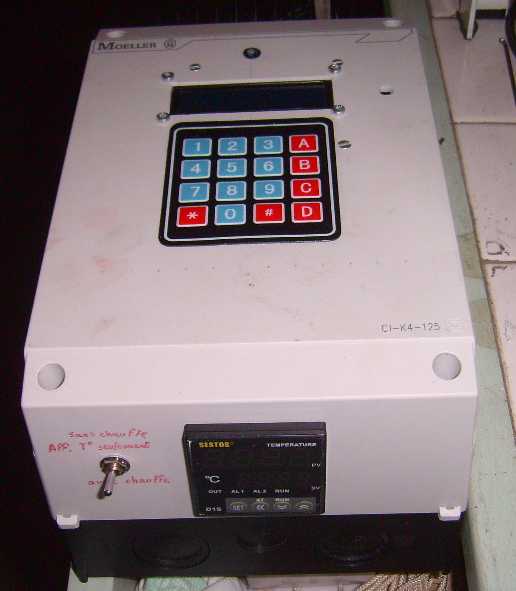
Au dessus la version II, sur le côté le contrôleur
d'origine parfaitement fiable