22-AVR-2015
J'ai encore des couteaux à finir dans les
tiroirs (je sais je me répète) mais là j'ai bien
envie de me faire un clone du Snody Menace. C'est une forme proche du
Boss avec des arcs de 25 et 250 mm en bas du manche (roues de 1 et 10
pouces), un dos un peu plus arrondi, un faux contre-tranchant et un
manche fin. S'il était chouette et que je voulais le vendre, il
vaudrait mieux qu'il soit en inox pour repousser le moins de clients
potentiels. En stock, j'ai
- du T7Mo de 3 mm mais de seulement 24 mm de large; or il me faut
absolument 25.4 au minimum pour respecter le design (la forme belle ou
moche d'un couteau se joue facilement à 1 mm près). Seul
moyen: forger un peu le tranchant pour l'affiner. Mais la forge de
l'inox (sans être impossible) et en plus avec mes faibles moyens,
c'est pas évident
- de l'X46Cr13 en 2.5 mm
- de l'AEB-L de 3.5 mm, trop gros et je le garde pour un autre projet
futur
Sinon y a du "semi-inox"
- D2 en 3 mm
- T508 en 2.9 mm
et du "qui rouille"
- XC75 en 3 mm
- XC75 en 4 mm (trop épais)
- râpe de brocante en approx 2.8 mm après usinage des
stries
- sandwich 90MV8/XC10 en 2.8 mm
- 100Cr6 à forger au préalable (au fait j'ai fait une
première relance chez Paulo Simoes pour une forge à gaz:
quedalle; l'a l'air occupé)
- limes et autres chutes inconnues à forger avant mise en forme
Bref ça sent l'X46Cr13. Je comptais y mettre
des plaquettes G10 orange de 3.2 mm. Cela nous fait un manche à
3.2+2.5+3.2= 8.9 mm d'épaisseur, ce qui est vraiment faible.
Avec deux intercalaires en fibre noire de 0.8 mm, on serait à
3.2+0.8+2.5+0.4+3.8=10.5 mm. Ça reste très fin pour la
prise en main...
23-AVR-2015
Alors il a suffit que j'en parle pour me faire
mentir. J'ai eu un mail de Paolo Simoes peu de temps après la
rédaction des lignes ci-dessus. Je l'ai appelé
aujourd'hui avec quelques questions et dans la fouléée je
lui ai envoyé un chèque pour la commande d'une forge
à gaz (son modèle standard, au propane, chambre 35..40 cm
x 12 cm, porte avant à deux ouvertures, désserte, fibre
céramique 1600°C non cancérigène,
manomètre, clapet de sécurité et
sèche-cheveux). Délai annoncé 3 à 4
semaines. Bon on va être réaliste et espérer avoir
mon nouveau jouet d'ici 6 semaines. Ça me laisse le temps de
trouver une ou deux pinces et une bouteille de propane de 13 kg.
Sortant le barbecue et le petit bois j'ai aussi
sorti la scie sur table. Les morceaux de pommier oubliés sont
déjà fissurés... Je les ai coupés en deux,
en quatre. Pratiquement pas le moindre duramen à se mettre dans
un manche. Tout cela pour rien. Je me dis que le mirabellier de chez
moi ou le prunier des bords de Moselle, ce sera pareil. Là aussi
peine perdue. J'ai aussi coupé le gros morceau de prunier fourni
par un collègue de travail et malgré
beaucoup de fissures internes il y aura peut-être un ou deux bons
morceaux de duramen. Avec le cerisier du Loiret qu'on m'avait gentiment
donné, il y avait tellement de fissures que je n'ai pu exploiter
pratiquement aucun morceau. Dommage car il est fort joli une fois poli
et huilé, comme dans le manche du "Gladel" (voir en
galerie)
En fait si je ramasse du bois dans la nature par
ici, il faut de gros morceaux avec un duramen d'au moins 40 mm (et non
pas la branche seule), ce qui nous fait un morceau d'au moins 75..80
soit 4 ans de séchage avec autant de chance de fissures. C'est
sûr c'est un métier... Alors moi avec ma fleur au fusil,
tu penses l'ébéniste amateur.
26-AVR-2015
Ce matin j'ai collé une photo du "Snody
Menace" sur mon plat d'X46Cr13 de 2.5 mm, j'ai sorti la disqueuse et
j'ai coupé. J'ai percé des trous pour les rivets et
l'allègement. J'ai façonné le contour au back. Ce
n'est pas une réplique à 100% mais c'est proche. Dans mes
projets, cette forme est tellement proche de "l'Alluviaq" que je vais
aussi baptiser ce couteau ainsi.
Alors je le sais bien et je le
réécris: il ne faut pas utiliser la technique du contour
collé mais le tracer. Avec la chaleur de la perceuse ou du back,
le papier brûle. J'étais pressé, j'avais envie d'un
truc vite fait, je n'avais pas préparé un patron avec le
contour.
L'après midi j'ai taillé les
émoutures. Coutellier c'est un métier, un talent.
- j'ai à moitié cramé la pointe
- mon tranchant devait finir à 0.4 mm, il est à 0.8
- le faux contre-tranchant qui devait finir à 1.5 mm n'a pas une
épaisseur constante (la faute à la pointe qui descend et
moi qui n'ai pas mis le bon angle entre l'axe longitudinal du couteau
et la bande: je le saurai pour la prochaine fois, c'est mon premier
contre-tranchant)
Bon je fais quoi avec ce taudis? Ben je le finis
comme d'hab'. Je vais essayer d'amincir le tranchant avec une petite
émouture convexe. La trempe ensuite et après tout
reprendre à l'os et au papier abrasif histoire de gommer au
maximum les défauts esthétiques.
27-AVR-2015
C'est fou comme un nouveau jour peut vous redonner
du courage. J'ai repris à la lime, à l'abrasif, à
la cale puis à la main tous les défauts de "l'Alluviaq"
clone de "Snody Menace" jusqu'à P400. J'ai
- égalisé les lignes d'attaques (les "plunge lines" en
anglais pour ceux qui surfent dans le monde du couteau) des deux
tranchants,
- aminci de façon convexe à 0.2 mm le tranchant (son
épaisseur augmente plus vite qu'avec une vraie émouture
plate) et
- égaliser l'épaisseur visuel du contre-tranchant (le
couteau est plus régulier ainsi)
J'ai tenté d'enlever la moindre amorce de rupture que ce soit
sur le chant de la lame, autour des trous (chanfreins partout). La lame
prête à être trempée fait 52 g.
Ne me demandez pas pourquoi mais j'ai
décidé d'essayer d'augmenter la durée
d'austénisation de l'X46Cr13 mais c'était une sorte
d'intuition (sans doute les lectures et le temps d'intégration
des choses apprises). Deux paliers vers 450 et 850°C semblent lui
faire du bien. A moins d'avoir 2 fours de plus ou deux bains de sels,
c'est impossible pour moi. J'ai alors décidé de mettre la
lame (dans sa papillotte inox) dans le four froid et une fois la
température d'austénisation atteinte, d'attendre encore
12 minutes. Auparavant, c'était lame froide dans four chaud avec
10 minutes d'austénisation (plus la remontée en
température; souvent environ 1 minute).
- au bout de 15 minutes l'ensemble était à 915°C
- au bout de 20 minutes, 1001°C
- la température cible de 1060°C fut atteinte en 24'31"
- 12 minutes supplémentaires de maintien
- refroidissement 30" sous plaques alu (vraiment efficace; on peut
manipuler la papillotte à la main nue)
- puis 40' au congélateur à -18°C
- spray réfrigérant à -50°C
- test de la lime: putain c'est d'la balle! C'est le X46Cr13 le plus
dur (et de loin) que j'ai eu en sortie de trempe jusqu'à
présent
- revenu de 60' à 150°C au four de cuisine
- refroidissement dans un seau froide
- stockage à -18°C jusqu'au lendemain (18h20; soit environ
20 h)
SMS
8:02 Bonjour, le courrier est bien arrivé, merci je vous tiens
au courant [C'est mon chèque pour la forge à gaz]
28-AVR-2015
En rentrant j'ai préchauffé le four de
la cuisine à 150°C et j'ai sorti la lame du
congélateur afin de la poncer un peu au P600 dans le but
d'éliminer les colorations apparues à la trempe. Ensuite
reprise des traitements thermiques avec
- revenu de 60' à 150°C au four de cuisine
- refroidissement dans un seau froide
- stockage à -18°C jusqu'au lendemain (6h00; soit environ 10
h)
Pourquoi déjà poncer? Parce que j'ai
songé que je pouvais tester une finition sablée. Comme
demain je vais à l'usine, j'irai voir à l'atelier, si par
hasard il y a une sableuse qui traine et je ferai un essai sur le
manche le cas échéant.
Comem déjà mentionné plus haut,
avec des plaquettes de G10 de 3.2 mm, l'épaisseur totale du
manche sera de 3.2+2.5+3.2= 8.9 mm. C'est fin mais c'est un peu plus
que mon "Snndy Black Diamond Boss 2012" avec deux couches de paracorde
stabilisée. Là aussi c'est un essai... Pour voir... En
éthnologue quoi. Ça devrait faire un couteau fin, discret
(sauf la couleur!) et plutôt élégant, qui ne
prendra pas de place (par exemple dans une pochette ou un petit sac
à main).
29-AVR-2015
Alors il y avait bien une sableuse à
l'atelier de l'usine. J'ai d'abord commencé par le manche. La
surface devient rugueuse et uniforme. La colle époxy va
très bien y accrocher. Un examen ruguo-tactile au doigt et
à l'oeil plus tard et je décide de tenter le coup avec la
lame. L'ensemble est devenu très mat, sans doute un tout petit
peu trop rugueux. Le point positif c'est que toutes les rayures ont
disparu et l'aspect est très uniforme. Il n'y a plus aucun
travail de finition requis. C'est un gros gain de temps.
Sur un sac de "sable" à côté de
la machine, j'ai relevé les indications suivantes: "Steel Shot -
GS-R nach DIN 8201 - 0,10..0,20 mm". Apparement des particules
métalliques de 0.1 à 0.2 mm. L'atelier s'en sert pour
préparer des pièces avant peinture ou pour des moules
où nous injectons une colle thermofusible (ça doit pas
améliorer la facilité de démoulage tout ça).
Le masque en toner pour la gravure du logo a super
bien adhéré. Encore un bienfait du sablage.
Décidément... Mais, car il y a un mais, bien que
parfaitement gravé le logo ressort très mal. On le
distingue très bien en incidence rasante mais pas de face.
Ça fait un peu logo fantôme. On va dire que ça
donne un style.
J'ai coupé les rivets et le tube après
les avoir égrénés au P120. Je percerai les
plaquettes demain, je les dégrossirai à la scie à
ruban et je les collerai. Je mettrai sans doute juste avant le
tranchant. Au sujet des trous et des rivets, ayant constaté par
le passé de très légers "gonflement" de la
matière (la martensite occupe plus de volume que la ferrite), je
perce en général mes trous avec un excès de 0.1 mm
avant trempe
- pour les rivets inox de 3.85 mm (barre récupérée
sur une grille de four, d'où la cote batarde), perçage
à 4 mm
- pour le tube alu de 6 mm, perçage à 6.1 mm
Les fôrets de 4 et 6.1 mm passent encore dans le manche durci et
c'est aussi avec eux que je vais percer les plaquettes. Cela me permet
d'avoir une toute petite couche de colle époxy tout autour des
rivets. A demain...
30-AVR-2015
Plaquettes superposées et collées au
double face, je les ai percées en me servant des trous du manche
comme guide. En montant les plaquettes à blanc avec les rivets
j'ai pu reporter le contour du manche. J'ai scié les
excès à la scie à ruban en suivant le tracé
du contour.
J'ai mis le tranchant sur la lame avec un demi angle
au sommet de 15° environ. Le tranchant est trop épais juste
derrière le fil. Du coup la partie affûtée remonte
trop haut et ce n'est pas esthétique. Je n'ai donc pa
affiné suffisamment le tranchant à la lame avant la
trempe. Moi qui préfère les lames tranchantes aux lames
plus" costaudes". L'épaisseur derrière le fil est de
l'ordre de 0.7 mm. Je l'aurai souhaité à 0.4.
J'ai façonné l'avant des plaquettes
puis je l'ai poncé à la main jusqu'à P2500 avant
passage au disque à polir chargé de pâte 2 microns.
J'ai masqué la lame et tout nettoyé
à l'acétone: couteau, plaquettes et rivets/tube.
Préparation de colle époxy à prise progressive,
enduction et mise sous presse. Nettoyage des excédents au
ricasso à l'acétone.
01-MAI-2015
J'ai dû mélanger la colle époxy
hier soir vers 21h00. A partir de quand peut on poursuivre le travail
sur le couteau? Les colles époxy ont un temps de prise qui
varie. La règle de base, c'est plus le temps de prise est long,
meilleure sera la résistance mécanique du joint à
la traction, au cisaillement...
J'ai commencé à faire des couteaux
avec de l'époxy de marque Araldite "à prise progressive".
La notice indiquait une durée de vie du mélange de 1h30
environ et une prise totale au bout de 14 h. La durée de vie est
importante pour tous les ajustments parfois nécessaires pendant
le collage: rivets, essuyage des excédents...
Dans le même rayon et la même marque il
y avait un modèle "90 secondes" et "5 minutes". Ce sont les
durées de vie des mélanges qui sont indiqués ici.
avec un temps de mélange minimum requis d'environ 2 minutes (un
mélange homogène est super important), on se dit qu'avec
la "90 secondes" c'est mal barré. J'ai cependant une paire de
seringues de ce modèle pour une éventuelle
réparation d'un objet biscornu qui n'autoriserait aucun serrage
avec des pinces, serre-joints ou ficelles. 90 secondes de maintien
à la main (outil universel s'il en est) c'est possible.
Toutes ces colles sont très chères au
poids. J'ai donc aujourd'hui deux gros flacons d'épocy
(résine+durcisseur) issu du net. Ils sont dits "slow cure"
(prise lente) mais la durée de vie du mélange est de 30
minutes. La notice ne donne pas de temps de prise complète mais
recommande d'attendre 24 heures. Ce matin le mélange restant
dans le récipient qui m'a servi à le faire est dur. Idem
sur le couteau. Ça fait 11 heures. Je ne travaillerai pas le
couteau avant cet après-midi, soit au total 17 heures de prise,
sous presse. Ça devrait suffire.
Mes 5 grandes règles avec l'époxy
- prendre une formulation à prise la plus progressive possible
- dégraisser les surfaces, y compris celle du récipient
mélangeur et leur donner une rugosité pour une meilleure
accroche
- mélanger longtemps: perso 2 minutes et quand je pense que j'ai
fini, je remets 30 secondes en plus. "Sicher ist sicher"
- serrage obligatoire, modéré à fort en fonction
de l'épaisseur du joint restant que l'on veut.
- nettoyage des coulures avant la solidification avec de
l'acétone
Ici pour du G10 directement sur de l'acier (sandwich
pas optimal en terme de résistance; m'enfin ça reste
hyper-costaud), j'ai choisi un serrage modéré avec des
pinces munies de ressorts.
L'après-midi j'ai donc façonné
jusqu'à la finition le manche. En sortie de presse, on est
à 84 g. J'ai utilisé deux disques à polir, avec de
la pâte 6.5 et 2 microns. Ils ont énormément sali
le G10 et à ma grande surprise, le nettoyage a été
quasi impossible avec de l'alcool ou de l'acétone. Ce qui a le
mieux marché (sans être parfait) c'est encore une fois le
décireur pour bois. Je peux aussi encore essayer le WD40 qui
fait parfois des miracles.
Je ne suis pas satisfait de la courbure du manche
(dans son épaisseur). Les plaquettes sont visuellement trop
plates encore. Peut-être que je vais reprendre l'ensemble mais
pour aujourd'hui ça suffit. On est à 75 g à
l'état fini.
02-MAI-2015
Tard le soir j'ai repris à la main et
à la cale à poncer les plaquettes de "l'Alluviaq" clone
de "Snody Menace". J'ai préfére cela au back pour bien
garder le contrôle progressif d'enlèvement de la
matière. Les plaquettes sont à présent bien
arrondies. Après la finition à P2500, j'ai enduit un cuir
neuf de pâte 2 microns pour la finition brillante sans salir le
G10. Peine perdue. Bien que la pâte soit blanche, le G10 prend un
léger voile plus sombre, plus visible dans les couches de fibre
de verre. Par contre j'ai réussi à presque tout enlever
au décireur. On est à 72 g.
03-MAI-2015
Tôt le matin j'ai tenté de faire un
étui e Kydex. Décidément suis pas doué avec
cette matière. Je dois encore tâter pour la meilleure
méthode et tacher d'être répétable.
L'étui est minimaliste avec deux rivets. Je l'ai plié
grossièrement (ce qui a donné la meilleure
défiition de la lame dans l'étui) puis j'ai mis les
rivets. Dégrossissage du contour notamment pour le profil
conjugué de l'extrémité du manche. Retour au
four pour la définition finale. Mis suis repris à trois
fois et je ne suis pas satisfait. Finition du contour. On est à
86 g au total. Quelques notes pour moi
- protéger la lame avec une seule couche de ruban à
masquer
- four de cuisine: sôle + voûte, 165°C, tôle
patissière alu pleine, retournée sur grille en position 2
(70% sôle, 30% voûte)
- ne pas prendre de gants à revêtement plastique, il fond
et colle sur le Kydex brûlant
- rivets: percer à 4.2 mm
07-MAI-2015
Il y a quelques jours j'ai vu sur le Net le
modèle Hiker 2.0 de Kyley Harris. Il est déjà le
créateur du Svord Hiker que j'ai copié avec le
"Coacoachou". Je me suis dit qu'histoire de garder la main je pouvais
aussi le refaire. J'ai un peu modifier la forme à mon goût
et fait un patron. J'ai aussi l'intention de le faire de 2 mm
d'épais. Mais je n'ai aucun acier dans cet épaisseur. Il
faut que j'en réduise un de 2.5 ou 3 mm. C'est du boulot chiant
mais je n'ai pas le choix sauf à acheter un autre acier ou
à taper dans le disque (de 2 mm) de la vielle
débroussailleuse de mon père que j'ai retrouvé il
y a peu.
En gros j'ai le choix entre le X46Cr13 en 2.5 mm, le
T508 en 2.9 mm, l'XC75 et le T7Mo en 3 mm. Le hic c'est que le dessin
tient en gros dans une bande 25 mm. J'ai encore deux barres de T7Mo
mais avec leur 24 mm de large, j'ai du mal à y faire tenir le
moindre dessin un peu courbe... A moins que...
Oui il ne manque qu'un petit bout de métal
pour que ça tienne en 24 mm de large et comme je ne veux que 2
mm, pourquoi ne pas tenter une déformation plastique à
chaud c-à-d du forgeage. Bon, forger l'inox c'est pointu selon
les fiches matières qu'on trouve partout: entre 800 et
1100°C et en dessous gros risques de fissures. Ou alors on essaie
et puis on verra bien.
J'ai tracé le contour du "Coacoachou II lean"
sur une barre de T7Mo et je l'ai "sorti" à la scie puis au back.
Le morceau manquant se situe au ricasso, là où il y a
parfois un casse-goutte. J'ai longtemps chauffé avec ma lampe
à souder mais le métal n'a même pas changé
de couleur. J'en ai eu marre et j'ai tapé dessus. Ça a
marché: il manquait si peu de métal que la
déformation requise était minime.
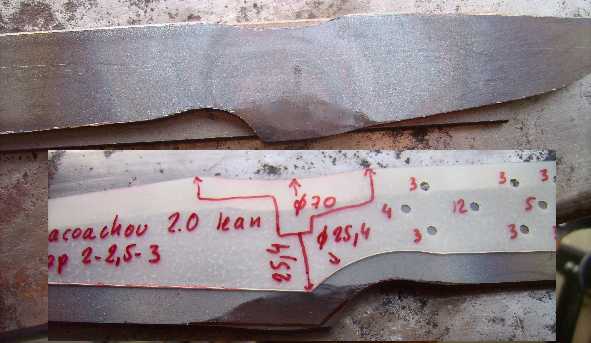
Sur mon enclume, en haut après chauffe et coup de marteau de 800
g (derrière il y a une bande 24 mm
pour vous montrer ce qui manquait)
en bas le patron et le profil complet reporté.
On verra ce que
ça donne mais la bonne nouvelle c'est que je devrai pouvoir
sortir au marteau des plats de T7Mo affinés au tranchant pour
des dessins tenant dans une bande de 26 à 27 mm.
Peut-être bien plus avec la forge que j'ai commandé
à Paulo Simoes.
Comme ce projet est un essai, autant explorer encore
d'autres possibilités
- je vais faire la trempe à l'huile de colza et non pas sous
plaques alu pour voir si la dureté augmente de façon
sensible (normalement non)
- donc pas de papillotte inox non plus (on va voir si ça
décarbure beaucoup)
- pas d'austénisation trop élevée (1100°C
d'habitude pour dissoudre un max de carbone), car à la maison je
ne peux pas de toute façon descendre sous -50°C (et encore
c'est un très court instant) pour éliminer l'excès
d'austénite résiduelle
- à l'usine on fabrique beaucoup d'outils pour nos capteurs dans
des plaques de "Pertinax". Il y a de petites chutes plein les
poubelles, chutes assez grandes pour faire des plaquettes. Avec 10 mm
ces chutes sont épaisses mais très planes et de couleur
brunes. J'ai pris 5 petites chutes de 35 X 120 cette semaine.
J'ai tapé "Pertinax" sur Google. Le
"Pertinax" est un composite dit "FR-2" dont la matrice est du papier,
noyé dans une résine phénolique. Il fait partie de
la grande famille des Micartas et nous revoilà
déjà dans la coutellerie. Marrant, non? Comme pour tout
micarta, sa poussière est sans doute cancérigène.
Port de masque obligatoire.
Bon demain tentative de perçage du manche
avant affinage de l'épaisseur et perçage du micarta (une
seule plaquette que je vais essayé de couper en deux à la
scie à ruban).
08-MAI-2015
J'ai percé le manche du "Coacoachou 2.0".
Pour les rivets inox de 3.85 mm, j'ai percé à 4 mm et
pour le tube alu de 6 à 6.1 mm. Par contre pour ne pas
renouveler l'erreur du dernier "Alluviaq" et ses horribles petits
cercles noires très fins autour des rivets, j'ai percé le
Pertinax à 3.9 et 6 mm. Le couteau pèse dans cet
état 62 g. Après enlèvement d'environ 0.7 à
1 mm d'épaisseur, où en seront nous? Facile (avec une
hypothèse quasi certaine d'acier homogène), entre 62 X
2.3/3= 47.5 g et 62 X 2/3=41.3 g.
10-MAI-2015
Histoire de se détendre l'après-midi
j'ai "descendu" à 2 mm environ l'épaisseur du "Coacoachou
2.0". L'épaisseur n'est pas constante. Il ne faut plus que je
fasse ce genre d'opération mais que je me procure la bonne
épaisseur directement. Il va y avoir immanquablement des jours
entre plaquettes et plate semelle. Dans la foulée j'ai fait un
casse-goutte à la lime et j'ai taillé les
émoutures scandinaves hautes avec environ 2.5° de chaque
côté. Finition de l'émouture à P400 au back
en vue du traitement thermique. Contrairement au couteau
précédent, cette fois je n'ai pas laissé trop (0.7
mm aulieu de 0.4 l'autre fois) mais pas assez de matière au
tranchant: à peine 0.2 mm. C'est dur de voir qu'on est nul...
(disons qu'on progresse très lentement)
Du coup j'ai peur de la décarburation puisque
je voulais faire sans papillote inox (essai pour voir) et de la
déformation avec l'huile de colza plutôt que plaque alu
(essai pour voir aussi). Je vais y réfléchir. En
attendant il faut encore finir à la main jusqu'à P400
cette lame, faire des chanfreins sur les trous et reprendre à la
main la ligne d'attaque de l'émouture au niveau du casse-goutte
(symétrie pour l'esthétique). On est à 32 g.
Avec ma petite scie à ruban Proxxon, j'ai
coupé en deux longitudinalement mon morceau de Pertinax.
Mauvaise idée: il m'a fallu des heures (hauteur de coupe 35 mm,
c'est déjà la limite pour ce type de matériau) et
j'ai aussi eu peur de désaffûtter la lame. Mais comme la
matrice est en papier et pas en fibre de verre, je crois que la lame
(pour le bois) est encore bonne. Après coupe, les surafces
planes restantes se sont arcboutées. Libération de
contraintes internes sans doute... C'est dommage il me faudra aussi
encore les aplanir
11-MAI-2015
J'ai remis des chanfreins à tous les trous du
manche du "Coacoachou 2.0" avec une fraise à noyer. Puis j'ai
repris toute la lame à la main jusqu'à P400. Ensuite j'ai
mis la lame en papillotte dans le four froid et je l'ai
réglé à 850°C. J'ai renoncé à
l'huile et à l'absence de papillotte pour cet essai. En effet
avec les reprises à la main le tranchant est presque descendu
à zéro. Trop de risque de voile et de
décarburation à l'endroit où j'ai le plus besoin
de dureté.
Je résume le traitement thermiques
- lame dans four froid réglé à 850°C
- 9'32" pour arriver à 850°C
- 5' de plus à 850°C (petit palier)
- puis réglage du four à 1070°C
- 8'40" pour arriver à 1070°C
- 8' de plus à 1070°C
- trempe entre plaques alu avec la papillotte: j'ai pris soin de
commencer par le tranchant en plaquant l'alu à la main contre
les émoutures (maximisation de la surface de contact)
- ouverture de la papillotte
- léger redressage (prudent) de la pointe au marteau
- 30' à -18°C au congélateur
- spray réfrigérant à -50°C sur le tranchant
- test de la dureté à la lime demi-douce: excellent,
ça patine!
- 45' à 150°C
- refroidissement dans un seau d'eau froide
- retour à -18°C jusqu'au lendemain soir
12-MAI-2015
Suite des traitements thermiques avec, après
22 h environ au congélateur
- 45' à 150°C
- refroidissement dans un seau d'eau froide
- retour à -18°C jusqu'au lendemain matin (soit environ 11 h)
En parallèle, j'ai poncé à plat
au P60 les faces à coller des plaquettes en Pertinax. Demain je
ramène tout à l'usine et à la pause, je sable
l'ensemble: lame, plaquettes et rivets.
13-MAI-2015
Comme prévu j'ai tout sablé
aujourd'hui. Quelques remarques vue le peu de travail effectué.
Les deux trous de 4 mm percés dans la semelle ont réduits
de diamètre après la trempe. Le jeu avec les rivets de
3.85 mm est devenu plus faible. Par contre, le trou de 6.1 mm ne semble
pas avoir bougé car le jeu avec le tube alu de 6 mm est toujours
aussi important. C'est bizarre.
Le tranchant a presque une épaisseur nulle et
malgré cela, il est resté très "stable"
après la trempe. La règle empirique de laisser 0.8 mm au
tranchant avant la trempe semble très conservatrice et
contre-productive si l'on cherche à obtenir un excellent pouvoir
de coupe. Il y a de fortes chances que ce couteau devienne le plus
tranchant que j'ai jamais produit.
14-MAI-2015
Il y a des jours moins joyeux que d'autres. Faisons
face! Petit déj au soleil, exercice en VTT, fabrication de
patisseries à gogo, encore du sport avec de la natation, sortie
ciné et coutellerie. Ne pas penser.
J'ai commencé par dégrossir les
plaquettes: contour, face externe aplanie, face avant finie et
chanfrein à 45° à l'avant aussi. Comme annoncé
je vais faire un essai de sablage du Pertinax pour augmenter le grip.
J'ai repris au P400 puis P600 la seule
émouture pour lui donner une finition tirée de long.
C'est très moyen mais c'est raccord avec le reste de la finition
sablée. Ce polissage est éaglement là pour
augmenter le contraste du logo, afin de ne pas renouveler
l'expérience malheureuse de la dernière lame
sablée.
J'ai réussi le transfert à chaud du
masque en toner du logo du premier coup.
Dégraissage intensif de toutes les
pièces et collage sous presse à l'époxy pour la
nuit.
15-MAI-2015
Le matin j'ai sorti le couteau des presses. Avec le
back, j'ai "descendu" les rivets à fleur des plaquettes, puis
pareil avec leur contour jusqu'au niveau de la semelle. C'est souvent
mon étape préférée, de ne voir aucun jeu
entre semelle et plaquettes, quelquechose de bien jointif.
Ensuite j'ai mis des chanfreins à 22.5, 45 et 77.5 ° aux
bords avant de continuer le façonnage à la main.
C'est à ce moment que j'ai découvert
une fissure dans le Pertinax de la plaquette, entre le premier et le
second rivet inox. Rien de bien méchant car elle ne commence ni
ne finit sur la semelle. Elle ne devrait pas évoluer, en toute
logique. J'ai arrêté le façonnage à la main
à P180 car je compte sabler le tout. Inutile de se faire du
travail en plus.
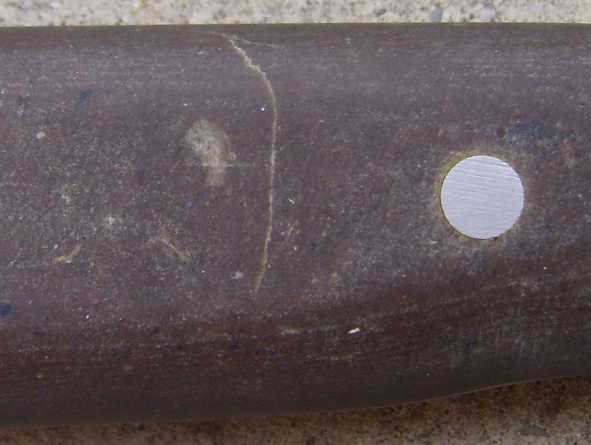
A t-elle été provoquée au sciage? Etait-elle
déjà là? J'espère qu'elle sera invisible
après sablage.
L'après-midi j'ai utilisé ma copie chinoise du
système Lansky pour mettre un tranchant sur le couteau. J'ai mis
l'angle minimal possible, soit environ 12.5° d'après mes
mesures et simple calcul trignométrique. Le métal est si
fin au fil qu'il semble souvent plié. C'est très bizarre.
Il n'y a que
deux
trois explications
- le métal est trop mou (vue le test de la lime, je serais
étonné et il n'y a pas eu d'enlèvement de
matière "à chaud" après la trempe),
- un angle total de 25° est trop aigu pour du T7Mo (25° c'est
pourtant pas si extrême) ou
- je m'y prends comme un manche pour l'affûtage
17-MAI-2015
J'ai encore peaufiné quelques détails
du manche du "Coacoachou 2.0" (des micro bosses, des arrondis) au P180,
à la main. J'ai enfin un tranchant qui tient sans se plier.
Finition du manche à P400 et il est prêt pour un sablage
mardi à l'usine. Je ferai sans doute encore un étui Kydex
et il y aura une photo pour vous, chers lecteurs.
J'ai fait ma classique mesure de dureté par
comparaison avec des couteaux aux duretés connues avec
lesquelles j'essaie de rayer la lame
- Izula à 56..57 HRc
- Tenacious à 58 HRc
- F1 à 59 HRc
- Trapper en D2 à 60..61 HRc
- Lauri PT à 63 HRc
Aucun n'est en mesure de rayer le T7Mo ce qui en toute logique signifie
que je suis au moins à 63 HRc. Ça parait techniquement
difficile avec le T7Mo qui selon mes calculs dissout à peine
0.49% de carbone dans l'austénite à 1100°C. Mais j'ai
peut-être chopé une barre de T7Mo (c'est une nouvelle
barre que j'ai entamé ici pour ce couteau) un peu haute en
carbone. Dans la zone 0.45 à 0.55% de carbone, le moindre
centième en plus fait grimper significativement la dureté.
Bizarrement sous la loupe pendant mes mesures, j'ai
pu voir que le fil était facilement pliable à cause de sa
finesse (on est à moins de 0.1 mm d'épaisseur). Or
à 63 HRc, il devrait casser non? Quoique des lames japonaises
à 62..63 HRc passent également sans problème le
"flex test" (je vous incite à chercher sur Google): on fait
plier le tranchant en appui sur une barre métallique de 6
à 10 mm de diamètre, sans trop forcer. En relachant
l'effort, le tranchant revient élastiquement en place. Plus on
force plus le tranchant plie jusqu'à casser. A chacun de
developper un feeling pour un compromis dureté (casse)
élasticité (retour) acceptable pour son usage.
19-MAI-2015
J'ai entièrement sablé le "Coacoachou
2.0". Le Pertinax du manche ne prend pas la même rugosité
en fonction de l'angle (il reste lisse aux arrondis). Ça donne
un genre. Le soir j'ai fait un étui en Kydex avec deux oeillets.
24-MAI-2015
J'étais à une brocante dans un village
voisin ce matin. J'y ai trouvé une pince de forge "maison" qui a
l'air neuve pour 4 EUR et une râpe de maréchal ferrant de
la marque américaine "Save Edge" pour 2 EUR. Il est possible
qu'elle soit cémentée (du carbone seulement dans le
premier demi-millimètre environ et rien au coeur donc pas de
trempe possible) mais à ce prix ce ne sera pas une grosse perte
si c'est le cas.
Les deux objets sont destinés à ma
future forge à gaz qui ne devrait plus tarder, si Paulo Simoes
m'entend...
26-MAI-2015