Une zone triangulaire non trempée de la même taille que sur les deux autres
sur mon "Kipawa".
Alors pour
l'instant la solution pour avoir une pointe trempée, c'est de
tailler une lame plus petite dans les bruts trempés en
évitant cette zone. Comme les "Bujeault" sont des prototypes de
test, je ne vais pas sacrifier de beaux morceaux de bois monobloc. Je
vais en faire à partir de carrelets plus petits issus de mes
chutes de chez FTFI. Alors j'ai sélectionné deux morceaux
de bois serpent, deux autres d'amarante et une grande planchette de ce
qui semble être du bois bagasse pour faire la partie centrale
dans laquelle sera creusée la forme complémentaire de la
soie.
J'ai repris la forge ce soir. Pendant que la forge
chauffait, j'ai vu que la soie la plus fine de la plane avait une large
fissure transversale tout près du corps principal.
- mise à la longueur de la seconde moitié de pince coudée
- un peu de finition pour arrondir les deux branches
- un peu de plat frappé dans la zone de l'axe de la pince
- suite du planage de la plane et en voulant redresser la soie fine, elle a cassé nette. Damned!
- j'ai mis ces deux pièces en recuit dans les cendres (je vais tacher de ressouder et de faire au mieux)
J'ai encore beaucoup relu des articles sur
l'austénisation et le magnétisme sur le site Knife Steel
Nerd, notamment sur les durées d'attente au delà de
points de transformation (Ac1 et Ac3) en fonction de la vitesse de
chauffe et de la structure cristalline (martensitique, perlitique,
sphéroïdale). Je continue à digérer et
internaliser de mieux en mieux après toutes ces années et
mes reflexions. Je crois que mon système d'induction ne peut
rien donner de bon avec du 100Cr6. Le 90 MCV8 semble avoir des
propriétés de cinétique plus favorables tout en
restant loin de l'idéal. Ces deux couteaux sont sans doute loin
de mes voeux d'aspiration à l'absolue perfection
métallographique. Mais on va faire l'imbécile heureux et
continuer un peu. C'est drôle de penser qu'on est à 50% du
potentiel maximal et que ça peut bien faire le job tout de
même.
16-MAR-2020
Une heure de plus pour rentrer à cause de ce
put**n de coronavirus. Des bouchons à la frontière
allemande à chaque pont que j'ai croisé sur ma route. Non
pas que j'y allais, mais tous les autres, si. Et tout ça pour
trouver un magasin vide, dévalisé, pas une miette de pain
à se mettre sous la dent. Bref pour vider la rage, j'ai
forgé un peu.
Afin de faire un petit poinçon pour taper le
trou de ma pince coudée, j'ai forgé un petit outil dans
un bout de ressort avec diamètre de fil de 6 mm. C'est pas gros,
mais ça va vite: on redresse et on affine... Je finirai la
pointe au bac (avant les traitements thermiques) un autre jour.
Ensuite j'ai poncé à plat au P60 puis
P80 les faces à encoller de mes deux morceaux de bois serpent et
d'amarante pour les manches des deux "Bujeault" en souffrance.
Décireur, puis colle à bois type D3 et 4 serre-joints
pinces sur chaque paire. Un de mes deux plus gros serre-joints pince de
chez pas cher à casser: devant, là où il y a la
petite palette articulée. D'abord une puis en essayant de la
réutiliser immédiatement après, l'autre. Ça
prouve une fois de plus la qualité dans le temps de tous ces
petits outils fabriqués à bas prix. Le pire c'est que la
variante de bonne qualité qu'ils ont dû copier il y a
40 ans a disparu du marché aujourd'hui. Je vais donc devoir
racheter exactement la même (dans un lot de 12 aux tailles différentes).
17-MAR-2020
Sortie des presses, avec la scie à ruban,
coupe à la longueur et en deux des blocs reconstitués de
bois serpent et d'amarante. Puis ponçage à plat des faces
au P60 puis P80 (en tirant vers soi uniquement; un vieux truc de Nick
Wheeler appris sur le Net il y a bien longtemps). Le "Bujeault"
à 106% en 100Cr6 sera pour l'amarante et le 107% en 90MCV8 pour
le bois serpent.
18-MAR-2020
Voilà, premier jour de ma vie à faire
du télé-travail. Alors le gros avantage c'est que je me
lève à 7h00 au lieu de 5h30, je n'ai pas 1h15 pour
l'aller et 1h15 pour le retour, la voiture ne prend pas 125 km, 5
litres de gazole ne passent par le pot et moi je récupère
autant de temps de loisir. Par contre, je vis seul depuis 2013
maintenant et la solitude me pèse souvent. Alors me voilà
servi. J'aurai ma fille la semaine prochaine.
Donc après mes heures de bureau, un peu
d'exercice et coutellerie. J'ai retaillé les lames
austénisées par induction en "Bujeault" de 106 et 107% de
l'original au back en prenant soin de bien refroidir. Je suis assez
fier de moi car il n'y pas eu la moindre coloration (faut des
bandes neuves bien affûtées). Ensuite j'ai affiné
les soies trop larges à l'origine. Par contre les deux
congés entre soie et lame ne s'arrêtent pas au même
endroit. C'est ma faute je n'ai pas fait attention. Il me faudra
rattraper cela, demain sans doute. Je vais aussi encore un peu diminuer
la hauteur de la soie sur la seconde moitié.
Puis j'ai poncé à plat la planchette
en bois bagasse qui servira à faire la partie centrale des
manches: toujours miroir et P60 puis P80. Ensuite j'ai dégrossi
les contours à la scie à chantourner. Fin pour
aujourd'hui.
19-MAR-2020
J'ai repris au back les soies des deux "Bujeault"
pour les amincir. Puis j'ai aligné au mieux les deux
congés de raccordement entre soie et lame. Ensuite j'ai
laborieusement transféré la forme de la soie sur papier,
découpé le papier et reporté le contour du papier
sur l'entretoise de bois bagasse. Suite en découpant à la
scie à chantourner et finition à la lime demi-douce. Fin
de la séance avec collage de la première face sur les
plaquettes respectives à la colle à bois type D3 et mise
sous presses.
20-MAR-2020
Journée de télé travail, tonte
de pelouse (avec affûtage de la lame pour la saison le back
étant de sortie!) et récupération de ma fille,
ça laisse
peu de temps pour les lames. J'ai juste sorti les demi-manches des
presses pour m'apercevoir que je m'étais planté sur celui
en bois serpent: au façonnage je ne vais pas me retrouver avec
la zone la plus veinée. Punaise! Deux pièces similaires
et j'arrive déjà à me planter sur une!
J'ai percé les soies pour y mettre un rivet
laiton de 2 mm. Test avec fôret HSS normal: ça part mal.
Le 100Cr6 et le 90MCV8 encore plus, trempent à l'air, rien
à faire et un recuit basique ne sert à rien ou si peu.
Mon idée de départ, c'était de chauffer
très localement la soie avec mon chauffage par induction (et
percer pendant que c'est chaud/mou) mais la pompe à eau a rendu
l'âme. Démontage (enfin découpage à la
Dremel) pour voir si c'était dû au dernier bain
salé. Mais il ne semble pas. La construction de cette pompe
chinoise très low tech ne semble pas compatible avec le milieu
aquatique. C'est ballot pour une pompe à eau... Pas de chauffe
très locale donc, alors tentative avec un fôret carbure en
y allant très doucement et progressivement. Ça a
très bien marché! J'ai fait les chanfreins avec un
fôret carbure de 5 mm (pété hélàs;
mais bien avant). Perçage d'une moitié de manche avec la
soie comme guide puis reperçage à 2.1 mm, comme toujours
dans le bois, une surcôte de 0.1 mm est nécessaire.
21-MAR-2020
J'ai façonné au back la forme avant
grossière des demi manches des "Bujeault". Ensuite j'ai
diminué l'épaisseur de l'entretoise centrale en bois
bagasse au back jusqu'à arriver à l'épaisseur de
la lame respective. J'ai fini cette opération à la main
avec abrasif sur miroir mais impossible d'avoir des faces
opposées parfaitement jointives. D'habitude j'y arrive mais
impossible aujourd'hui et cela sur les deux! J'ai collé
l'ensemble à la colle type D avec mise sous presses fortes pour
compenser les déafauts de planéité.
Ensuite j'ai repris un peu les lames à la
main avec limes et abrasifs. Celle en 100Cr6 avait accidentellement
frotté le back équipé P120 en haut de
l'émouture et celle en 90MCV8 avait une petite
surépaisseur juste derrière le ricasso. J'ai aussi fait
des encoches à la lime queue de rat dans
les soies. Malgré l'impossibilité de les percer avec
des fòrets HSS conventionnels, ça allait à la
lime. Bizarre.
J'ai refait l'attaque chimique au perchlo sur celle
en 100Cr6: 2 x 5 min dans du perchlo tiède avec neutralisation
subséquente et ponçage fin au P2500 à l'eau. Petit
polissage à la pâte à polir les métaux
domestiques pour finir.
22-MAR-2020
J'ai dégrossi le contour des manches des
"Bujeault" au back. M'y suis pris comme une tanche puisque j'ai
enlevé un petit millimètre de trop à l'avant du
manche du "Bujeault" à 106% en 100Cr6: le petit
décrochement entre lame et soie est visible hors du manche.
Ça donne un genre. J'ai enesuite ramené
l'épaisseur des manches à environ 14 mm. Ensuite j'ai mis
des chanfreins à 45 puis à 22.5 et 67.5° tout
autour sauf à l'avant où j'ai mis un chanfrein à
35°. J'ai repris un peu les faces avant pour enlever la
couleur brûlée du bois mais j'ai renoncé pour ne
pas faire "apparaitre" ne plus de soie. En ecrivant ces quelques lignes
je m'aperçois que j'aurai dû donner une section
légèrement conique aux manches vus de face (pour y faire
à la fin une section en forme d'oeuf pointe en bas). On verra si
j'ai assez de courage dans le futur pour reprendre cela.
J'ai profité du back pour façonner le
poinçon de 6 mm forgé dans un ressort, avec lequel
je compte taper le trou pour l'axe de ma pince coudée. Le
métal sain remontant à la surface, je me suis
aperçu que j'avais très mal forgé la pointe: il y
avait un pli dans le métal sur une grande longueur, j'ai
dû éliminer une grande partie de métal de la pointe
pour revenir à un corps intègre. Encore une leçon
à retenir.
23-MAR-2020
J'ai recommandé une nouvelle petite pompe
à eau, la même que l'autre fois. Dieu seul sait quand elle
arrivera... Allez faut les sortir ces deux "Bujeault" et passer
à autre chose.
- Gravure des logos
- reprise des manches avec section ovoïde préparée
- retouche de l'avant à P220 et 400 (encore de la matière
qui recule et une soie de plus en plus apparente, sur les deux cette
fois!)
- polissage de l'avant des manches au disque coton et pâte 40 microns spéciale bois
- préparation de rivets de 2 mm en laiton
- collages manches à l'époxy, mise en place grace aux rivets
- essuyage des excès, sortie des rivets
- bouchage des trous avec du ruban adhésif
- ajout d'époxy supplémentaire entre manche et soie
- dernier essuyage à l'acétone
24-MAR-2020
On m'annonce la pompe à eau pour le 9 mai très précisément! C'est bô...
J'ai préparé un peu d'époxy
noire avec une pointe de peinture céramique et j'ai
comblé les jours entre lames et manches des "Bujeault" suivi
d'un petit essuyage des excès.
D'abord au back, puis finalement à la
meuleuse d'angle, j'ai un peu dégrossi ma plane en souffrance.
J'en ai profité pour mesurer l'angle du biseau de mes ciseaux
à bois chinois: 22° semble-t-il. Je comptais y mettre
20° mais 22° c'est peut-être mieux (les ciseaux chinois
sont dans un acier sacrément dur malgré la qualité
médiocre du bois des manches).
25-MAR-2020
J'ai dégrossi à la râpe, puis
aux limes plate batarde et demi-ronde demi-douce les deux manches des
"Bujeault" en souffrance. 45 minutes. Il y a un certain plaisir
à travailler le bois avec des outils à main: on voit les
formes prendre naissances doucement tout en étant plutôt
efficace car les outils enlèvent pas mal de matière
malgré tout. La lime est sans doute la fraiseuse à main
la plus sous-estimée de tous les outils. Un peu pour tous les
jours en ces heures de confinement. Demain on tachera de poncer et on
sera presque au bout.
26-MAR-2020
Pas eu beaucoup de temps pour avancer aujourd'hui
car j'ai dû aider ma fille à faire ses exercices de
physique. Période, fréquence et longueur d'onde...
Bref j'ai commencé à poncer à
la main les deux manches de "Bujeault". Ils sont à
présent bien agréables en main mais il faut encore des
finitions.
J'ai également réfléchi
à que faire du brut en ressort de BMW que j'avais fait à
la JPO de la forge associative et dont le cul avait brûlé
dans la forge. Pekka Tuominen a publié il y a quelques jours des
photos d'une lame brute après plusieurs étapes et sur un
fond en papier millimétré. C'est une petite lame
annocée à 70 mm (75 en réalité) pour un
puukko en port au cou. Je vais retailler grossièrement mon brut
dans cette forme, peaufiner à la forge et y mettre le manche du
Mora Eldris. J'ai également un morceau d'os (de bovin je
suppose) trouvé un jour dans ma pelouse (un clébard je
suppose après en avoir sucé la moelle). Je vais essayer
d'en faire la ferule de ce puukko. Alors avec la meuleuse
équipée d'un disque à tronçonner, j'ai
retaillé le brut et découpé un bout d'os. J'ai
façonné le contour grossièrement au back. Il
faudra finir les travaux de forge avant de poursuivre: affiner,
aplanir, égaliser, bref finitions quoi... Et puis tous les
traitements thermiques! Trouver un nom pour ce projet. Depuis
aujourd'hui je sais que je dois rester en télétravail au
moins jusque fin avril. Ça nous fait environ 1h15 de temps libre
en plus par jour, de quoi avancer si la motivation reste intacte. Aller
on va l'avoir à l'usure ce virus de merde... On va faire
ça sur une jambe comme dirait Ventura dans La
Métamorphose Des Cloportes.
27-MAR-2020
J'en ai fait encore moins qu'hier car il a fallu ramené ma fille chez sa mère.
J'ai encore recoupé le morceau d'os pour
faire la ferule du prochain puukko. J'ai décidé de
l'appeler aussi "Caplan" comme tous mes autres puukko.
Quant aux manches de "Bujeault" j'ai essayé
de boucher les pores et un joint collé non jointif avec de la
cyanoacrylate qui avait hélàs fini par durcir (en 4 ou 5
ans). Mon voisin m'a filé de la cyano fraiche que j'ai mis sur
le second manche. La suite demain.
28-MAR-2020
Suite et fin des manches. Bouchages
supplémentaires à la cyano, ponçage 180, 320 et
600. Nettoyage au décireur. Chanfreins sur les trous des rivets.
Mise en place des rivets en laiton avec un peu de cyano et matage en
place. Reprise des petits accidents dus au matage aux abrasifs et
polissage au disque coton avec la pâte 40 microns spéciale
bois. Nouveau nettoyage au décireur.
Création d'un petit casse-goutte avec une
lime ronde: les tranchants sont tout de même assez durs, et
encore une fois je constate que le 90MCV8 est un poil plus dur que le
100Cr6.
Création du tranchant à 15° environ, à main levée avec la meule à eau.
Enduction des manches à l'huile
- 3 couches d'huile de tung diluée à 50% à la térébenthine (et 1.5% de siccatif)
- 2 couches d'huile de tung pure (avec 1.5% de siccatif)
29-MAR-2020
Dernière couche d'huile de tung pure (avec
1.5% de siccatif) sur les "Bujeault". Le siccatif
accélère grandement le séchage, un peu de chaleur
modérée aussi.
Deux couches de cire de carnauba appliquées au disque à polir.
Affûtage à la main aux pierres à
eau Haïdu P180 et 280, à la pierre diamantée DMT 45
microns / P320 et finition au cuir avec pâtes 2 microns.
Deux couches de cire d'antiquaire appliquées
à la main. Les numéros 100 et 101 sont sortis du
bal. Faudra encore mettre à jour la galerie.
30-MAR-2020
Allumage de la forge et reprise du brut de puukko
taillé dans le brut cramé dans le charbon lors de la JPO:
j'ai remis tout cela en ligne, dans l'axe et à plat, bref des
finitions. 3 normalisations à l'air pulsé (sortie
d'aspirateur) et un recuit dans les cendres. Toutes les chauffes
à la forge. Au fait le ressort est un avant de BMW 320d E46. Si
ça va, je vais tenter une section rhombique (plus de
matière au milieu qu'au dos de lame) à la Yrjö
Puronvarsi.
J'ai profité de la forge pour tremper
sélectivement à l'eau mon petit poinçon de 6 mm
pour l'axe de mon projet de pince coudée. Premier revenu avec la
chaleur résiduelle en visant le gorge de pigeon puis deux de
plus à la forge en chauffant le cul, très léger.
La lime patine mais pas tant que sur les fils issus des ressorts de
bagnoles. Le petit ressort d'origine est sans doute destiné
à des fonctions moins exigeantes.
J'ai encore allongé un peu les branches de ma pince coudée en puissance.
Pour le manche du "Caplan" à venir, j'ai
changé d'idée. Par souci de simplicité et afin de
rester dans l'esprit, ouste le précieux ébène,
place à du chêne que je vais peut-être teinter en
noir au brou de noix ou à la paille de fer dissoute dans le
vinaigre blanc. Ferule en os de bovin et la lame traversante sera
matée au cul sur un pommeau en laiton. Je vais aussi tacher d'y
disposer astucieusement un tube de passage dragonne. Le morceau de
chêne fait 90 X 35 X 25 [mm] pour 57 g soit environ 723 g/dm
3.
C'est un très vieux morceau issu d'une poutre retirée
d'une maison des années 1800. Pour le manche je vais copier la
forme générale du Mora Eldris MAIS comme celui-ci me
semble parfaitement symétrique (on ne sait pas si le tranchant
est en haut ou en bas si on ne voit pas le couteau) je vais
l'améliorer avec une section ovoïde.
31-MAR-2020
Il me reste 8 heures et quelques d'heures de rab et
grace à Covid19, pas possible de les reporter au trimestre
suivant, alors pour ne pas les perdre je n'ai pas bosser aujourd'hui.
J'avais décidé d'en mettre un grand coup.
- retriat du brut des cendres
- façonnage précis du contour
- reprise de toutes les zones pour sortir tout risque d'amorce de rupture
- émouture grossière avec finition jusqu'à P400 et micro chanfrein au tranchant
- (soyons fou) reprise de l'émouture à l'a main pour bien "lisser" et "fermer" la surface
- perçage du manche en chêne
- modification du trou en se servant de la soie chauffée au rouge dans la forge
- austénisation à la forge
- trempe sélective à l'eau de pluie pure à 50°C sur environ 8 mm
- ping... ping...
- sidération, corde, pendaison
- tentative de revenus à la forge pour s'entrainer
- reprise de la face interne de l'os de bovin pour ce projet un jour, plus tard.
- découpe du morceau de laiton qui sera necessaire au cul
- (la prochaine fois commencer par une trempe sélective au goop quand on connait pas l'acier, nez de boeuf!)
- moral in the socks...
- photos et mise à jour de la
galerie

Au moins une journée de boulot perdu, un jour de congé en plus... 2 fissures sur plus de la moitié de
la lame malgré la trempe sélective.
01-AVR-2020
Pour combattre la frustration d'hier, j'ai repris la
forge de ma pince coudée. J'ai un peu peaufiné les
branches et les coudes, forgés, contre-forgé et j'ai
essayé de taper des trous de 6 mm. Ce fut difficile mais j'y
suis arrivé. Je voulais enlever le moins de matière
possible pour simplement la repousser au maximum. Pour cela j'avais
forgé un poinçon très pointu (dans un fil de
ressort de 6 mm) et avec une faible pente. C'est trop fragile, la fine
pointe se déforme au second coup de marteau. Idem pour des
pointeaux et autre chasse-clous du commerce. J'ai aussi
déformé le corps de mon poinçon maison (qui a
flambé). Pas assez bien trempé, redressé,
re-trempé deux fois!. Je comprend pourquoi tous les
poinçons qu'on voit chez le forgerons ont un cône si
prononcé: la solidité! Il faut oublier vouloir ne pas du
tout enlever de la matière.
02-AVR-2020
Suite de la pince.
- J'ai déroulé le ressort avec fil de 6 mm qui
m'avait servi à faire le poinçon afin d'en tirer un axe
pour la pince.
- J'ai contre-coudé au mieux les branches, sans outil, juste avec le bord de l'enclume et la panne du marteau de 800 g.
- avec la guillotine j'ai un peu isolé les zones des trous d'axe
afin de pouvoir courber la pince plus tard dans cette zone, au moment
des ajustements finaux.
- à la disqueuse, j'ai coupé un morceau de fil pour faire
l'axe et mis à la longueur le bec le plus court de la pince.
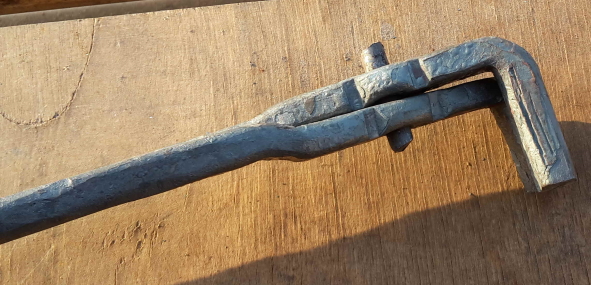
Bon c'est pas joli joli, mais je tacherai de faire une finition acceptable.
03-AVR-2020
J'ai repris un projet laissé en plant depuis
longtemps, le pliant N°161 de chez Otter. Il s'agissait de le
démonter pour le copier éventuellement un jour et
d'arrondir un peu le manche trop "carré" à mon
goût. J'ai laissé tomber le démontage depuis
longtemps mais en retouchant les plaquettes, j'avais rayé les
mitres, ressort et platines ainsi que dégeulassé le bois
sapelli.
Bref, reprise à la main au P180, 320 et 600
du bois, masquage du sapelli, reprise des parties métalliques au
back à P400, puis à l'éponge abrasive usée
fine (320, 400?) et au P600. Polissage des métaux aux disques
sisal, coton et flanelle avec pâtes respectivement noire, verte
et blanche. Masquage des parties métalliques et polissage au
disque coton et pâte 40 microns spéciale bois du sapelli.
Gros nettoyage au décireur et enduction de 6 couches d'huile de
tung dans la même journée, y compris la nuit, surtout
possibles grace au poele à granulés en route en cette
froide journée (3 couches diluées à 49.25% de
térébenthine, 3 pures, toutes avec 1.5% de siccatif).
04-AVR-2020
En matinée j'ai fini le Otter N°161: deux
couches de cire de carnauba et deux couches de cire d'antiquaire. Zou!
Retour en vitrine.
Me suis forcé à faire de menus travaux
autour de chez moi l'après-midi, et vers 17h j'ai repris la
forge de la pince coudée. Pas facile de garder au rouge un petit
axe de 6 mm, pas facile de l'avoir rouge juste sur un côté
d'abord pour y faire une "tête", des ajustements difficiles et
très longs, qui fichent en l'air tout ce qu'on a fait avant: des
faces planes, perpendiculaires, etc. J'ai décidé d'en
faire une pince pour des ronds de 13 mm puisque ce sont les ressorts
automobiles que j'ai le plus. Du coup avec un bout de ressort
redressé, j'ai forgé la forme dans chaque bec de la
pince. Pour finir enfin un jour, j'ai grossièrement poli la
pince à la meuleuse avec un vieux disque P40. Et
voilà donc ma première (et sans doute unique) pince
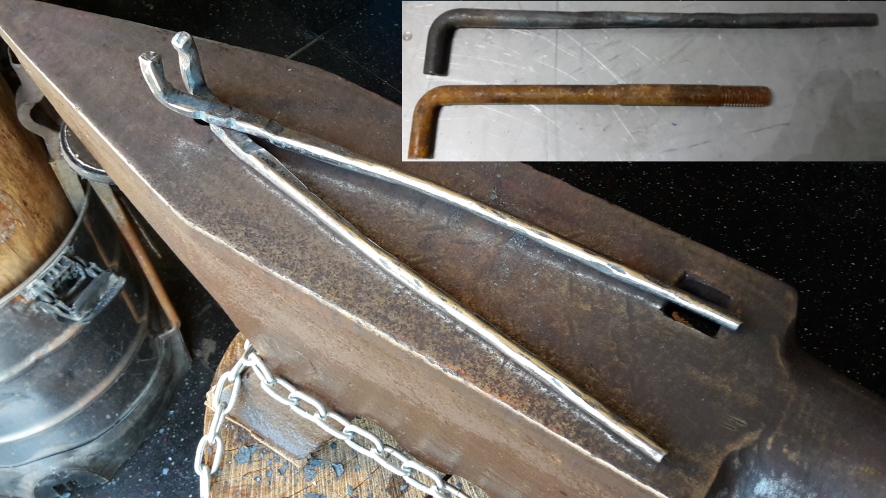
Pour rappel, chaque branche est issue d'un tirant restant du chantier
de ma maison Phénix vers fin 2008. Le design et les
étapes ont été pompés
sur le site Youtube de Glen Stollmeyer, forgeron sur balcon, à Taïpeï.
05-AVR-2020
Grace à la pince finie hier et avec le
morceau de ressort ayant servi à l'ajustement exact des becs,
j'ai forgé un décapsuleur comme celui que montre, par
exemple, Torbjörn Ähman sur Youtube. Par contre, le mien est
trempé! Ça ne sert à rien et c'est donc
parfaitement indispensable. Le plus dur et le plus long a
été l'amorce du trou.
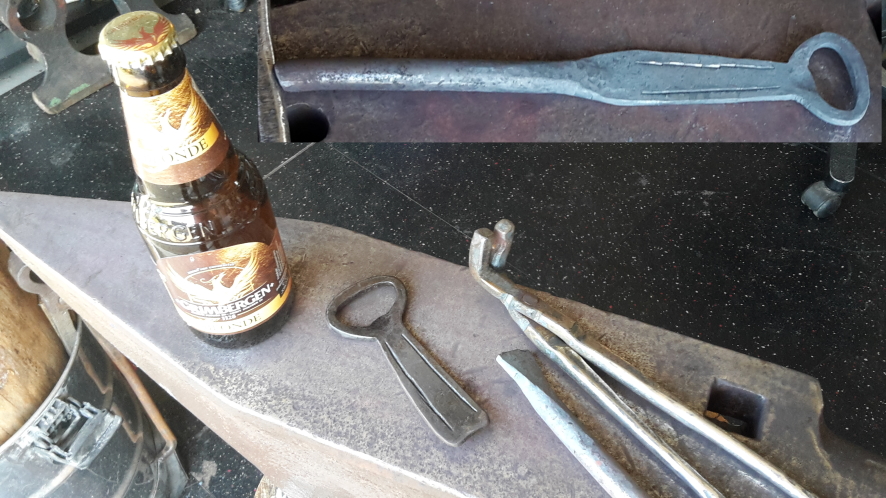
La pince a super bien marché! Trempe light interrompue à
l'eau, revenu unique gorge de pigeon (~280°C), finition huile de
lin échauffée.
J'ai mis la courbure inverse de celle de Torbjörn car sur le coup
ça em semblait plus logique. On verra à l'usage. La
binouze a été prétée par un voisin
pour mise au point et essai. Je n'ai pas ce genre de produit chez moi.
10-AVR-2020
Seconde tentative qui fut la bonne: j'ai un peu
rangé ma ferraille. J'ai trouvé parmi mes roulements une
bague intérieure pesée à 99 g, d'environ 5 mm
d'épaisseur, 19 mm de large et environ 25 mm de diamètre.
Je tacherai de retrouver la référence du roulement
d'origine. Allumage de la forge pour une tentative de coupe avec un
burin monté dans le trou de diamètre 18 mm de mon
enclume. J'ai fini le dernier tout petit morceau à la disqueuse.
Redressage, planage du chemin de roulement, début de pointe et
fin du propane. Heureusement en ces temps de confinement, j'ai une
bouteille d'avance. Donc c'est back in buisness dès demain, si
j'ai envie. Je pense tenter de refaire un puukko pour remplacer celui
en acier ressort pété à la trempe à eau.
J'ai déjà pas mal de matos pour le manche qui attend...
Autant en profiter.
Je pense tenter des TTH selon les dernières
publications du site Knife Steel Nerd. Aurai-je besoin d'un recuit
d'adoucissement à coup de DET vu que je ne vais pas percer le
moindre trou? On verra.
11-AVR-2020
Retour à la forge...Reprise du brut en 100Cr6
pour en faire un nouveau "Caplan". Alors petits détails au sujet
du roulement
- modèle 6306Z, pas de marque de fabricant
- di=30 mm, Largeur B=19 mm
- avec le poids de 99 g, cela nous fait un diamètre moyen
extérieur de la bague intérieure de 41.77 mm, soit donc
environ 5.9 mm d'épaisseur, cela en fait un plat très bon
candidat pour un couteau.
A cause de la coupe au tranchet improvisé,
les bords n'étaient pas nets et cela m'a provoqué un
petit replis de métal d'un côté de la pointe.
Je l'ai eliminé avec un vieux disque sur la meuleuse. Ensuite du
classique, forge de la lame avec beaucoup de surépaisseur,
sortie de la soie avec la guillotine de Glen Stollmeyer, allongement et
affinage de la soie, retour à la lame pour des finitions,
tout en me servant du "Caplan" précédemment cassé
à la trempe comme patron.
J'ai laissé la lame dans la forge chaude éteinte. Je ne
fais jamais cela en général car je laisse le
sèche-cheveux tourner 5 min afin d'éviter une
remontée de chaleur qui pourrait endommager ledit
sèche-cheveux.
La pince spéciale de Glen Stollmeyer et ma
pince coudée ont été très pratique lors de
cette séance. Le marteau boules confirme aussi son statut de
favori. Si on en a qu'un, c'est avec celui là que la forge d'une
lame sera la plus efficace.
Donc on va dégrossir le brut en laissant
autant de surépaisseur que possible ("[...] forge it thick and
grind it thin") et on fera les TTH au four. Recopions ici les derniers
essais de Knife Steel Nerd au sujet des TTH du 100Cr6 à usage
coutelier
- le meilleur compromis dureté résilience a
été obtenu avec une microstructure de départ
obtenue par DET (j'ai pas de traduction, Divorced Eutectoid
Transformation)
- après forge et façonnage grossier (P220 ou 400), 20 min @ 927°C, refroidissement à l'air
- 30 min @ 793°C, refroidissement à l'air
- 30 min @ 793°C, descente au four à 682°C en
370°C/h (donc en 18 min), puis refroidissement à l'air
(c'est celle-ci l'opération de DET)
[en théorie, c'est maintenant que l'acier est le plus mou et
qu'il devrait se laisser percer et usiner; si on fait cela, un petit
recuit de détente devrait être entrepris, disons vers
680°C et refroidissement au four; les étapes d'usinage
n'étant pas mentionnées, on imagine la lame
complètement terminée avant les TTH de cet article; sauf
façonnage finale bien entendu]
- (au fait, j'ai découvert dans un vieux livre scolaire de votre
serviteur qu'on dit austénitisation et non pas
austénisation, j'ai tout faux depuis un temps fou)
- austénitisation 15 min @ 816..829°C et trempe dans une huile rapide
- (un traitement cryo optionnel rapportera environ 0.5 HRc en plus)
- 2 revenus de 1 h entre 149 et 204°C
Si je décode les graphiques avec attention,
- les éprouvettes faisaient 2.5 X 10 X 55 [mm], donc pas
question de réduire les temps puisque mon couteau sera
certainement plus épais
- avec 823°C d'auténitisation et des revenus à
205°C, on tombe vers 61,2 HRc tout en ayant une résilience
pratiquement au maximum avec 27.5 ft.lbs (pied livre, oui c'est des
anglos saxons...). Le maxi est à 28.
- je ferai des passages cryo au congélo à -18°C
uniquement (la dureté augmentera un chouilla et la
résilience baissera un chouilla aussi)
- comme milieu de trempe je commencerai par le goop sur 8 mm (et la lime demi-douce nous dira quoi en penser)
- on devrait avoir environ 7% de carbures et 5% d'austénite résiduelle
12-AVR-2020
Sortie du brut de la forge froide.
- 87 g, pointe 1,52 mm, dos 3,80, tranchant 1,9..2,8, ricasso 4,20 et cul (de la soie) 1,75
Retrait de la calamine avec un vieux disque P40 sur
la meuleuse. Façonnage du contour. J'ai changé
d'idée pour la forme: un peu plus long que le
précédent (+ 4 mm), dos de lame droit mais
légèrement plongeant. Début d'émouture au
back et à main levée. En chemin je me suis
décidé pour une section rhombique à la Yrjö
Puronvarsi. J'ai fait le début du contre-tranchant aux limes
batarde, demi-douce et douce. Les congés entre soie et lame ont
été faits à la lime queue de rat. Quelques
redressages au marteau. Puis j'ai tout repris au back jusqu'à
P400, contre les amorces de rupture. Le brut rentre dans le manche en
chêne déjà fait pour la lame
précédente. Alors je trouve cela joli mais c'est beaucoup
trop de boulot, en gros faut se taper 4 émoutures! Une remarque
concernant l'usinabilité avec de bonnes limes: aucun souci sauf
un peu sur la faible couche de surface (écrouie par le back?).
Alors n'est ce pas du "vrai" 100Cr6? Ou est ce que le fait de laisser
refroidir dans la forge a permis un meilleur recuit d'adoucissement que
les traditionnelles cendres (en copiant un peu le mécanisme du
DET?). En tout cas ce fut une bonne surprise, toutes mes
expériences précédentes que ce soit sur du 100Cr6
ou du 90MCV8 ont montré que la trempabilité
améliorée par les éléments d'addtion font
toujours tremper à l'air mes bruts et cela les rend en
général imperçables avec des fôrets en acier
rapide
- 48 g, pointe 1,07 mm, dos 1,88 (6 mm en dessous, épaisseur maxi de 3,5), tranchant 1,3, ricasso 3,52 et cul 1,75
Pour la trempe et les revenus dans la foulée,
comme je veux tout faire à la suite pour stabiliser le moins
d'austénite résiduelle possible, je vais me garder tout
cela pour le lundi de Pâques. D'ailleurs à cause de
l'excellent compromis dureté résilience annoncé
par les essais de Knife Steel Nerd, je renonce à la trempe
sélective (pour éviter des déformations) au profit
d'une trempe intégrale à l'huile de colza
préchauffée. Mais j'ai attaqué les traitements
antérieurs avant, c-à-d aujourd'hui.
Pour protéger la lame de la
décarburation, j'ai fait les traitements du jour avec une couche
d'acide borique vitrifié
- j'ai mis lame au four en route pour 927°C et je l'ai sortie vers 700°C pour la recouvrir d'acide borique, ensuite
- 20 min @ 927°C (il a fallu 1'30" au four pour remonter)
- au lieu de laisser refroidir à l'air, j'ai utilisé de
l'air pulsé (en sortie d'aspirateur) par peur que la couche
d'acide borique ne soit un peu trop isolante thermiquement
- [le but de ce premier traitement c'est de passer au dessus de Acm et
de dissoudre tous les carbures afin de bien les repartir; le
refroidissement à l'air -jusqu'à la perte totale de
couleur, disons 500°C- est suffisamment rapide pour
également diminuer la taille des grains qui ont bien grossi
durant ces 20 minutes à très haute tenpérature;
pour être sûr de la réduction de la taille des
grains, j'ai préféré accélérer un
peu le refroidissement]
- 30 min @ 793°C (il a fallu 30" au four pour remonter)
- au lieu de laisser refroidir à l'air, j'ai utilisé de l'air pulsé (en
sortie d'aspirateur) par peur que la couche d'acide borique ne soit un
peu trop isolante thermiquement
- [le but de ce second traitement
-un recuit d'affinage de grain ou normalisation- c'est de rester juste
au dessus de Ac1/Ac3 afin d'obtenir une nouvelle réduction
de grains au refroidissement suivant -par changement de structure
cristalline austénite -> ferrite ou martensite; pour
être sûr de la réduction de la taille
des grains, j'ai préféré accélérer
un peu le refroidissement]
- 30 min @ 793°C puis baisse à 682°C en exactement 18'
(soit 370°C/h) suivi d'un refroidissement à l'air (calme
cette fois)
- [ce troisième traitement -un recuit d'adoucissement- est la
DET dont le but est d'obtenir un acier le plus mou et usinable
possible; c'est maintenant qu'il faudrait faire des trous et
éventuellement façonner au back; mais dans ce cas il
faudra ajouter un recuit de détente afin d'éliminer les
tensions internes générées par les retraits de
matière; la structure cristalline de l'acier est alors
constitué de sphères et non plus de plaques; les
sphères comme les piscines à boules des mômes
laissent pénétrer plus facilement les outils; le prix
à payer sera un temps d'austénitisation plus long car ces
sphères se dissolvent moins vite en austénite, mais les
essais semblent montrer que sous les 850..875°C le 100Cr6 ne voit
pas son grain grossir très vite; en échange cette
structure sphéroïdale de départ avant trempe semble
donner les meilleurs résultats en terme de compromis
dureté résilience]
La suite demain...
13-AVR-2020
La lame est pliée à peu près
à la jonction lame - soie. J'avais beaucoup martelé cet
endroit pour redresser après façonnage au back. Y
avait-il des contraintes qui se sont libérées?
La couche vitrifiée d'acide borique est
très difficile à enlever: en grattant avec plein de
méthodes, en tapotant au marteau pour casser... Je regrette la
sableuse du boulot. Faudra éviter à l'avenir si pas de
possibilité de sablage. J'ai enlevé le plus gros et j'ai
fait un petit ponçage manuel à P400. Pour ne pas marquer
l'acier censé être mou, j'ai progressivement
redressé la lame avec le maillet à embouts plastiques sur
billot en bois (en me servant de bosses, creux et plats dans ledit
billot; un peu d'acide borique a encore sauté). Ce qui me
tracasse le plus c'est que sous certains endroits libérés
de la couche vitrifiée, il y a comme des petits
cratères, qu'on voit parfois en cas d'acier
brûlé à la forge ou de forte décarburation.
Hmmm...
Four programmé à 823°C et huile de
colza préchauffée à 70°C (alarme du
thermomètre de cuisine; et c'est là que je me suis
aperçu que cette seconde sonde IKEA déconnait aussi
à présent; comme son ancêtre, ces sondes ne
survivent pas plus de 5 ans on dirait; je me suis dépanné
avec mes thermocouples chinois).
- 15 min @ 823°C (+ 28 s de remontée); l'huile était à 68°C à t=0
- trempe à l'huile de colza à 58°C (le nez perlitique
vers 600°C sur la meilleure doc que j'ai est donné à
t=3 s)
- aucune déformation
- test lime demi-douce sur lame tiède: métal hyper mou!
Décarburation de surface? Ou martensite qui se fait attendre
(M0=240°C, M90=166°C selon la littérature)
- 1 h à -18°C; test à la lime demi-douce vers 40 min
au moment d'allumer le four de cuisine. C'est toujours aussi mou!
[je vous dis pas comme j'ai cogité: roulement
cémenté? C'est pour cela que c'était si facile
à limer après la forge? J'avais décidé de
stopper là si le dernier test à la lime en profondeur ne
donnait rien; et j'avais peu d'espoir vues les précautions
contre la décarburation avec l'acide borique]
- à la sortie du congélo, j'ai limé dans la
surépaisseur du tranchant, et vas y que ça faisait du
copeau, du beurre... Jusqu'à ce que plus rien, ça patine
sévère. J'estime avoir enlevé 0,2..0,3 mm d'acier
de surface. J'ai refait le test dans une autre zone (jointure soie
lame) pour constater le même phénomène: copeaux
puis patinage. Ouf! On continue donc avec le premier revenu.
[Mon bout de ferraille a-t-il perdu son carbone à la forge? Ou
bien juste dans les 15 min d'austénitisation? L'acide borique ne
marcherait pas? Surtout dans la longue phase à 927°C?]
- 1 h à 205°C au four de cuisine avec thermomètre
calibré à l'intérieur (mon four Siemens est un
modèle de précision!)
- refroidissement brusque dans un seau d'eau de pluie à
16.5°C. La lame a pris une couleur jaune un peu brillante dans les
parties que j'avais polies avec la lime
- 1 h à -18°C
- 1 h à 205°C
- refroidissement brusque dans un seau d'eau de pluie à 18.5°C
- 2 h à -18°C
14-AVR-2020
Reprise du "Caplan". J'ai commencé à
enlever l'espèce de calamine de surface avec une lime demi-douce
afin de préserver les bandes (j'ai encore renouvelé le
test de dureté sur l'autre face du tranchant: pareil, d'abord du
copeau puis ça finit par patiner en profondeur). La soie a
été faite à la meuleuse, avec une main
légère. Puis au back, à la table verticale
- reprise du contre-tranchant à P220 et faible vitesse
- reprise des émoutures principales à P120 à faible vitesse et P220
- reprise du contre-tranchant à P400 à vitesse encore plus faible
- reprise des émoutures à P400
- chants du dos et du tranchant à la roue de 250 mm à P220 et 400
J'ai pris mon temps et j'ai eu la main légère. Il reste
de petits cratères apparemment issus de l'acide borique (?). Je
vais finir à la main au P400. J'ai bien envie de faire une
révélation au perchlo histoire d'essayer de "voir" s'il y
a bien une décarburation en surface: on devrait voir un
changement de couleur façon San Mai (3 couches laminées
avec couche centrale dure) si la lime ne m'a pas trompé. Le
tranchant est juste sous les 0.6 mm et avec le contre-tranchant
à presque 2 mm, la lame a l'air super fine alors que dans la
section principale elle est presque à 3.5 mm.
15-AVR-2021
Aujourd'hui je suis sorti à vélo pour
aller me ravitailler à la ferme en lait crû. J'avais un
couteau, mon pliant à lentille "Kipawa", qui a
échappé d'une poche de mon bermuda de trail au retour...
Bois serpent à 25..30 km/h contre le macadam. Devinez qui a
gagné? Il y a un choc au cul (pas grave fonctionnellement) mais
surtout un "poc" et une fissure non loin de la butée de
fermeture... Damned!
Reprise des émoutures du "Caplan" à la
main au P180, 220, 320 et 400. Grace à la couche
supérieure décarburée, ça allait plus vite
que d'habitude. A se demander si ce ne serait pas un moyen très
simple de faire des lames en 3 couches laminées? Polissage aux
disques sisal, coton et flanelle avec respectivement les pâtes
noire, verte et blanche. J'ai passé mon perchlo 25 s au micro
ondes pour le tiédir et j'ai fait 3 bains de respectivement1, 2
et 5 min. Neutralisation entre les bains et polissage à la
paille de fer. Toute la lame est noire sauf le sommet des deux
émoutures qui se rejoignent sur une même face
(décarburée?). Après polissage, on croit deviner
que la couleur noire s'accentue lorsqu'on s'approche du tranchant. Tout
cela va dans le sens de la décarburation de surface que je crois
avoir détecté à la lime. L'aspect de la lame
laisse voir des fines bandes de perlite (claire) et de cémentite
(sombre) parallèles au tranchant. Il faudrait un temps de
révélation plus élevé pour mieux les voir,
par exemple 4 fois 5 minutes comme sur les deux derniers "Bujeault".
16-AVR-2020
J'ai réparé au mieux la fissure dans
le manche de mon "Kipawa" en bois serpent avec de la simple colle
à bois type D3. Les autres marques seront
légèrement poncées plus tard.
J'ai repris un peu la planéité du
morceau d'os supposé de bovin avant d'y tailler longuement une
fente pour faire passer la soie du "Caplan". Idem avec le pommeau en
laiton qui servira à recevoir le matage de la soie. J'ai
décidé d'allonger d'environ 6..7 mm le manche du "Caplan"
par rapport à celui du Mora Eldris que je repompe dans ce
projet. J'ai aussi percé le trou pour le tube de passage
dragonne à 6 puis 6.1 mm avant de faire le petit
décrochement dans la soie (pourquoi elle a pas
décarburé elle? Elle est inusinable) qui permettera de le
contourner. A propos de soie, il a fallu une fois de plus la remettre
un peu dans l'axe de la lame. Sans doute le polissage à la main
d'hier qui nous a un peu décalé tout ça.
17-AVR-2020
J'ai gratté les surplus de colle à
bois séchée sur le manche du "Kipawa". C'est pas trop mal
et ça a l'air assez solide.
J'ai poli jusqu'à P2500 la face avant de la
ferule en os. Je n'ai pas osé polir au disque de peur de salir
de façon irréversible l'os. J'aurais dû faire un essai sur
la face cachée. La face extérieure du pommeau en laiton a
été égalisée aux limes. Cette pièce
issue de la poubelle de l'usine avait de petits fraisages qui rendaient
la face non plane. J'ai accentué à la lime le chanfrein
qui recevra la soie matée. J'ai repris au chalumeau à gaz
la soie: presque au rouge dans la zone à mater et au delà
du "bleu" gorge de pigeon sur le reste afin de tenter d'y faire de
petites encoches rondes pour favoriser l'accroche de la colle.
J'ai fait le logo sur l'émouture gauche
de la lame, contrairement à mon habitude car l'émouture
droite était trop accidentée, vraisemblablement à
cause de l'acide borique. J'ai poursuivi avec
l'affûtage grossier uniquement à la meule à eau
à main levée avec un angle de 15° environ par
côté. J'ai
peur des accidents si j'affûte après montage car le talon
de la lame est très proche de la ferule. Nettoyage des
surfaces à coller avec l'acétone et préparation
d'un petit coin de bois pour mieux coincer la lame dans le manche
(trou trop gros?) au moment du collage. Préparation de la colle
époxy à prise lente, enduction des surfaces, bouchage du
trou de la dragonne pour éviter les coulures et les fuites et
mise assez compliquée sous presses. Essuyage des excès
à l'acétone au niveau de la jonction lame ferule.
18-AVR-2020
J'ai essayé d'adapter la forme verticale du
manche du Mora Eldriss à la longueur à peine plus grande
du manche du "Caplan". Et ce n'est pas très satisfaisant. Le
dessin d'un couteau tient dans le millimètre entre le beau et le
moche. J'ai découpé cette forme sur papier pour la
reporter sur le manche.
J'ai sorti le "Caplan" des presses et avec un ciseau
à bois j'ai retiré l'époxy qui a coulé dans
le chanfrein destiné à recevoir la soie matée.
Ensuite j'ai réduis la longueur de la soie à un
dépassement de 1.5 mm et je l'ai longuement matée dans
son logement. J'ai sorti le back, fait des tracés et longuement
travaillé sur le manche le faisant évoluer en permanence
et s'éloigner du Eldris... Et je sens bien que c'est en train de
m'échapper... Le manche va être trop gros par rapport
à la lame, mais c'était voulu pour bien remplir la paume,
par contre sa forme est bizarre. Moche quoi. Les congés entre
les angles droits des ferule et pommeau sont trop petits. On verra ce
que ça donnera après les finitions ou bien que je sois
satisfait ou fatigué. J'ai aussi poli au back le pommeau
jusqu'à P400.
19-AVR-2020
J'ai entièrement repris le manche du "Caplan"
pour aller à nouveau vers une forme très lisse non
accidentée, de section ovoïde, façon Pekka Tuominen.
Beaucoup de finition à la râpe et à la lime
demi-douce pour progresser lentement. Cela m'a pris beaucoup de temps.
Chanfrein à 45° dans le trou, sciage, mise à taille
et matage du tube de passage dragonne. Nettoyage, polissage au disque
coton et pâte spéciale bois 40 microns, coupe des
dernières traces d'époxy au ricasso au ciseau à
bois, nouveau nettoyage, masquage et teinte à la paille de fer
dissoute dans du vinaigre blanc. La forme est pas mal mais la position
de la lame par rapport au manche n'est pas très
réussie je pense. La faute au façonnage de
départ, complètement HS qui a enlevé trop de
matière là où il m'en fallait plus tard...
20-AVR-2020
Egrénage du manche du "Caplan" à la
paille de fer et étalées sur une grosse journée, 6
couches d'huile de tung, les 3 premières diluées à
50% avec de la térébenthine et les 3 dernières
pures (avec chaque fois 1.5% de siccatif). Avec la teinte un peu
irrégulière en fonction des veines et de la
densité du chêne, je le trouve très beau d'un coup
ce bois... Les tanins du chêne réagissent vraiment bien
avec le fer dissout dans le vinaigre blanc.
21-AVR-2020
Dernières couches: deux de cire de carnauba,
deux de cire d'antiquaire. Affûtage aux pierre à eau
Haïdu P180 et 280, pierre DMT 320 et petit coup de cuir avec
pâte 2 microns. Création du tableau dans la page galerie.
27-AVR-2020
J'ai fini par enfin pouvoir lire le livre sur les
couteaux japonais ("The knifenerd guide to japanese knives" par Kevin
Kent ISBN 9781999390600) que je me suis offert pour Noel. J'y ai appris
que Takayuki Shibata affûte ses couteaux à 800 (J800 c'est
environ P1000, J8000 n'a pas d'équivalent en
garanulométrie de papier européen mais c'est bien au
dessus de P5000; selon mes recherches sur le Net) sur le tranchant
gauche et 8000 sur le droit. J'ai supposé une
granulométrie japonaise et que les côtés gauche
droite sont ceux lorsqu'on tient le couteau en main. J'ai donc fait un
essai sur mon dernier "Caplan" (photos faite et galerie mise à
jour) avec du P320 à gauche et de la pierre de coticule belge
à droite (5000..8000). Je ne constate hélàs aucune
réelle différence à la coupe. Mais je ne suis pas
le Mozart de l'affûtage.
01-MAI-2020
Contre l'ennui et à côté des
tâches quotidiennes, j'ai commencé par travailler sur deux
étuis en cuir
- un premier classique, plié en deux, 3 couches de martyr, passant de ceinture monobloc pour le "Bujeault 107%" en 90MCV8
- un second de type scandinave pour le dernier "Caplan" avec fourreau en bois en deux parties
Pour le premier, rien de spécial à
signaler, au soir j'en suis à avoir creusé la rainure
pour la couture avec le marquage des trous, une grande
partie teinte, le passant de ceinture cousu. Cuir tanné
végétal.
Pour le second, un type que je réalise la
première fois de ma vie, j'ai maladroitement creusé au
ciseaux à bois deux morceaux de platane d'environ 8 mm
d'épaisseur. Après un peu de ponçage à
plat, j'ai collé le tout pour former un fourreau qui
après affinage devra être cousu dans un étui avec
une seule couture à l'arrière. Ici je prévois de
réutiliser le cuir d'un vieux cartable. Pas sûr qu'il se
laisse bien conformer comme du tanné végétal...
02-MAI-2020
J'ai presque fini le premier étui en cuir pour le "Bujeault 107%".
- perçage des trous
- seconde rainure pour relier les trous sur la face cachée
- mouillage, teinture de la zone de couture ainsi que le martyr (dedans comme dehors)
- marquage avec la roulette, couture point sellier, dernier marquage avec la roulette
- mouillage, arrondi des angles, lissage et introduction du couteau avec film plastique alimentaire pour la protection.
Le manche pénètre peu mais je voulais un port très haut pour ce couteau.
J'ai dégrossi le fourreau en bois au couteau.
D'abord avec le "Caplan" lui même (je trouve super d'utiliser un
couteau comme outil pour faire son propre étui) puis avec mon
pliant "Kipawa". Je voulais voir la tenue du tranchant de ces deux
aciers. Sur le platane, elle est excellente pour les deux, notamment le
supposé XC100 (d'une lime) du "Kipawa" austénitisé
par induction sur lequel j'ai toujours des doutes. Le 100Cr6 du
"Caplan" avec les TTH de Knife Steel Nerd ne prête pas le flan
à la moindre. La mécanique (pivot 3 mm et palette,
bois serpent) du piémontais encaisse très bien les
efforts. Cependant deux remarques
- le tranchant du "Caplan" est trop gros juste derrière le fil,
il vaudrait mieux le reprendre. Il est sans doute hyper costaud mais
oppose un peu trop de résistance à la
pénétration dans des objets assez durs
- la pointe du "Kipawa" était pliée/enfoncée. Sans
doute une des conséquences de la chute récente en
vélo que mes yeux de 48 ans sans lunettes n'ont pas vu l'autre
fois. Rectification rapide à la lime puis à la pierre
Fallkniven. Ces deux faits confirment que la trempe n'a que peu prise
à la pointe, comme semblait déjà le
révéler le perchlo ainsi que mes tests de dureté.
J'ai souvent eu des problèmes de trempe aux pointes (sur des
aciers non alliés) au four, comme à la forge et à
l'induction. Pourtant je trempe toujours pointe en premier. C'est
vraiment cette zone qui doit se refroidir hyper vite à la sortie
et me fait louper le nez perlitique. Je ne vois guère comme
solution que de laisser plus de matière ou un peu surchauffer la
pointe (ou laisser tomber les purs carbone)
Le fourreau a été poursuivi à
la râpe, puis à la lime demi-douce et enfin avec une
vieille éponge abrasive Norton deux grains ("gros" et "fin")
ultar rincée. Ce fut beaucoup plus qu'avec le backstand mais
j'avais envie d'utiliser des outils à main. Cela permet d'y
aller très progressivement. Comme je veux former le cuir
mouillé autour du fourreau je lui ai mis une petite couche
d'huile de lin afin qu'il n'absorbe pas trop d'humidité. Pour le
cuir, on reste dans l'esprit "récup" du "Caplan" (os
trouvé, chêne de poutre offert, roulement de la benne...)
avec mon vieux cartable. Le morceau choisi et découpé est
très déformé et plein de trous de couture mais
ça ne fait rien. Il est actuellement en train de tremper dans
l'eau pour essayer de le ramollir et de le mettre à plat.
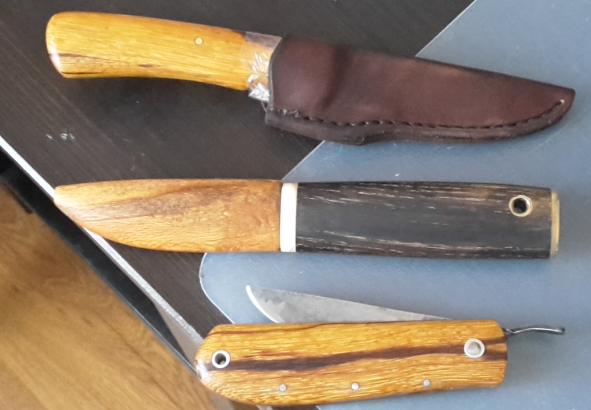
L'étui cuir en train de sécher, le fourreau en bois huilé et la pointe du "Kipawa" réparée.
03-MAI-2020
Fabrication d'un étui de type scandinave pour
le "Caplan". J'ai regardé un tuto sur YouTube et j'ai dû
me taper chaque trou avec le vieux poinçon de mon
grand-père (un peu affûté et redressé pour
l'ocsasion). Le moins qu'on puisse dire, c'est que pour une
première expérience, j'ai tout fait pour me
dégoûter en décidant d'exploiter le cuir d'un vieux
cartable. Celui-ci ne se comporte absolument pas comme du tanné
végétal: quasiment pas le moindre de gré de
conformation. Il faut tirer fort sur le fil pour forcer le cuivre
à suivre la forme du manche puis du fourreau en bois. A cause de
la seconde aiguille qui passait toujours dans le fil au lieu de
l'éviter (trou trop serrés), la mort dans l'âme,
j'ai renoncé au point sellier. Ma ligne de couture est un peu
irrégulière, j'ai passé avant l'abat-carre sur
l'entrée intérieure et extérieure de
l'étui. Finition avec le petit backstand Peugeot, teinture de la
couture et séchage.
04-MAI-2020
Sortie des "Bujeault 107%" et "Caplan" de leur
étui. Le "Bujeault 107%" entièrement recouvert de film ap
assé deux jours dans l'humidité. Un tout petit bout de
son tranchant est rouillé orange. C'est parti avec de la paille
de fer mais elle reste de la coloration localement. Le "Caplan" n'avait
que le manche qui était protégé, la lame a
passé la nuit dans le fourreau et l'humidité
environnante: tout le tranchant est orange. Là encore c'est bien
parti avec de la paille de fer. Idem il reste des traces de
coloration noirâtre. Bon de toute façon, je voulais
"casser" l'épaulement derrière tranchant pour l'affiner...
Plus tard en fin de journée, un coup
d'abat-carre sur la couture de l'étui scandinave avec teinture
et lissage ainsi que nouvelle teinture de l'entrée du premier
étui (tout est légèrement humidifié avant).
Et pour finir en soirée, une couche de graisse "Le Phoque" sur
chaque étui.
J'ai encore débité deux planchettes de
12 mm dans une branche du cerisier pleureur abattu chez mes parents,
hsitoire de voir ce que ça raconte en dedans: bof on dirait du
buis, tout blanc sans la moindre veine. Il est encore bien humide et
commence à fisssurer de partout.
05-MAI-2020
J'ai eu finalement assez de motivation pour tenter
d'affiner le tranchant du "Caplan" mais pas assez pour sortir le back.
Du coup j'ai essayé avec une pierre de coticule de 150 mm. Bien
que le grain soit très fin (de 5 à 8000 selon le morceau
de caillasse chopé), il est très agressif et
enlève beaucoup de matière. Le tout avec de l'eau. Que
demande le peuple craignant des revenus intempestifs dus à des
machines?
Très vite le tranchant devient convexe au
niveau de l'épaulement qui sépare le tranchant de
l'émouture. Sous la pulpe des doigts tout semble devenu
sensiblement plus fin. Pas pour mon pied à coulisse cependant.
Les "lignes de niveau" à 0.5 et 0.7 mm me semblent encore
exactement au même endroit! C'est juste l'arète entre
émouture et tranchant que j'ai dû "casser". Petit essai
sur du bois: ça pénètre bien mieux, la lame est
plus mordante, c'est assez bluffant. Le fil reste bien tranchant. La
bel finition matte du perchlo a disparu dans la zone du tranchant. On
va attendre avant d'essayer éventuellement de la refaire,
dès fois que j'ai encore des élans d'affineur qui me
reprennent...
06-MAI-2020
Ça manque sérieusement de motivation,
putain de Covid! J'ai retrouvé de petits oeillets en laiton
d'environ 4 mm dans mes affaires coutelières. J'ai percé
l'étui du "Caplan" dans la zone prévue à cet effet
pour y placer l'oeillet par déformation plastique (il a
aussi de petites griffes). J'y ai mis un anneau élastique de
porte-clefs. Faudra faire encore un passant de ceinture et ça
devrait être fini.
07-MAI-2020
J'ai trouvé une chute de mon vieux cartable
parfaite pour y faire le passant de l'étui du "Caplan":
découpe, abat-carre, égrénage des zones à
coller, teinte du chant, collage. J'ai trouvé un ancien tube de
colle UHU "Kraft" dont la notice indique la possibilité
d'encollage immédiat en 1 face et après séchage en
2 faces (type néoprène) et je l'ai essayé.
Ça marche plutôt très bien et cela ne sent pas
aussi fort. Ça peut dépanner mais je crois qu'il faut
toujours rester avec la colle la plus spécialisée
possible: bois avec du bois, néoprène avec du cuir et
éviter la bi compsant à toutes les sauces...
08-MAI-2020
Perçage des 3 pauv' trous de couture du
passant à 1.8 mm, petite coup de rainette pour noyer le fil,
mouillage, teinture et pour finir, couture point sellier et
voilà. On enfile l'anneau et c'est opérationnel!
12-MAI-2020
Un collègue de la forge associative m'a donné 2 objets
- un gros ressort d'origine Mercedes (sans doute de classe E) qui
a 14.1 mm de diamètre de fil. Le plus gros en ma possession
- une grosse vieille lime tiers point de 30 cm, 22 mm de
côté de marque Talabot Duteil France et avec une sorte
d'écusson sur une autre face
13-MAI-2020
Après presque 2 mois, ma petite pompe
à eau de Chine a fini par arriver. Rigoureusement identique
à la défaillante, elle me sert à refroidir le
serpentin de mon chauffage par induction. Je l'ai cablée dans la
foulée en essayant de faire une installation plus
sérieuse que la première.
14-MAI-2020
La possibilité de pouvoir enfin refaire des
auténitisations par induction trotte dans ma tête. Je
ferai bien un nouvel essai avec du 90MCV8 qui semblait mieux
répondre à ce traitement. Pourquoi pas sur une lame
taillé dans la masse, comme avant? Ou alors sur un pur carbone
type XC100? Je me suis souvenu que j'avais toujours voulu refaire une
copie d'Enzo Elver. Avant d'offrir le vrai à mon frère
j'avais scanné le contour. J'ai aussi songé que
plutôt que d'y faire 6 trempes sélectives qui font
remonter les pointes de 8 mm au final (et dont il faut anticiper le
contour au départ), je pourrai faire des trempes
intégrales, sauf la dernière en sélectif.
15-MAI-2020
J'ai ressorti mon contour d'Enzo Elver des archives pour le
coller sur une tôle fine afin de se faire un patron durable. J'ai
tout de même allongé la lame de 4 mm avant de
façonner le tout au back. Il est très proche de mon
modèle "Kegaska" et je le baptiste donc "Kegaska 2.0". Je vais
le tailler dans un plat de 90 MCV8 de 3.3 mm sorti il y a longtemps de
la benne de mon usine. Une chute si parfaite que je n'avais pas voulu
la forger, avec de belles faces bien parallèles. En la
recherchant je suis retombé sur l'espèce de grosse
râpe qui m'avait servi à faire le "Mule" de Kyley Harris
(voir
galerie AVR-2015). Je pense y
tailler un second exemplaire obtenu à la forge. De cette
façon je peux récupérer un petit morceau restant,
trop court, mais dont je devrai réussir à suffisamment
amincir la semelle pour obtenir le contour complet.
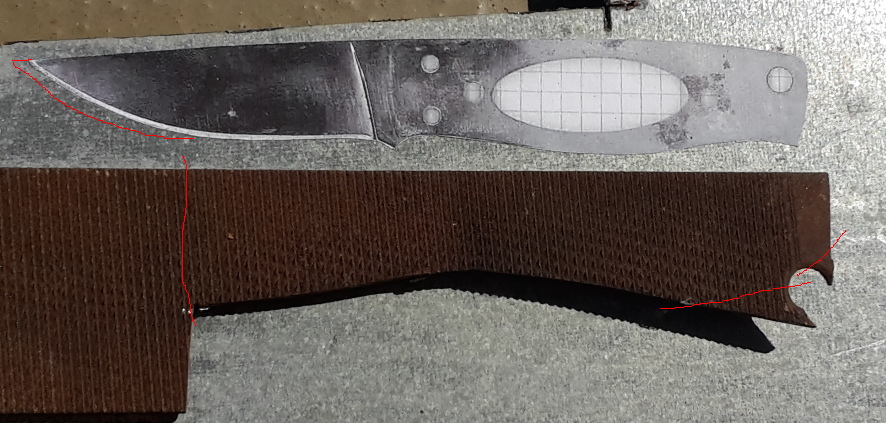
Les lignes rouges montrent la pointe allongée de 4 mm et les
coupes à la disqueuse dans la grosse râpe de brocante.
Après le "Caplan" pas assez agressif sur le
bois, je songe à faire au "Kegaska 2.0" des
émoutures scandinaves qui descendent à 0 comme sur
l'Elver original qui a 14° de demi-angle au sommet. En plus en
laissant un gros tranchant avant TTH, je devrai avoir moins de
déformation et moins de refroidissement entre sortie d'induction
et bac de trempe.
J'ai donc reporté le profil sur ma chute de
90MCV8 et je l'ai façonnée au back. Le back étant
sorti, j'en ai profité pour amincir au P220 puis 400 le
tranchant du dernier "Caplan" en 100Cr6. J'ai bien pris soin de ne pas
chauffer et ça a marché, pas la moindre coloration. Par
contre, mon pied à coulisse m'a montré que je n'ai pas
aminci grand chose derrière le tranchant. Je suis
péniblement arrivé à 0.5 mm, juste avant de voir
la batterie du pied à coulisse mourrir. J'ai fini de le polir
à la main à la pierre de coticule pour voir apparaitre
des défauts de planéité de surface. Je vais
sûrement tout reprendre à la pulpe du doigt et papier
de 800 peut-être.
Le brut du "Kegaska 2.0" est très lourd.
Comme sur le Elver du commerce je vais tacher d'enlever pas mal de
matière dans la semelle. Mais je ferai cela en même temps
que je percerai la semelle du brut qui sera forgé. La prochaine
étape sera l'ébauche d'émouture scandinave, sans
doute demain matin. Mais comment faire mes tracés avec
l'affichage du pied à coulisse en panne?
On passera ensuite (je ne sais pas quand)
à la forge du second brut. Il faudra d'abord sortir les
arètes à la meuleuse d'angle, après une
première chauffe, pour ne pas les marteler en permanence dans la
surface.
PS: en regardant une recette sur YouTube, j'ai vu
par hasard des os à moelle. C'est bien cela que j'ai
trouvé dans ma pelouse et qui a servi à faire la ferrule
du dernier "Caplan". C'est toujours du veau ou du boeuf selon Internet,
donc bien du bovin comme supposé.
16-MAI-2020
Le pied à coulisse fonctionne à
nouveau avec un affichage erratique: la pile sans doute mais qui me
redonne au moins de quoi tracer le tranchant du "Kegaska 2.0". Le plat
fait 3.35 mm et j'ai décidé de laisser 1.5 mm de
tranchant avant TTH. Petit marquage de la ligne d'attaque de
l'émouture avec lime et guide. Retour au back encore sorti et en
avant pour une pré émouture scandi à 14° de
chaque côté avec mon support et la table inclinée:
P120 à 2800 tr/min, 220 à 2000 tr/min et 400 à
1500 tr/min. Bon je dois être une brêle, y a pas
d'autre explication. Mes émoutures sont
dissymétriques, sont remontées plsu en arrière
vers le ricasso malgré le marquage de départ et il
reste à peine entre 1 et 1.20 mm de tranchant...
Je voulais faire les opérations de
perçage des deux "Kegaska 2.0" en même temps mais pour
combler le reste de la matinée du samedi, j'ai finalement
percé la semelle du modèle taillé dans la masse.
J'ai complètement oublié de peser la lame avant et
après perçage pour voir le gain de poids. Bref j'ai mis 2
trous de rivets à 3 mm et un de tube passage dragonne à
6. J'ai fait d'autres trous et des pré-trous avec le forêt
carbure de 3 mm avant d'en agrandir 4 à 11 mm. La perceuse Bosch
arrive à ses limites par rapport à la perceuse du
boulot que j'utilisais à la pause. Heureusement le fôret
était bien affûté, le 90MCV8 bien recuit et que
j'ai mis moulte huile de coup. Avec la disqueuse et beaucoup de travail
de lime j'ai fait 2 grosses découpes pour gagner du poids. Le
centre de gravité est juste devant le premier trou de rivet et
c'est déjà pas assez proche du ricasso. Avec ce qui
manquera devant après émouture finale et ce qu'il y aura
en plus derrière avec les plaquettes, ce sera pire... Je vais
voir si j'ai le courage d'aller gratter encore dans les recoins des
découpes. Vive les semelles amincies!
17-MAI-2020
Dimanche après-midi de glande. Au lieu
de forger le brut du second "Kegaska 2.0", j'ai continué mes
recherches dans mes 3 ouvrages de référence, à
savoir le bouquin de Verhoeven, celui de Landes et le site de Larrin
Thomas, Knife Steel Nerds. Chaque fois que je me replonge dedans je
découvre d'autres choses. Quelle complexité les TTH, avec
tant de conditions antagonistes. Le plus efficace plutôt que mes
plans théoriques ce serait évidemment de vrais essais
avec des mesures scientifiques...
Bon bref, je veux essayer mes trempes par induction
après un relatif succès avec les deux derniers
"Bujeault". Un des résultats c'est que le 90MCV8 semble
répondre bien plus favorablement à
l'austénitisation par induction. rappelons que j'avais fait au
moins 6 trempes sélectives à l'eau + 5% de sel. Les
pointes étaient remontées de 8 mm et il avait fallu
laisser de la matière pour corriger la forme.
Pour garder de la dureté, les revenus étaient
passsés de 200 à 150°C. En vrac
- mes recherches indiquent des trempabilités relatives (par
rapport à XC75-XC80 situé à 1) à 800°C
de 1.27 pour le 100Cr6 et 2.39 pour le 90MCV8
* la profondeur de trempe sur le 90MCV8 doit être très supérieure au 100Cr6
* C'est vraiment un acier qui doit très
bien prendre la trempe à l'huile (quand on est assez haut pour
l'austénistisation; moi je vais rester à l'eau
salée vus les derniers essais, mais j'ai peut-être un poil
plus de temps pour rejoindre le bac de trempe et malgré tout
réussir à tremper la pointe...)
- je compte saler l'eau à 10% cette fois (ça semble être la référence)
- la trempabilité est fortement impactée par la taille de
grain: plus elle est petite moins on trempe en profondeur: comment
obtenir une trempe à coeur avec un grain ASTM14..15? Sur un
tranchant assez fin ça pourrait passer mais celui-ci n'ayant pas
assez de masse il refroidit trop vite
* peut-être que mes émoutures scandinaves avec 1..1,2 mm au tranchant seront un bon compromis?
- la structure de départ avant trempe influe la structure après trempe
* dans l'ordre de la meilleure à la moins
bonne: la martensite (donc après une première trempe), la
perlite, un recuit avec des graphites sphéroïdaux
(état de livraison standard optimisant la facilité
d'usinage)
* le problème c'est les temps
d'austénitisation qui sont exactement inverses: les graphites
sphéroïdaux demande le moins de temps
d'austénitisation alors que la structure à grains de plus
en plus fins (à cause de trempes multiples) de la
martensite tend à devoir austénitiser à l'infini
* bref pour combattre la déformation, je
compte tremper intégralement, disons 3 fois avec une trempe
sélective finale sur 1/3 de lame
* pour les durées, à cause de la
relatiuve grosse quantité d'alliage et de la température
d'austénitisation très faible, 10 minutes ne seront pas
encore assez j'en ai peur, surtout vers les dernières trempes
lorsque le grain s'est affiné. Que faire?
- après chaque trempe intégrale, il faudra bien descendre
sous Ms (approx vers 240°C, M90=? -90% de martensite formée-
on va dire T ambiante) pour avoir un maximum de martrensite comme
structure de départ de la trempe suivante
- du côté magnétique, plus on chauffe vite, plus
les températures de transformations Ac1 et Ac3 sont
décalées vers le haut, avec l'induction 25 à
40°C facile selon moi
- donc au départ on se dit "super ça nous fera
727+25..40" mais cela ne sert à rien car c'est justement parce
que la structure martensitique n'est pas obtenue qu'on monte aussi
haut. Une fois stabilisé, l'ensemble va sans doute s'auto
réguler vers Ac1-Ac3
- une courbe TTT de 90MCV8 donne Ac1=720°C et Ac3=780°C
- une formule empirique de Verhoeven donne Ac1=720°C (pour le 90MCV8)
- quoiqu'il en soit le 90MCV8 est selon les formules empriques
l'acier avec les températures de transformations les plus
basses, vient ensuite l'XC100 dont j'espère que la plupart de
mes limes sont un cousin (et qui explique ma seconde lame en cette
espérée matière pour un essai avec l'induction)
Et pendant que j'y étais, j'ai relu le
paragraphe sur le recuit par DET de Verhoeven pour essayer de
comprendre pourquoi ça avait marché sur du 100Cr6 et pas
sur du 90MCV8. Larrin Thomas avait utilisé la même recette
(à savoir 795°C-680°C) sur du CruForgeV sans que ses
résultats soient prodigieux. Je pense que ça vient
simplement de la position de Ac1 par rapport aux limites haute et basse.
- cas idéal utilisé par l'industrie, donc une bonne
source: 100Cr6 Ac1 750°C, DET 795-680°C, donc +45°C et
-70°C (Verhoeven parle d'une amplitude approximative d'une
cinquantaine de dégrés autour de Ac1)
- essai moyen avec le CruForgeV: Ac1 selon la formule de Verhoeven
736°C, avec les valeurs ci-dessus, on aurait une DET à
781-666°C, c'est proche
- mais pour mon 90MCV8 l'autre fois, Ac1 720°C, soit une DET
"théorique" à 765-650, peut-être la cause du ratage
car 30°C ça commence à être significatif tout
de même; à essayer un jour avec la même rampe de
370°C/h ou une plus lente (à cause de la trempabilité
supérieure du 90MCV par rapport au 100Cr6; le CruForgeV est
à 1.52 bien plus proche des 1.27 de trempabilité relative
du 100Cr6)
Bref je vous noie, je vous perd, mais écrire
et dormir me permet de digérer, d'intégrer et de
régler mon pifomètre pour des essais à des points
de départ pas trop pourris. C'est balaise les TTH
théoriques tout de même... Surtout si on s'impose en plus
une température trop basse pour l'austénitisation...
18-MAI-2020
C'est vrai que je ne vous avais pas dit que grace au
Covid19, j'ai grasse mat' tous les lundis de mai... Short time work
parait qu'on dit en angliche, pour chômage partiel...
J'ai forgé environ 2 heures le "Kegaska 2.0"
en brut d'une très large râpe d'origine inconnue,
peut-être pour de l'alu ou un métal tendre. J'ai
chauffé le lopin au rouge puis je l'ai laissé noircir
dans la forge éteinte et fermée avant
d'éliminer les dents avec la meuleuse d'angle. J'ai
été surpris de la quantité de métal restant
après élimination des dents: à peine 2.85 mm
environ à l'endroit le plus fin...
Comme il y avait peu de métal, j'ai
essayé de forger au plus près de la forme finie sans
émouture à la lame et avec une semelle amincie. Long...
Et obligeant à retourner souvent à la forge. Pas
très efficient en fait de chercher le dernier
pouillième... Résultat: il me manque 4 mm de lame et me
voilà donc à pouvoir y faire exactement la forme courte
de la lame du Elver du commerce mais surtout le métal a
sacrément minci... J'ai peur que le dos de lame soit à
peine vers les 2 mm. On verra bien à la sortie des cendres.
Pour finir après un planage appliqué
au marteau (Merde! J'aurai dû y mettre des coups de chasse
à parer!) j'ai fait 3 normalisations de la lame à la
forge et à l'air pulsé suivi d'un recuit principalement
de la semelle, dans les cendres.
20-MAI-2020
Allez on sort de la léthargie. J'ai agrandi
les découpes d'allègement dans la semelle du "Kegaska
2.0" en 90MCV8. La lime, une école de patience... Et une ampoule
au pouce.
Sortie du back et de la meuleuse d'angle. Petit
grattage de la calamine sur le "Kegaska 2.0" forgé,
traçage du contour et façonnage du contour au mieux (suis
pas à 100% du profil original) au back: P120, 220 et 400 +
cylindre Kirjes en 220 et 400 pour les rayons très petits. J'ai
aplani au mieux au marteau, puis j'ai rectifié les 4 faces (2
pour la semelle et 2 pour la lame) à P60 sur la table verticale
du backstand. J'ai cassé à main levée (à
cause d'une épaisseur de lame non constante) l'angle du
tranchant en y mettant une émouture scandinave grossière
et convexifiée. Enfin j'ai percé et ébavuré
la semelle: 2 trous de 3 mm pour des rivets, 1 de 6 mm pour le tube
passage dragonne et 4 de 10.5 mm pour allègement. Je ne ferai
pas de fenêtre car la semelle est déjà amincie.
Aucun problème de semelle imperçable pour cause de recuit
pourri ou d'acier blindé en élements d'alliage. Bilan
- pointe 1,26 mm
- tranchant 1 .. 1,26 mm
- dos de lame 2,23 mm au maximum
- ricasso 2,31 mm
- cul de semelle 1,44 mm
21-MAI-2020
Mes brioches qui poussent (enfin de la levure
fraiche trouvée en magasin!), aller faire du vélo? Non je
préfère surveiller mes petits déjeuners à
venir. Vélo cet après-midi malgré les fortes
chaleurs annoncées et garage pour polissage à la main...
- "Kegaska 2.0" en 90MCV8 dont les faces rectifiées me faisaiten
espérer un travail minimal, ma cache! Alors oui faces
parallèles mais profondes traces, très longue
séance au P120, 180, 220, 320 et 400. Ouf!
- "Kegaska 2.0" forgé: bon degrossissage à la lime douce
en travers et séance au P120, 180, 220, 320 et 400. Ouf bis!
- avec tout ce papelard abrasif sorti, reprise des émoutures du
dernier "Caplan" en 100Cr6 après affinage récent de
celles-ci au back, sortie des rayures à P180, 400, 800 et 2500.
C'était presque plus facile que sur le 90MCV8 recuit
malgré les 61 HRc, mais il faut dire que la surface était
déjà bien finie.
24-MAI-2020
A cause de l'annulation du salon Coutellia (ou un
autre je ne sais plus...), Eurotechni proposait d'offrir les frais de
port. J'en ai profité car depuis quelques temps ils vendent une
peinture de protection contre la décarburation à haute
température. Même effet que le feuillard inox. Vu mon
échec avec l'acide borique sur le 100Cr6 vers 920°C
pendant 30 min (dissolution des carbures au dessus de Acm) avec
mon dernier "Bujeault 106%", je me suis qu'il fallait eessayer avec un
truc plus sérieux. Le pot est plutôt cher et il faut
trouver du xylène pour nettoyer le pinceau après
application, mais je ne trouverai sans doute pas meilleure offre
facilement. Pour atteindre le montant minimum afin de profiter de
l'offre, j'ai complété avec un peu de ferraille bon
marché: T7Mo, X50CrMoV15 et C130.
25-MAI-2020
Peut-être mon dernier lundi de chômage
partiel. On en profite pour tremper les deux "Kegaska 2.0" avec
l'induction et de nouvelles stratégies que voici
- Non plus mais 4 austénitisations à l'induction au total
- avec les trois premières, trempe intégrale à l'eau salée à 10 % (avant c'était 5%)
- pour la dernière trempe sélective à l'eau
salée à 10%; J'espère ainsi éviter la
remontée de la pointe
- pour les durées d'austénitisation, observation du
courant absorbé: lorsque celui est stable j'ai envie de croire
que toutes les transformations possibles dans l'acier (dissolution de
carbone, formation d'asuténite et de carbures) à la
température atteinte sont faites; Si l'acier de la grosse lime
de brocante est "simple" contrairement au 90MCV8 plus allié,
cela devrait durer plus longtemps avec ce dernier; Il est d'ailleurs
notoire qu'on recommande des temps d'austénitisation plus longs
avec les aciers faiblement alliés qu'avec les "purs" carbone.
J'ai tout installé au mieux avec un
système pour que la lame tienne seule et sans mouvement dans la
bobine. L'eau de refroidissement est pure pour préserver la
nouvelle pompe. L'eau salée est de l'eau de pluie dans une
bouteille coupée pour les trempes intégrales et un bac
pour la trempe sélective. J'utilise mon établi Workmate
pour mettre les bacs de trempe le plus près possible de la
sortie de la bobine. J'ai un thermocouple pour surveiller les
températures des liquides dans les trois bacs. Un chrono pour
mes relevés.
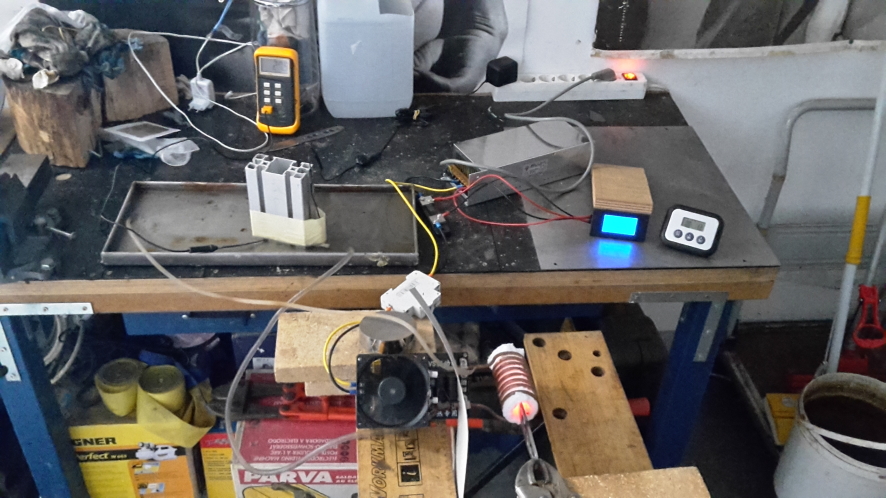
On distingue ce que j'ai décrit ci-dessus et aussi la pince
étau qui tient la lame en reposant sur une brique.
L'établi étau Workmate ouvert pour un accès
rapide vers le bas et le bac de trempe.
Voici un tableau
pour les auténitisations du premier "Kegaska 2.0" en 90MCV8 de
3.3 mm. Le courant à t=0 n'est pas constant car je n'ai pas
toujours appuyé au même moment sur le chrono, ne pas en
tenir compte.
courant absorbé [A] |
Temps t=0 |
t=1 [min] |
t=2 [min] |
t=3 [min] |
t=4 [min] |
t=5 [min] |
t=6 [min] |
t=7 [min] |
t=8 [min] |
t=9 [min] |
t=10 [min] |
température eau de trempe salée à 10% [°C ] |
durée austénitisation approx. [min] |
austénitisation 1 |
10.80 |
9.58 |
9.44 |
9.38 |
9.32 |
9.30 |
9.28 |
9.26 |
9.25 |
9.23 |
9.22 |
18.6 |
11 |
austénitisation 2 |
12.16 |
9.65 |
9.50 |
9.38 |
9.34 |
9.31 |
9.29 |
9.28 |
9.27 |
9.26 |
9.26 |
24.5 |
11 |
austénitisation 3 |
12.00 |
9.66 |
9.42 |
9.35 |
9.32 |
9.30 |
9.29 |
9.28 |
9.28 |
9.28 |
9.28 |
31.3 |
11 |
austénitisation 4 |
10.73 |
9.47 |
9.34 |
9.28 |
9.26 |
9.25 |
? |
9.24 |
9.24 |
9.24 |
- |
17.8 |
10 |
Hormis t=0 que j'ai essayé de mettre lorsque
I=12 A sur le second essai, on voit qu'un régime stationnaire
s'installe. Les faibles évolutions cependant significatives vers
la fin semblent me dire qu'il y a bien encore de lentes transformations
qui se passent après 5 minutes dans le 90MCV8. Après
chaque trempe, j'attends d'avoir l'acier vers 20°C afin d'être
sûr d'avoir une microstructure martensitique pour la prochaine
austénitisation, gage d'une meilleure réponse du
traitement thermique et d'un grain plus fin avec des carbures
répartis de façon homogène. Aucune casse, un acier
très blanc avec une calamine qui explose presque dans l'eau. La
lame est restée bien droite sauf après la trempe
sélective qui l'a fait fortement dévier à gauche
vers la pointe. L'aspect de l'acier est aussi moins blanc qu'avant. Les
yeux me disent que cette trempe n'était pas optimale. Lame au
congélo à -18°C à 15h19.
A cause de la faible taille du bac de trempe pour la
dernière trempe sélective, j'ai été
obligé de saisir le couteau autrement avec la pince étau
et donc de le placer autrement dans la bobine. J'ai fini la trempe
sélective dans le bac d'eau de refroidissement de la bobine
à environ 35°C.
J'ai remarqué que la pointe avait du mal
à devenir orange alors qu'elle est bien placée dans la
bobine (assez loin de l'extrémité). J'ai tenté de
le photographier sur la première photo ci-dessous mais
impossible. La tache un peu sombre à la pointe a une ligne
de séparation du reste de la lame qui est verticale... Exactement
comme sur toutes mes autres lames trempées par induction avec
des lignes de trempe devant la pointe indiquant qu'elle est beaucoup
moins dure... Et si ce n'était pas ma lenteur à sortir de
la bobine pour rejoindre le bac mais plutôt une sorte "d'effet de
bord" de mon montage? Mais qu'elle en est la cause? J'ai
espéré qu'un temps d'austénitisation d'au moins 10
min arrangerait les choses par conduction thermique du reste de la lame
qui rechaufferait la pointe.
J'avais mis des traces de crayons thermiques
à 774 et 804°C mais je n'ai pas réussi à voir
dans la bobine s'ils ont fondu. Impossible de savoir les
températures atteintes. Plus le temps passait, plus il semblait
y avoir des plaques noires sur la lame: de la calamine en plaque.
Peut-être que c'est cela que j'ai vu sur la pointe, puisqu'au
contraire elle doit chauffer plus vite que le reste de la lame.
J'ai fait des tests à la lime demi-douce
après chaque trempe: chaque fois l'acier semblait très
très dur! Il en fut de même pour le second couteau en
acier inconnu et supposé "pur" carbone.

Voici la position de la lame pendant l'auténitisation avant trempe intégrale.
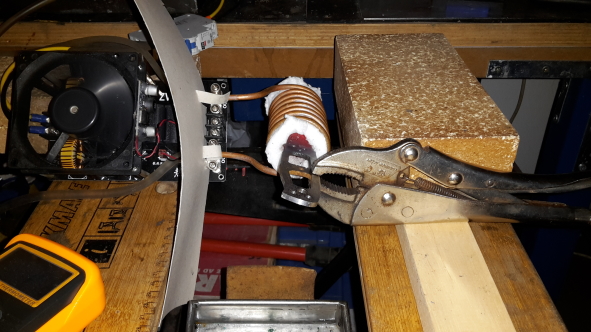
Voici la position de la lame pendant l'auténitisation avant trempe sélective.
On recommence avec le "Kegaska 2.0" forgé dans une lime avec 2.31 mm d'épaisseur de lame.
courant absorbé [A] |
Temps t=0 |
t=1 [min] |
t=2 [min] |
t=3 [min] |
t=4 [min] |
t=5 [min] |
température eau de trempe [°C ] |
durée austénitisation approx. [min] |
austénitisation 1 |
12.00 |
9.10 |
8.99 |
8.97 |
8.96 |
8.96 |
33.2 |
7 |
austénitisation 2 |
12.00 |
9.12 |
8.98 |
8.93 |
8.92 |
8.91 |
36.1 |
6 |
austénitisation 3 |
12.00 |
9.05 |
8.92 |
8.92 |
8.93 |
- |
39.3 |
4 |
austénitisation 4 |
12.00 |
9.00 |
8.96 |
8.95 |
8.94 |
- |
20.4 |
4 |
En effet sur cet acier le courant s'est
stabilisé beaucoup plus vite. Il semble donc (et c'est
élégant) que la stabilisation du courant (moins 0.01 A de
variation en 1 minute) indique également quand
l'austénitisation peut prendre fin puisqu'il n'y a plus la
moindre transformation dans l'acier.
Aucune casse, un acier très blanc à
chaque fois sauf en sortie de trempe sélective. Après la
première trempe il restait des traces de calamine sur
l'épaisseur du tranchant (trop vite refroidi avant d'atteindre l'eau salée?). La lame s'est
aussi tordue vers la gauche au niveau de la pointe après la
première trempe. Après chaque nouvelle trempe elle est
revenue progressivement vers la droite pour finir pile dans l'axe
après la dernière trempe, sélective. C'te chance!
J'ai fini la trempe sélective dans le bac d'eau de
refroidissement de la bobine à environ 39°C pour bien remonter la zone trempée vers le ricasso.
Pareil avec la lime demi-douce (d'la balle!), les
descentes à l'ambiante après chaque trempe.
Congélo à 15h56.
Sortie de congélo à 16h34 pour les
deux. Pour essayer ce fameux truc déjà vu très
souvent, j'ai plaqué la lame en 90MCV8 avec un serre-joint
(décapé) contre un fer plat afin de redresser la lame
pendant le revenu. Et en avant pour 60 min @ 150°C (lors des
derniers essais avec l'induction, les lames en 90MCV8 et 100Cr6 ont
perdu beaucoup de dureté pendant les revenus à 200°C;
j'ai décidé d'y aller progressivement)
En sortie du four trempe à l'eau de pluie
à 20°C. Avant même la trempe, je constate que la lame
du 90MCV8 a cassé nette pendant le revenu juste derrière
le serre-joint, la contrainte a dû être trop forte. C'est
rageant. Je continue avec ce qu'il en reste pour engranger de
l'expérience. Test à la lime demi-douce: les deux lames sont
extra dures. Pas de saut à 170..175°C, je mets le prochain
revenu directement à 205°C.
Retour au congélo à 17h40 et sortie à 18h28.
Nouveau revenu 60 min @ 205°C. Trempe eau de
pluie à 20°C en sortie, test lime demi-douce, toujours aciers extra
durs. Congélo à 19h41. Ma fille crie famine!
26-MAI-2020
Sortie des lames du congélo à 7h07,
fin des TTH. Je peux enfin vous faire une photo de la casse d'hier en
sortie du premier revenu. J'ai testé les duretés avec mes
lames de dureté connue, sans avoir enlevé la couche
supérieur de métal. Donc ces valeurs prennent en compte
une éventuelle décarburation qui a eu lieu selon moi
quand on voit la quantité de calamine au fond des bacs de
trempe. Le 90MCV8 ne se laisse pas rayé par le Lauri à 63
HRc. Même dans le dos de lame il a du mal à mordre (normal
ce truc trempe grave à l'air), on est sans doute vers les 62
HRc. Pour l'acier issu de la grande râpe, on est vers 62 HRc
au tranchant et le dos se laisse entaillé par mon Yakitori de
cuisine en 1.4116 donné pour 55 HRc. Au feeling on a l'air bien
en dessous, 50 HRc peut-être? Par rapport au patron de
départ, le dos de lame et la pointe n'ont pas bougé
sur le 90MCV8. Sur l'autre acier inconnu, la première
moitié du dos de lame est remontée d'environ 1 mm. Il est
vrai que le 90MCV8 est réputé pour rester
dimensionnellement stable après trempe.
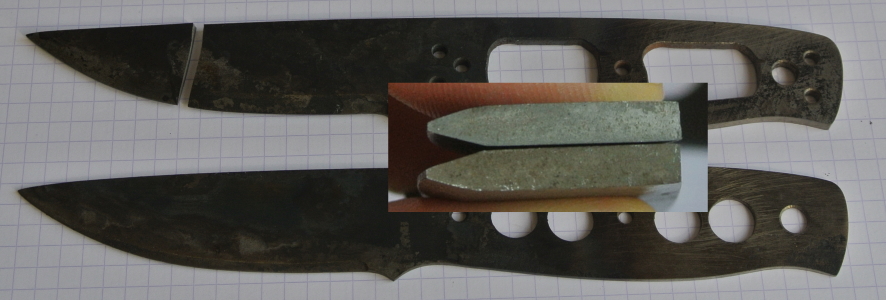
La cassure est perpendiculaire au tranchant. Hasard? Le grain est
plutot très sympa. La partie la plus claire est la pointe qui a
subi un seul revenu à
150°C tandis que la lame ayant subi le second revenu à
205°C est plus brune. Le fameux jaune des revenus vers
200..230°C?
J'ai l'impression
que le 90MCV8 et les purs carbone type XC100 sont de bons candidats
pour des trempes simples et faciles à l'induction. Sans doute
impossible d'avoir 65..66 HRc après trempe, mais avec 0,6..0,7%
de carbone dans l'austénite on obtient sans doute des
duretés plus qu'élevées tout en ayant une
très grande résilience.
Il faut sans doute oublier les trempes
sélectives. Seules des trempes intégrales hyper rapides
sans contrôle précis des gestes me donnent des aspects
blanchâtres de lame dont je pense que les trempes sont les plus
complètes. Il faudra plutôt se concentrer sur des revenus
sélectifs du dos de lames après deux revenus
intégraux au four de cuisine. Plus de contrôle, moins de
risque de casse et de déformation, trempe plus complète.
Eventuellement faudra se procurer un chalumeau. Ma lampe à gaz
ne concentre pas assez la chaleur pour les revenus sélectifs.
Je pense rester avec de l'eau saléée
à 10% pour les "purs" carbone. J'ai l'impression qu'avec le
90MCV8 austénitisé au moins 10 min, l'huile de colza vers
50..70°C fera l'affaire aussi. Avec tant de manganèse et de
chrome, le nez perlitique est si loin que ça devrait durcir. Je
pourrai tester à la lime et si je vois que ça prend
moins, toujours revenir à l'eau pour les autres trempes.
Peut-être que le 100Cr6 meriterait un dernier
essai avec un temps d'austénitisation de 15 min. Toutes les
rares courbes et données que j'ai pu trouver, même
avec la meilleure microstructure avant austénitisation indiquent
des temps relativement longs.
28-MAI-2020
Arrivée du vernis/de la peinture contre la
décarburation et les quelques aciers de chez Eurotechni. Le
xylène pour le nettoyage du pinceau était là aussi
mais sans la moindre annonce par mail. Equipé!
Petite remarque: voilà déjà
deux commandes de 135Cr3 en 3 mm que je fais avec à la
livraison du 130CrV3 qui arrive. Par contre, le plat de 6 mm est bien
noté 135Cr3 à la reception. Alors en soi, ce n'est pas
grave, je dirai même qu'à choisir, la pointe de vanadium
en plus (0.08% pour une valeur nominale de 0.1%!) en échange des
0.05% de carbone en moins ne fait pas de mal, bien au contraire mais ce
ne sont pas les mêmes aciers selon la norme et on vous livre donc
autre chose que ce que vous avez commandé. Pas bien ça.
Et deuzio, si tu commandes des stencils avec inscription 135Cr3 en
parallèle et que te voilà avec du 130CrV3, pas glop non
plus, du moins si t'es un peu maniaque comme moi.
03-JUN-2020
Aujourd'hui j'ai repris au backstand les
émoutures des deux "Kegaska 2.0". Le brisé en 90MCV8
aussi pour explorer le concept jusqu'au bout. J'ai recalé la
table horizontale à 14° et comme d'habitude, je n'ai pas
réussi à faire des émoutures symétriques.
La faute à mon inclinomètre, car une fois la table
horizontale à 0°, la table verticale n'est pas à
90° par rapport à la table horizontale. Donc au lieu de
faire des émoutures à 14°, elles sont plutôt
à 16 ou 12°, etc. J'avais fait des tracés pour y
aller à taton mais cela n'aura pas suffit. Par contre, la
dissymétrie n'est pas catastrophique et pas handicapante du
point de vue fonctionnel.
Chaque face a été passée au
P60, 120, 220 puis 400. Fier de moi, le métal n'a jamais pris la
moindre coloration. On continuera avec des reprises à la main.
04-JUN-2020
Le soir j'ai repris sans gros zèle les faces et émoutures à la main
- au P120, 180, 220, 320 et 400 sur une face du "Kegaska 2.0" en 90 MCV8 et P400 sur l'émouture
- puis avec le recul, l'autre face au P120, 180, 220, 320 et 400 et P320 +400 sur l'émouture
- et avec le retour d'expérience, les deux côtés du
second "Kegaska 2.0" à P80, 120, 180, 220, 320 et 400 avec P180,
220, 320 et 400 sur l'émouture
06-JUN-2020
J'ai repris les deux "Kegaska 2.0" à la main
au P400: plats et émoutures. Bien que j'ai prévu de
les attaquer au perchlo, j'ai poli les lames aux disques
sisal, coton et flanelle avec pâtes respectivement
noire, verte et blanche. Puis j'ai fait tiédir du perchlo
au micro-ondes avant d'immerger les lames deux fois deux minutes, avec
neutralisation et petit polissage à la paille de fer. La ligne
de trempe sur l'acier de la lime est plus marquée que sur le
90MCV8 où elle est presque invisible: toute la lame semble
trempée malgré la trempe sélective.
L'après-midi j'ai gravé les logos suivi d'un petit polissage au P2500 et à grande eau.
07-JUN-2020: bonne fête Maman!
J'ai fait des plaquettes pour chaque "Kegaska 2.0"
- pour celui en 90MCV8, à partir d'une chute de 19 mm de MDF
teinté noir pleine masse, avec une densité de 0.777. Je
la gardais depuis longtemps. C'est le moment de faire un essai sur un
couteau sans pointe, à la semelle parfaitement plate
- perçage des 3 trous à 3 et 6 mm avec la semelle servant de guide,
- reperçage en surcote de 0.1 mm (3.1 et 6.1 mm)
- tracé du contour, dégrossissage à la scie à ruban
- coupe en deux à la scie à ruban
- rectification des faces à encoller à la main sur miroir et papier abrasif P60
- pour l'autre avec des chutes FTFI de buis
- tentative de faire des plaquettes aux faces
parallèles avec le rabot électrique sous ma
dégauchisseuse
- rectification des faces à encoller à la main sur miroir et papier abrasif P60
- perçage des 3 trous à 3 et 6 mm avec la semelle servant de guide pour les deux plaquettes,
- reperçage en surcote de 0.1 mm (3.1 et 6.1 mm)
- tracé du contour, dégrossissage à la scie à ruban
- finition des faces avant sur les deux jeux
- arrondi au mini backstand Peugeot
- chanfrein à 35° sur le mini lapidaire Peugeot
- finition à la main des faces avant et chanfreins: P120, 180, 320 et 400,
- puis polissage disque coton et pâte spéciale bois 40 microns
- dégraissage et décirage des surfaces
- préparation et enduction d'époxy à prise lente et progressive
- montage sous presses légères (sur le 90MCV8 pour ne pas
chasser toute la colle; sur l'acier de lime pour compenser les
défauts de planéité et remplir les jours)
- nettoyage des excès d'époxy au ricasso
- retrait des rivets de mise en place
08-JUN-2020
Profitant de mon jour de chômage partiel
pour faire des courses, j'ai acheté un petit couteau de chef de
17 cm (vendu pour 20 cm) que je compte customiser
- c'est encore un Tarrerias-Bonjean de Thiers
- inox, forgé
- le tranchant neuf a de petites entailles par endroits, malgré la protection de l'emballage
- j'ai mesuré la position de la "ligne" d'épaisseur 0.5
mm, elle est a à plus de 3 mm derrière le tranchant:
ça c'est de l'émouture fine qui va trancher!
- à la loupe le tranchant semble avoir été fait entre P120 à P180
- je l'ai mesuré d'une largeur de 0.5 mm avec une
épaisseur de 0.3 mm soit un demi-angle au sommet d'environ
Arctan (0.15/0.5)=16.6°; on est plus proche des 15 que des 20°
- ça coupe mais sans plus, faudra affûter et ça roulera ce truc.
- en le cherchant sur le site Tarrerias, on ne le trouve pas tout de suite mais on
trouve une gamme, aux gardes différentes, très similaire.
Il y est indiqué 56 HRc acier Nitrox "maison" avec 0.35% de
carbone, 16 de chrome et dopé azote (ce qui explique l'obtention
des 56 HRc après revenu malgré le bas taux de carbone).
Je pense que le modèle de la grande distribution est en inox
plus classique (et moins cher) type X46Cr16, Z50 ou 55 CrMoV14 ou 15...
- puis en cherchant parmi tous les couteaux de chef, on le
découvre, exactement celui là,sous la
référence 446740, avec garde et mitres identiques.
Pas la moindre indication sur l'acier ou la dureté.
L'après-midi j'ai percé les rivets des
plaquettes en polypropylène du couteau de chef de 17 cm pour
pouvoir les démonter. Il y avait encore d'autres fixations
surmoulées, ultra solides. De la très bonne came solide
ce truc. J'ai collé deux planchettes de 5 mm de noyer et
d'acajou pour en faire la matière d'oeuvre pour les futures
plaquettes.
Pour finir, sortie des presses des deux "Kegaska
2.0" pour façonner les contours au back et cylindre pneumatique
Kirjes (encoche façon mini garde pour l'index): P60, 120, 220 et 400.
09-JUN-2020
Sortie du sandwich noyer acajou des presses. J'ai
mesuré les divers trous dans la semelle du TB
(Tarrerias-Bonjean): 4, 4.1, 4.2 et 6 mm. Je me suis
décidé à reprendre les efforts de cisaillement
avec deux tourillons en bois de 6 mm montés à l'aveugle
et de mettre 3 rivets inox (de 3.85 mm; récup de tige inox d'une
vieille grille de four) pour l'esthétique, seulement
collés.
Le raccord entre semelle et mitre est en arc de
cercle avec un angle obtus de 105°. Pas facile. J'ai cependant
réussi avec le petit lapidaire du petit combiné Peugeot
incliné à 15° à y faire à main
levé un arc de cercle qui épouse bien le contour (un gros
rouleau de ruban adhèsif avait le bon diamètre que j'ai
reporté au crayon). Préparation du tourillon (sciage,
chanfreinage), égrénage des surfaces, dégraissage,
décirage, perçage des trous borgnes de 6 mm dans chaque
plaquette, colle à bois type D3 pour les tourillons,
époxy à prise lente et collage de la première
plaquette avec les 2 tourillons et mise sous presses fortes.
Ensuite j'ai façonné les contours
grossiers des deux manches des deux "Kegaska 2.0" à main
levée et au back à P60 et P120 (après des
tracés pour m'aider visuellement). Faudra finir à la
main. Le MDF semble trop peu résistant pour faire un bon manche.
Ça ne résiste pas assez à l'abrasion...
N'empêche que le Elver avec 4 mm de lame de plus, c'est
plutôt joli et équilibré dans les proportions.
10-JUN-2020
La suite du TB de 17 cm...
- sortie de presse
- affinage du contour de la plaquette déjà collée à la scie à ruban
- perçage des 3 trous de rivets à 4 mm de ladite
plaquette (la semelle a des trous oblongs de 4.1 et 4.2 mm de largeur
à ces endroits)
- dégraissage, décirage des surfaces
- époxy pour la liaison bois métal et colle à bois
type D3 pour la liaison tourillons acajou de la seconde plaquette
- mise sous presses fortes la seconde face de la semelle ayant un défaut de planéité
A la tombée de la nuit, j'ai repris à
la râpe et à la lime demi-douce les manches des deux
"Kegaska 2.0". Autant il faut un peu de patience avec le buis, autant
le MDF n'oppose pas la moindre résistance à l'abrasion.
Il faut faire très attention de ne pas enlever trop de
matière d'un seul coup.
11-JUN-2020
La suite du TB de 17 cm...
- sortie de presse
- affinage du contour de la seconde plaquette à la scie à ruban
- contre-perçage des 3 trous de rivets à 4 mm de la seconde
plaquette
- descente du contour des plaquettes au niveau de la semelle avec le back
- descente de l'épaisseur des plaquettes de 10 à 8.5 mm
comme sur le couteau d'origine: un trou parfaitement cylindrique est
apparu dans le noyer de la plaquette droite (?!) entre le premier et le
second rivet.
- petite pente d'une dizaine de degrés sur les champs (comme sur l'origine aussi)
- dégrossissage au back
Il reste du boulot.
12-JUN-2020
J'ai continué les retouches du TB 17 cm au
back à la bande de P800 (liège). Il aurait
été plus judicieux de faire un montage à blanc des
plaquettes et de les coller une fois retouchées et toute la zone
de la garde polie définitivement. J'essairai de m'en souvenir.
Ici il faudra sans cesse polir la garde, retoucher les plaquettes,
retoucher la garde et ainsi de suite. J'ai coupé 3 rivets inox
(qui ne seront pas matés) et je les ai collés à
l'époxy. Il reste encore du boulot de finition. Je songe
à une petite protection de tranchant en bois avec aimants de
rétention.
Reprise à la main des manches des "Kegaska
2.0": P80, 120, 180, 320, 400 et 600. Polissage au disque coton et
pâte spéciale bois 40 microns (pour le buis il restait des
rayures et j'ai dû revenir par deux fois aux abrasifs).
Nettoyage au décireur. Il faut définitivement rayé
le MDF des matériaux pour plaquettes: trop mou, marque
très vite, ne prend pas un beau poli. Exit. Been there, done
that.
13-JUN-2020
J'ai coupé, aplani, ébavuré la
quincaillerie pour faire les rivets et les tubes de passage dragonne
des deux "Kegaska 2.0" tout en étant obligé de
repassé les trous à 3.1 et 6.1 mm dans l'acier de
râpe, semelle comprise et seulement les plaquettes sur le 90MCV8
(mais c'est sans doute dû à un forêt de 6.1 mm HS
plus qu'à une trempe partielle de la semelle) avec un accident
sur une plaquette MDF endommagée. J'ai aussi fait les chanfreins
à 45° sur les trous.
15-JUN-2020
J'ai maté la quincaillerie laiton sur les
deux "Kegaska 2.0" puis je l'ai poncé à ras ainsi que
celle en inox du TB de 17 cm au backstand. Il faut encore tout
reprendre à la main.
16-JUN-2020
Reprise à la main au P180, 320, 400 et 600
des zones autour des rivets des deux "Kegaska 2.0". Nettoyage au
décireur puis polissage au disque coton et pâte 40 microns
spéciale bois avec second nettoyage au décireur. Le buis
du second est plus veiné que d'habitude pour cett essence, c'est
joli, mais il a une fissure près du riccaso sur la plaquette
droite. Si j'avais encore de la cyanoacrylate en stock, j'y mettrai
p-ê un petit coup. Mais j'ai envie de passer à l'huile de
finition et de classer ces projets qui n'ont pas suivi le programme que
j'avais en tête pour eux.
J'ai repris à la main les plaquettes du TB de
17 cm puis aussi toute la garde, une vraie cochonnerie à polir,
sans arriver nulle part.
17-JUN-2020
J'ai préparé un peu d'époxy
(Araldite 90 secondes) pour boucher les fissures dans le buis du
"Kegaska 2.0" et collé un petit bout de cuivre issu d'un fil
électrique de 1.5 mm
2 dans le trou de la plaquette en
noyer du TB 17 cm: c'était exactement la taille. Afin de ne pas
polir une énième fois de plus le buis, j'ai essuyé
les excès d'époxy à l'acétone mais sans
réussir à combler les fissures à ras.
Une fois l'époxy prise,
- aux limes j'ai ramené le petit bout de fil de cuivre au niveau de la plaquettes
- et j'ai passé les 3 couches d'huile de tung
diluée ainsi que la première couche d'huile pure sur les manches des deux "Kegaska 2.0": le MDF absorbe
énormément tandis que le buis semble déjà
imperméable.
Reprise de la garde du TB 17 cm à la main,
puis polissage ainsi que la lame (manche protégé par
ruban à masquer) aux divers disques polissoirs, si souvent
cités ici que ça doit finir par gonfler mon imaginiare
seul lecteur fidèle (qui que tu sois, merci!). Gravure du logo
IMC.
Ensuite j'ai découpé 3 pièces
en noyer, acajou et samba pour en faire une sorte d'étui
censé protégé le tranchant du TB 17 cm. Ajustage
du contour avec le petit back Peugeot et premier collage avec mise sous
presses du martyr en samba sur la plus grande plaque en acajou.
Perçage diamètre 4 mm sur 0.5 mm de profondeur à 4
endroits afin d'y noyer 4
petits aimants collés à la colle forte.
18-JUN-2020: Général nous voila! :)
Enduction des deux dernières couches d'huile de tung pure sur les manches des deux "Kegaska 2.0".
Collage de la seconde plaque en noyer et
façonnage (au petit backstand) du protège-tranchant du TB
17 cm. Arrondi des angles (Back + P60 à la main), polissage
(main P100, P180, P320 et disque coton+pâte), nettoyage au
décireur, enductions multiples à l'huile de tung
diluée et pure. L'acajou a très soif mais pas tant que le
MDF!
Suite et fin du façonnage à la main
(jusqu'à P600 à cause de la semelle) du manche du TB 17
cm. Décirage, polissage et premières couches d'huile de
tung diluée.
19-JUN-2020
De passage chez Casto pour une bricole
électrique chez mes parents, j'ai pris une lime ronde
demi-douce de leur marque maison Magnusson, Mac Allister, une
chinoiserie, mais trop mal. Diamètre 7 mm.
21-JUN-2020
J'ai passé deux couches de cire de cranauba
sur les 3 manches et le protège-tranchant en souffrance et
en sus deux couches de cire d'antiquaire sur les deux manches des
"Kegaska 2.0".
J'ai rattrapé les ébréchures du
TB de 17 cm avec les pierre à eau Haïdu P180 et 280 avant
un dernier passage à la DMT 45 microns avec finition cuir et
pâte 2 microns. Pour les deux "Kegaska 2.0" il aura suffit de
blanchir les émoutures à la pierre de coticule avec un
micro tranchant à la DMT 45 microns (2 passes
légères à ~25°) et passe de finition au cuir
avec pâte 2 microns. Mesures et photos et ce sera fini pour ces 3
candidats.
22-JUN-2020
Mise à jour de la galerie, prise de
caractéristiques: le "Kegaska 2.0" forgé dans une lime
est plutôt vers 60 que 62 HRc. C'est à partir du
Fallkniven F1 à 59 HRc que ça patine et le Enzo Trapper
à 60..61 HRc mord.
23-JUN-2020
Tiens je m'aperçois que je n'avais pas fini
le dos des deux "Kegaska 2.0" alors qu'ils sont déjà aux
oubliettes muséales. Bon ce sera fait à l'occasion d'une
prochaine sortie du backstand.
En panne de cyanoacrylate, j'ai fait une commande
Amazon pour 50 g en viscosité moyenne (100 centipoise) pour
usage général.
Aujourd'hui c'était pas chômage partiel
mais fête nationale là où je travaille.
Malgré moultes taches incontournables, un peu de temps pour moi.
Alors pour une fois je me suis fait un peu d'expérience avec le
"edge flex test" des US: on incline un tranchant perpendiculairement
à la génératrice d'une tige (souvent du laiton de
6.35 mm) et on regarde: ça plie, ça revient, ça
casse etc. En gros si ça casse on est trop dur, si ça
plie et que ça reste ainsi, c'est évidemment tellement
mou que c'est pas trempé et si ça revient, on
déclare le TTH OK pour un couteau. Bref je vous parie qu'on peut
plier et laisser revenir entre 45 et 65 HRc. Tout est question de la
force avec laquelle on appuie, de la finesse du tranchant, de sa
géométrie, etc. Mais je crois que c'est un bon exercice
à répéter pour pouvoir se situer et avoir un
certain feeling.
Alors j'ai passé une grande partie du
tranchant de mes dernières réalisations sur une tige de
laiton d'environ 7 mm de diamètre, en inclinant de plus en plus
la lame et en poussant de plus en plus fort jusqu'à ce que
quelque chose se passe, mes yeux étant équipés de
mon espèce de loupe avec serre-tête
- "Kegaska 2.0" en 90MCV8 scandi zéro à 32° et au
moins 63 HRc: au delà d'un certain point, le tout petit sommet
du tranchant plie et fait une bavure à peine perceptible. A deux
endroits voisins j'ai pu faire deux ébréchures de 0.15 mm
de profondeur mais sans que le métal ne se détache
- "Kegaska 2.0" en lime forgée scandi zéro à 31° et environ 60 HRc: au delà d'un certain
point, le tout petit sommet du tranchant plie et fait une bavure à
peine perceptible. Aucune ébréchure.
- "Caplan" en 100Cr6 forgé tranchant 0.5 mm convexe à
~30° et environ 61 HRc: rien à faire ça ne bouge pas
- "Bujeault 106%" en 100Cr6 forgé tranchant 0.5 mm en vé
à ~30° et environ 58..59 HRc: rien à faire
- "Bujeault 107%" en 90MCV8 forgé tranchant 0.5 mm en vé
à~ 30° et environ 60..61 HRc: rien à faire
- "Gadois 2.0" en lime forgée tranchant 0.5 mm en vé à ~34° et au moins 63 HRc: rien à faire
- "Matané" en ressort Mazda forgé tranchant 0.65 mm
convexe à ~36° et environ 61 HRc: rien à faire,
indestructible
- "Maskinongé" usiné en disque à tronçonner
le bois tranchant 0.4 mm en vé à ~26° et environ 62
HRc: j'ai fait les ébréchures les plus faciles, avec une
jolie répétabilité
- "Couchepaganiche" en lime Facom forgée tranchant 0.5 mm en
vé à ~40° et au moins 63 HRc: rien à faire
- "Caplan" en lime Facom forgée tranchant 0.3 mm en vé
à ~30° et au moins 63 HRc: j'ai réussi à plier
le micro sommet du tranchant
- pour vérifier, j'ai pris la réplique du Mora Companion
vendu par Bahco avec émouture scandi zéro, 12C27
laminé entre deux couches d'inox, estimé à 56..57
HRc: très facile de plier plastiquement le sommet du tranchant.
Conclusions? En fait rien de nouveau sous le soleil,
juste un peu d'entrainement. Plus c'est dur, plus c'est haut en
carbone, plus c'est fin, plus l'angle est aigu, mieux on arrive
à déformer ou ébrécher le tranchant. Si
c'est épais et/ou convexe cela devient vite impossible.
Même les couteaux du commerce avec des duretés
conservatrices, de gros angles, des aciers résilients suivent
les mêmes lois, avec notablement moins d'effort. Bref mes
couteaux n'ont rien de différents des autres, les aciers suivent
bien les lois de la physique et des TTH qu'ils soient
transformés en couteaux par les meilleurs ou votre humble
serviteur. J'ai surtout pu me jauger la main et les efforts
nécessaires pour les déformations et par comparaison au
Mora, je trouve mes réalisations plutôt très
résistantes. Suis content.
Les tranchants endommagés ont
été corrigés avec une pierre de coticule. Les
tranchants sont revenus très très vite avec une mention
spéciale pour le 90MCV8 du "Kegaska 2.0".
24-JUN-2020
Je me suis servi de l'étui de mon Enzo
Trapper pour dessiner le patron un peu raccourci d'un étui pour
le "Kegaska 2.0" en lime forgée. Je vais utiliser le même
cuir de mon vieux cartable que celui qui a servi pour faire
l'étui du dernier "Caplan" en 100Cr6. Il trempe dans l'eau pour
le ramollir et en sortir les plis des soufflets depuis ce midi.
25-JUN-2020
J'ai sorti le cuir de l'eau le matin et je l'ai mis
sous des pavés toute la journée sous la cagnard. Le soir
j'ai découpé l'étui et le martyr. J'ai
percé quelques trous, creusé 3 rainures pour le pli, préparé certains angles avec
l'abat-carre et teinté certaines zones.
26-JUN-2020
J'ai revu un duromètre Leeb (à rebond)
chinois sur ebay... C'est cher, mais infiniment moins qu'un
pénétrateur. J'ai bien envie de craquer...
La suite de l'étui du "Kegaska 2.0".
- Marquage des trous de couture du passant de ceinture,
- perçage, grattage, replis
et collage du passant.
- Contre-perçage et creux autour des
trous afin de noyer le fil.
- Collage du martyr et façonnage du
demi-contour au petit back Peugeot.
- Creux pour la couture d'un seul côté, marquage des
points à la roulette, perçage des points, collage/fermeture de l'étui,
- réouverture de l'étui car j'ai oublié de coudre le passant!
- Couture du passant (point sellier),
- second collage/fermeture de l'étui, contre-perçage des trous de couture dans le martyr,
- égalisage de la tranche avec
le back, chanfreins et arrondi des angles (ce vieux cuir sec au tannage chimique ne s'y prête guère).
- Nouvelle rainure de l'autre côté
pour noyer le fil, teinte des zones restées claires.
- Couture du martyr avec point sellier...
Et voilà!
S'il n'y avait pas la douloureuse étape de couture à la
main, ce serait presque sympa le travail du cuir...
27-JUN-2021
Petites couches de crème et graisse pour cuir
sur le dernier étui. Massage, pénétration, repos,
essuyage, lustrage. Enfin fini.
30-JUN-2020
Dans un moment de faiblesse, j'ai craqué...
Puisque la dureté c'est l'alpha et l'omega pour juger des
résultats de mes TTH, j'ai commandé sur ebay en Chine un
duromètre Leeb (à rebond!). Hyper bon marché par
rapport à un classique Rockwell mais cela reste une
sacrée somme pour un amateur. Ne vais-je pas le regretter?
Ça en ferait des mètres de Damas inxo ou même
de Wootz d'Achim Wirtz pour ce prix.
03-JUL-2020
Une petite découverte aujourd'hui. Ces
derniers temps j'étais plutôt insatisfait de
l'affûtage de mes dernières lames. Impossible de
retrouver le mordant que j'aime tant avoir, quelque soit les outils
utilisés. Pour changer, j'ai sorti ma pierre Norton IB-134 et
comme je n'avais rien sous la main, j'ai pris dans ma cuisine mon huile
IKEA Skydd (pour planche à découper). La pierre est
censée être remplie d'huile d'origine mais c'était
il y a plus de 20 ans. Du coup je me suis dit qu'il était temps
de lubrifier... Le tranchant est devenu super agressif avec la face
India "fine" indiquée par Norton comme P400. J'adore! Comme
j'aime! Du coup j'ai refait l'expérience avec tous mes derniers
couteaux et ce fut le même résultat à chaque fois.
Bref, l'ajout de lubrifiant semble indispensable pour obtenir le
maximum d'une pierre Norton. En plus cette huile nourrit le bois des
manches. Que demande le peuple?
04-JUL-2020
J'ai encore affûté une vingtaine de
couteaux récents (et mes couteaux de cuisine) avec la pierre
"Fine" India (P400) Norton de ma IB-134 et l'huile minérale IKEA
Skydd. Toujours le même résultat hyper agressif quels que
soient l'acier, la dureté, le procéde d'obtention.
Même pas de passage au cuir, juste 2 passages par
côté avec le seul poids du couteau sur la céramique
(P600) de la Fallkniven DC-4 avec environ 5° de plus. Et
voilà, équipé et paré!
07-JUL-2020
J'ai construit un petit support en bois pour ma
pierre Norton IB-134, avec un morceau de planche de pin qui accompagne
les livraisons de plats Eurotechni, des bâtons de glace et un
vieux gant de vaisselle (pour la face anti dérapante)
08-JUL-2020
Samedi y a forge associative de 9 à 16. J'ai
prévu de redresser un ressort de 8 mm afin d'en faire un axe
pour réparer ma pompe à pied bicylindre Michelin made in
China qui a rendu l'âme: comme toujours, les axes trop petits ont
usiné des trous oblongs dans les tôles latérales
trop fines. Dur de trouver du matos de qualité (ou alors mettre
une étiquette près des axes avec la mention "oil
frequently"). J'ai aussi l'intention de tremper ma plane (voir en date
du 29-FEV-2020), en suspend depuis. Je veux profiter du foyer au
charbon pour ne tremper que le corps central. Alors ce soir j'ai
ressoudé à l'arc et électrode rutile la branche
qui était cassée... Sauf que comme j'avais
oublié mon masque chez mes parents, j'ai soudé les yeux
fermés. Déjà que je suis nul en soudure, vous
imaginez la petite saynète...
Bon faudra encore trouver autre chose à faire...
09-JUL-2020
Fausse alerte pour samedi. Pas de forge
prévue, juste du rangement et du nettoyage, bref le boulot
associatif quand il faut des bras... Cela veut dire que je vais sortir
ma forge pour réparer ma pompe et peut-être essayer de
tremper la plane.
Voilà plusieurs semaines qu'il traine de
vieilles fenêtres devant une maison rénovée du
village. Sur un vieux site (belge je crois) dont j'ai malheureusement
oublié le nom, il était dit que les montants de
fenêtres (en bois!) font de bons manches car souvent en bois
tropical très stable. Aujourd'hui j'ai enfin croisée la
propriétaire qui m'a gentimenet autorisé à prendre
tout ce que je voulais. J'ai juste pris un montant, bien droit et
plutôt dur. Impossible de reconnaitre l'essence. Je demanderai
à une connaissance.
14-JUL-2020
Si si je bosse aujourd'hui... Voilà plusieurs
semaines que ma dernière pompe à pied (une bicylindre) de
marque Michelin mais made in China m'a laché. 45.90 EUR le
03-JUN-2011. Un bon manomètre précis, un excellent embout
à visser, toujours étanche mais le tout monté sur
des tôles pas assez rigides maintenues par des tiges aux
extrémités embouties.Des patins caoutchouc troués
à force. Je me sers beaucoup de ce type de pompe pour les
voitures, les motos, les vélos. Cette fois c'est l'emboutissage
d'une extrémité de l'axe de rotation qui s'est
frayé un chemin dans la tôle. On a beau parcourir les
magasins ou le Net, y a plus que des pompes de qualité
merdique, visible à l'oeil nu. Même pas un truc cher mais
haut de gamme.
J'avais offert le même modèle mono
cylindre à mon frère. C'est le flexible qui est vite
devenu poreux alors que le mien est en excellent état. On avait
remédié au problème avec du
ruban adhésif d'électricien, très efficace,
mais récemment c'est le ressort qui a cassé.
Ma meilleure pompe à pied date de
l'époque des francs, 259, la plus chère chez Norauto,
marque Orex, made in Germany, très bon mano, flexible
tressé. L'embout était vite devenu non étanche
mais un collier et un nouvel embout pro plus tard, c'était
reparti. Tôle deux fois plus épaisse que la Michelin,
pieds en caoutchouc qui n'ont jamais été percés
par les pattes mais un jour l'extrémité du ressort a
cassé. Réparé à chaud (car il manquait
quelques millimètres), au final c'est aussi l'axe qui a fini par
me faire un trou oblong et une portée ovale. Je l'ai encore et
elle attend patiemment une réparation. J'ai compté sur un
tourneur qui m'a hélàs oublié (volontairement
j'imagine, c'est pas faute d'avoir demandé 4 fois par an pendant
5 ans, si si!)
Devant l'impossibilité de trouver une
remplaçante, j'ai essayé de réparer la bicylindre
à l'africaine et pas selon les règles de la construction
mécanique made in Arts et Métiers. J'ai refait à
la forge un grand axe de 8 mm dans le fil d'un ressort que j'avais et
repercé tous les trous de 5 et 6 mm à 8 mm. La tôle
est toujours aussi fine mais je lubrifierai avant chaque usage et
ça devrait nous refaire au moins 5 ans. Encore deux rondelles M8
pour caler le jeu latéral et je pense que je ne ferai même
pas de butée à chaque extrémité
(déformation plastique d'un côté et filetage M8 de
l'autre) tant l'axe dépasse. On va voir. Je vous ferai une
petite photo à la fin.
15-JUL-2020
Comme la forge était encore sur
l'établi, j'ai tenté de tremper la plane dont j'avais
ressoudé une branche récemment. J'ai ouvert la porte de
la forge, posé des briques réfractaires pour conserver la
chaleur le plus à l'intérieur possible et mis le
débit de gaz au mini pour chauffer lentement est
uniformément.
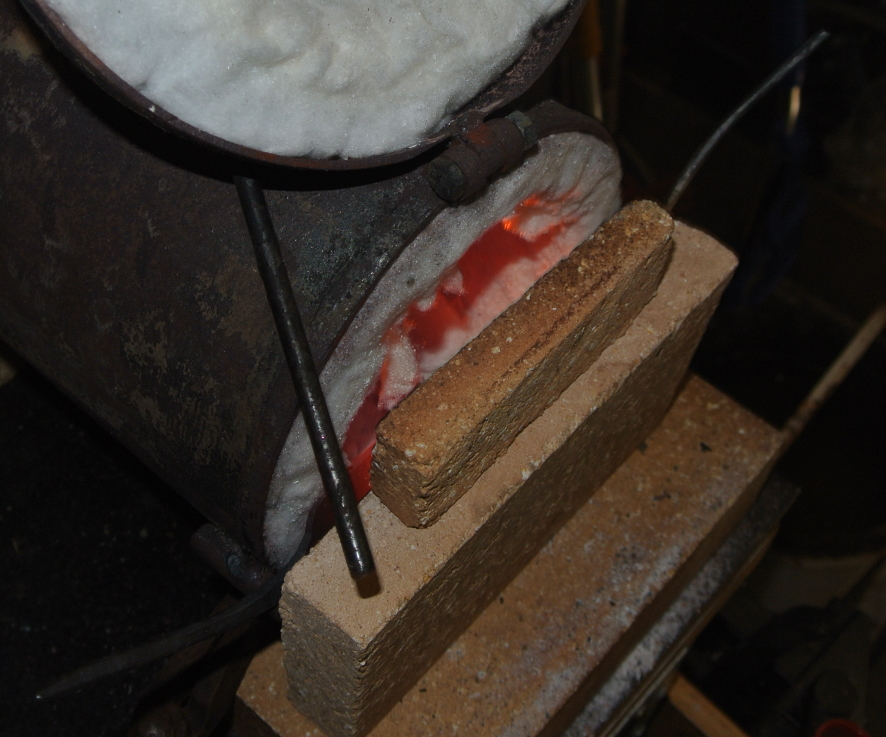
C'est le mieux que j'ai pu faire comme photo dans le noir (pour voir les couleurs). On devine la plane en voyant les branches.
Les branches sont
restées bien noires. Trempe à l'eau de pluie vers
23°C sans le moindre bris. Faut dire que j'avais laissé de
la matière, presque 2 mm au tranchant. Test à la lime
demi douce: super! Grattage de la calamine et j'ai fait deux revenus
devant l'entrée de la forge avec le dos vers le foyer. Pour le
premier j'ai eu un beau jaune paille ou or selon les zones au
tranchant, le second c'était bleu gorge de pigeon de partout. La
lame s'est un peu courbée. On verra si je tape dessus ou pas. Je
suis déjà très content que la trempe ait prise et
que les branches soient encore en place.
.